Shuttle boosts warehouse performance
A multi-channel shuttle system installed at Coventry-based Christie Lites has provided a dramatic increase in volumetric capacity and a five-fold rise in the number of pickable locations, ensuring optimum operational efficiency.
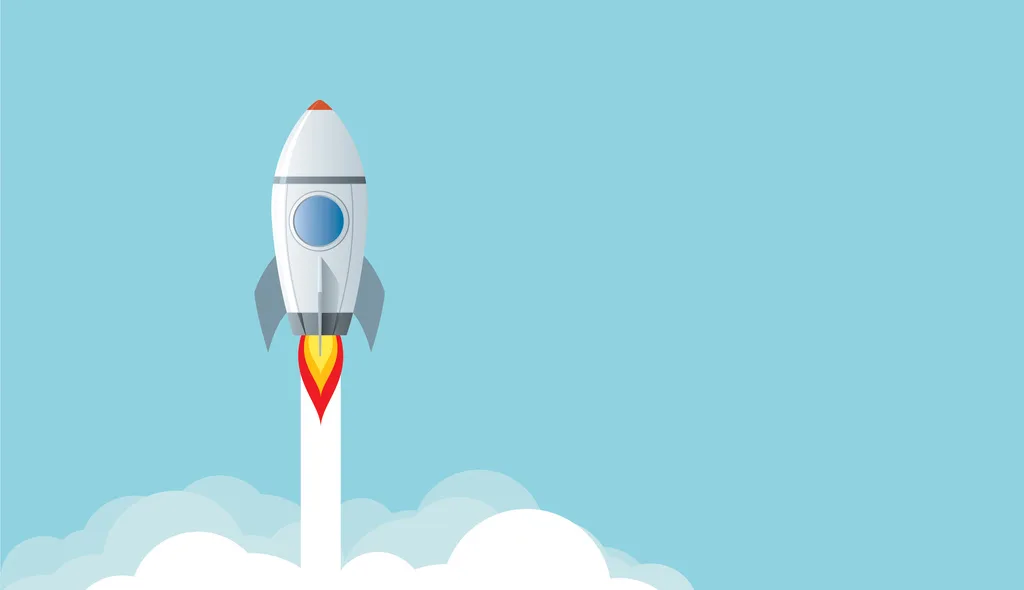
SEC STORAGE was invited by Christie Lites, a US stage lighting company, to design a solution to store their stage trussing, which was being bulk-stacked at their large warehouse facility in Coventry, as this existing system was causing several key operational issues, in both capacity and selectivity.
The two design options that the client was considering prior to SEC’s involvement, were either a traditional Adjustable Pallet Racking (APR) system or Drive-In system, however, both had significant limitations:
- APR would provide 100% selectivity but resulted in very low floor print utilisation (31.1%) with a volumetric utilisation of only 24.2%.
- Drive-In made better use of the cube, however, caused significant operational issues, just 30% selectivity of products resulting in huge picking inefficiencies and high operational cost increases, and the operation would require a special type of truck adding considerably more expense to the fleet.
- Health and safety concern for both in-rack damage caused by drivers entering the rack, as well as high pick velocity which a drive-in solution could not support.
Bespoke shuttle design
SEC identified that a solution that would overcome both the selectivity and storage density issue, would be a shuttle system. However, Christie Lites had been told by other companies that it would not be possible due to:
- The irregular load and castors on the base meant that no commercially available shuttle would be able to safely pick up the load.
- The sensors of a standard shuttle would not be able to sense the load without a pallet, meaning the front-facing laser sensors would have failed to notice the load and be unable to position itself correctly.
SEC reached out to key partners within its supply chain, and found that virtually all shuttle suppliers confirmed they would be unable to handle the load as standard.
Making It happen
In response to this, SEC used in-house logistics experts to design a completely bespoke, modified shuttle system, comprising of an additional raised platform that would be inserted between the castors in order to lift the product safely.
SEC proposed technical modifications to the program algorithms and sensor technologies that would allow the products to position themselves correctly underneath the load and also designed a split-load level, allowing storage of two smaller cases within one rack, only previously possible if stored in APR.
Furthermore, SEC incorporated a rapid moving, ground floor pedestrian picking location beneath the shuttle, aided by a bespoke designed mesh system to protect users from any falling equipment, thus reducing the cost of the system and increasing pick velocity.
After putting its bespoke and highly innovative solution forward to its supply chain, all the primary European suppliers declined to quote due to the inability to adapt their own standard system.
SEC explains: “Confident that our proposed solution was achievable, we looked outside the UK and identified one supplier that saw the opportunity to deliver this innovative technology with us. For testing, we transported the load items to our supplier at their facility. Once completed successfully, we were able to evidence the testing process with in-depth data and analysis which led to the final design being agreed with Christie Lites.”
The client takes up the story. Christie Lites director Robin Wain, explains: “Having worked with SEC Storage on our previous warehouse installation, we knew that they offered something different to other partners. But we have been overwhelmed by the lengths they have gone to, designing and delivering a totally bespoke solution to an otherwise unsolvable issue. The other options out there were just not fit for purpose, and everyone told us we couldn’t do what was required. But not SEC Storage. Their team of experts together with the manufacturer have been incredible to develop this solution and we will be reaping the rewards for years to come.”
For more information, visit www.sec-group.co.uk