UK retailer de-risks Peak with smart tech
Automated right-size packaging technology from Sparck has de-risked peak fulfilment for The Works and its logistics partner iForce.
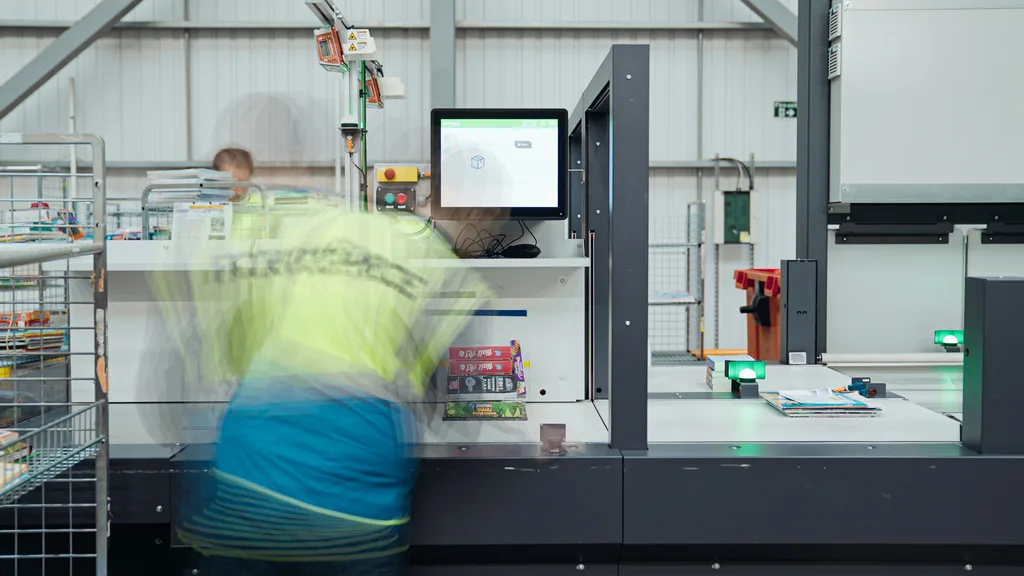
CHALLENGES IN finding labour, combined with rising costs, prompted logistics service provider, iForce, and client, The Works, to re-think their approach to achieving peak for the toys and stationery retailer. Ensuring reliable fulfilment would require a commitment to advanced automation including right-size packaging technology from Sparck.
To address these issues, in 2020 iForce embarked on a business-wide initiative to develop a strategy for warehouse automation investment, and as a key client The Works was fully involved.
{EMBED(1256951)}
IForce business planning manager Neil Lavercombe, who is responsible for ecommerce development, explains: “Like every business in the industry labour was becoming increasingly difficult to find and more expensive, and that put at risk our ability to deliver peak for our clients. So, we decided to develop a strategy around automation, based on lowering our dependency on labour, particularly at peak.”
There were three elements to the strategy: robotic goods-to-person order picking, robot assisted picking and automated packaging systems. However, it was absolutely critical that all three should work in perfect synchronisation with each other.
The Works was a prime candidate for robot-assisted picking linked to an automated packing machine. Lavercombe points out: “When it came to evaluating the different packing solutions on the market, we quickly determined that the principle of auto fit-to-size packaging had big advantages over the traditional box-closer systems, and the supplier that really stood out was Sparck Technologies with its CVP Impack machine.”
The CVP Impack measures, constructs, tapes, weighs and labels each parcel in seconds. The operator places the item(s) to be packed onto the machine and scans the order. The system identifies the order and automatically conveys the items to a 3D scanner to measure and calculate the minimum box size required. The cardboard is then cut and folded to create a fit around the goods and tape is applied on two sides to secure the box. Then an in-line scale checks the weight against the order and the box is automatically conveyed to a label printer where a carrier compliant label is created and applied.
{EMBED(1256950)}
Speed, throughput and reliability are core attributes of Sparck’s fit-to-size auto-boxing technology, an important capability given that at peak The Works will see around 70% of its eComm parcels created automatically by the CVP Impack.
Typical eComm challenges around very changeable order profiles at peak, multi-item orders and SKU variance play to the strengths of the CVP Impack and the flexibility of Sparck’s fit-to-size technology.
Lavercombe says: “Order profiles, in terms of items per order together with the physical size of orders, can vary throughout the year, ranging from a typical ecom profile of one or two items per order to 10+ items per order. The CVP Impack simply produces the right sized packaging for whatever orders we have, a far simpler and less complex process than using traditional fixed size cartons, with the added advantage that void fill is completely eliminated.” As a consequence, significant savings in material costs have been achieved.
“We wanted to keep things very simple,” says Lavercombe. “The packaging machine had to integrate with both our existing manual processes and our new robotic systems – once again the simple approach of the Sparck machine worked for us. It seemed designed from the bottom up to do the job, rather than an adapted system. For example, a great feature is the way components needed for day-to-day maintenance are readily available and a drawer system offers easy access – well thought out design, from day one.
So, how is the machine performing? “Feedback from the Rugby site has been really excellent,” concludes Lavercombe.
For more information, visit www.sparcktechnologies.com