Expect the unexpected
With many more low-value items shipped as parcels, distribution centres are receiving more odd-shaped or poorly wrapped items. These are difficult to handle and sort automatically, but new system designs can handle a much larger chunk, argues Jørgen Staun.
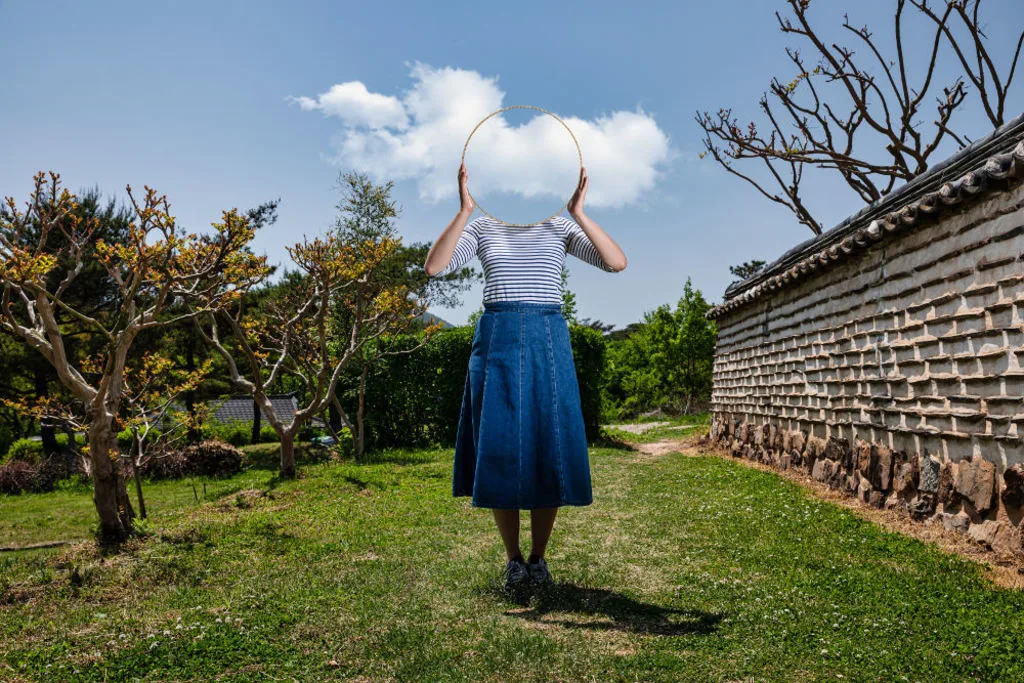
NO MATTER how carefully a conventional system is designed, it won’t be able to adapt to the introduction of these new shapes into the parcel mix, while operating at high-speed processing capacity. So, BEUMER Group has developed a system design that addresses these limitations and solves the problem of how to sort these troublesome incompatible items. Let’s take a closer look at the solution.
In the new system, parcels are fed in bulk from the tipper to the hopper and then transported to operators who singulate and face them. Each item is placed on an induction belt, which inducts it onto a free tray. The number of induction areas can be determined and designed according to parcel hub requirements.
The new design incorporates a number of new features to the induction process, improving the ability of the system to handle non-conveyable items.
Induction flap: This is a special feature introduced to the induction belt. As the item travels along the induction belt, the belt flap pushes the item onto a free tray. The flap is able to handle all manner of item shapes, such as polybags, flats, round and odd items.
Sorter tray: The sorter tray is shaped and tilted in such a way that items roll into the tray corner, providing stable transportation of odd items at higher speeds.
Discharging items: When items are discharged, the double-sided trays are designed to ensure that the discharge of one item does not affect the positioning of the second item sitting on the other side of the tray. It now stays in its position without falling out.
Sorter capacity: Using a parcel size 300*400mm as an example, the sorter capacity per induction area will be more than 17,000 items per hour.
The new system design also offers different solutions for discharging items into bags and roll cages. The design allows each chute to cater for multiple destinations, further optimising the use of footprint. With OPEX considerations in mind, the chutes have been designed to gently slide the items to avoid damage during processing.
There are a number of advantages of the new system design.
First up, the design provides increased capacity – especially in light of previously having to deal with these types of parcels manually. Even with one induction line, for instance, operators can achieve a high number of handled parcels per hour.
Secondly, the variety of items the system is able to process has been extended considerably compared with other high-speed handling solutions. This is due to not having the traditional belt-to-belt transfer which is often associated with jams when handling odd sized and oddly wrapped parcels. With no gap and the pushing flap, the solution handles challenging items such as polybags – also those with bendable corners and unstable content.
Thirdly, the system is designed to use very little floor space, saving on the physical footprint of the overall system.
Fourthly, the new system design also integrates well with both manual induction and automated singulation and induction and can even include an automatic weighing system in the induction.
Finally, the system doesn’t necessarily require 6-sided scanning systems – at least not with manual induction where the human factor intuitively will face the label upwards.
Jørgen Staun, concept designer, Beumer Group
For more information, visit www.beumergroup.com