Investment pays off
This year the logistics industry has continued to face a perfect storm – demand for online shopping has remained high driving requirements for additional storage but at the same time a lack of suitable warehousing space means moving wasn’t always possible. On top of this rising costs have hit businesses hard.
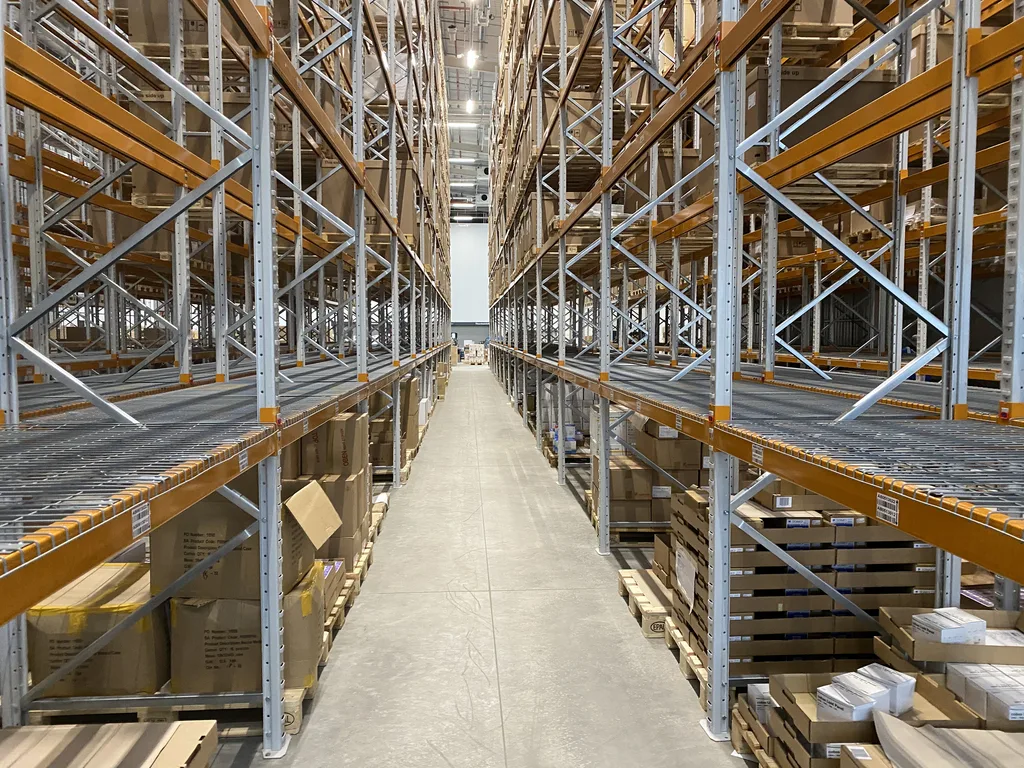
YOUR WAREHOUSE space is an expensive commodity, and you need to evaluate how your assets can deliver a maximum Return On Investment (ROI). As the backbone of your warehouse, your storage equipment needs to deliver across an interrelated matrix of different requirements. The criteria include a safe working environment, maximise your storage capacity, improve on efficiencies, reduce damage to stock and deliver on longevity of the equipment.
Maximise racking
SEMA manufacturing members and SEMA Distributor Companies (SDC) understand the complexities of the warehouse and can offer unparalleled knowledge to supply a solution that meets your requirements. They can also ensure you meet all the important legal and health and safety responsibilities that are associated with racking.
Every warehouse is unique and an experienced designer like our SDCs use their technical knowledge to design a bespoke racking solution which considers all the variables and uses various types of racking or shelving to maximise your cube.
Getting the balance right between storage and frequent order accessibility means analysing the number of product lines, how they are stored and the rates at which they move through the warehouse. It should also identify how your stock is picked, whether it is manually, automatically or a mixture of both. Where can you increase your storage capacity – reducing aisle widths, doubling the racking depth, increasing the height of your storage or even adding additional space with mezzanine flooring. Finally, it will consider the future, how will your needs change and is your racking flexible enough to adapt.
Quality
When choosing your racking, view it as an investment. Yes, the optimum design will enhance operations and maximise your space, but it should also encompass the lifetime of your racking. How is it being used and is it the right product for the job.
Get assurances by asking for proof of your supplier’s credentials. One advantage of buying from SEMA Full or Associate Members is that their products are subjected to meticulous and independent assessments. This guarantees that the storage equipment has been designed by a structural engineer to SEMA Codes. Its structural integrity and rigidity are calculated to meet precise criteria under specified conditions, to accommodate heavy loads.
As you maximise the cube and fit in more storage capacity you need to be aware of the challenges of installing new or dovetailing equipment to your existing structure. The approach requires a significant level of technical knowledge to uphold the integrity and safety of your storage system.
Do you know if your installer has used the correct number and type of floor fixings, that the racking is correctly lined and levelled and that all fixings are positioned and tightened to manufacturers’ tolerances? Getting anything wrong at this stage could greatly impact on not only the safety of system but it also contributes towards the longevity of the equipment.
Get the work undertaken by companies such as our SEMA Approved Installation Companies who can clearly demonstrate, through an independent audit process, that the quality of their work meets SEMA’s high standards.
Warranty
Maintaining high installation standards is especially important when adding equipment into your existing system. Any alteration work by an unverified company could have a dramatic impact on the manufacturer’s warranty.
Our SDCs and SAICs are qualified to conduct work and repairs on equipment from our manufacturing members. They are also committed to using SEIRS trained installers, which is a unique initiative from SEMA that trains on the safe and correct methods of installation according to our defined standards and manufacturer specifications.
Completing the circle in your investment is through continued maintenance. Employees should receive Rack Safety Awareness training on how to correctly use and maintain the racking within their varied environments. Through this education they can confidently perform regular checks and understand how to report and address issues that need attention to maintain a safe system.
The HSE also recommends an annual expert inspection undertaken by a technically competent person who has sufficient training and knowledge. To support this, we operate our SEMA Approved Rack Inspector (SARI) initiative which consists of highly qualified professionals who must successfully pass an intensive three-day training course, written examination and practical assessment to achieve their qualification.
A report from a SARI provides you with clear guidance on the condition of your equipment and uses a traffic light system to indicate actions required and recommended timescales for corrective action.
Safety
As a leading voice on safety within the warehouse industry we understand the cost of safety. Did you know under the HSE’s Construction Design & Management Regulations 2015 it is a legal obligation for you to check your racking supplier’s quality credentials, ensure they meet health and safety requirements and use trained labour. Failing to do so can result in hefty fines from the HSE, damage to your reputation and the cost of lives affected by an accident.
A safe working environment comes as standard when working with SEMA. Each member is committed to demonstrating their expertise and raising quality within the industry. They can provide assurances that the storage solution has been correctly designed, manufactured, installed and maintained to meet SEMA Standards.
New for 2023
Safety in the workplace is increasingly important and it is something that SEMA has worked hard to promote over the last 50 years. It is the driving force behind every decision, guidance, publication, and initiative we develop. As the industry changes and new technologies are introduced, our technical committee continues to review and develop their guidance to meet the changing needs of logistics and warehouse companies.
Next year will be about raising quality and reminding everyone on the importance of using trained labour, for example you wouldn’t buy an expensive car and then risk getting the brakes fitted by a novice using a handbook. We feel the same when it comes to areas like the installation of your racking. After all it is performing a critical job holding tonnes of product above employees’ heads and keeping everyone safe. Getting it right at the installation stage is essential, each and every time!