Boost productivity quickly
Warehouse automation innovations and analysis from Locus Robotics.
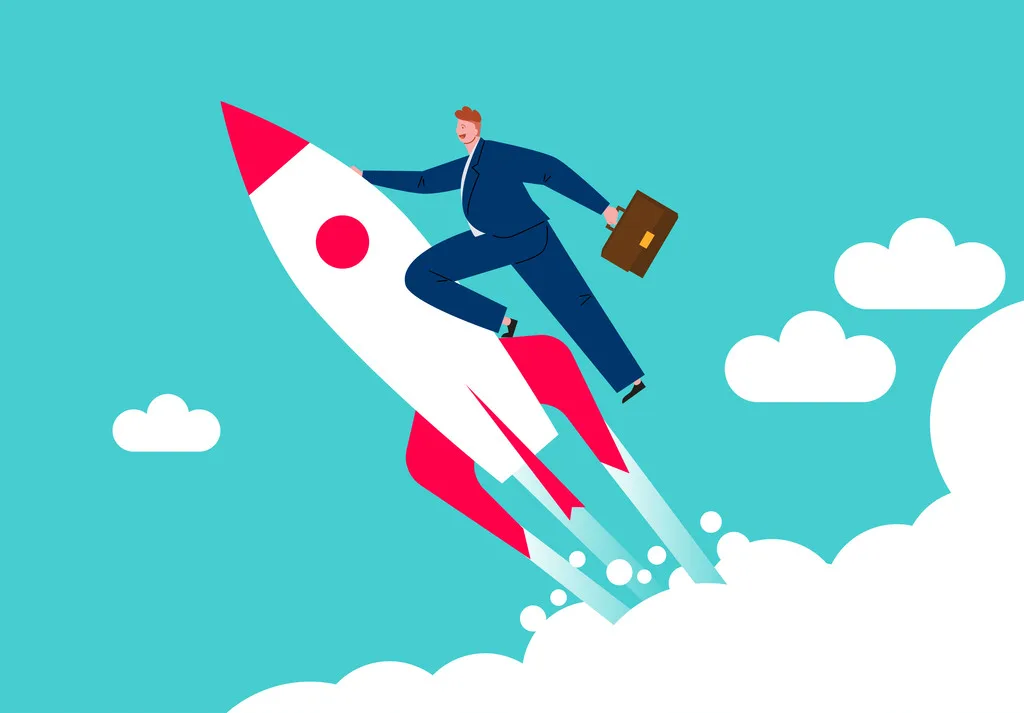
LOGISTICS MATTERS is delighted to have a Q&A with Locus Robotics vice president, EMEA & APAC Denis Niezgoda to dig deeper in the world of warehouse robotics.
What ROI can customers expect from moving from manual picking to Locus robots?
If you’re moving from manual picking to the Locus solution, it delivers value in several ways. In broad terms, customers can expect to see a boost to productivity of 2-3x in as little as 4 weeks following implementation. This productivity boost reduces the cost of picking operations, so it generates an immediate benefit. Remember that because we offer the Locus bots on a “robots as a service” (RaaS) basis, there’s no hefty capital cost upfront just a monthly fee. Beyond that, there are a raft of other benefits that we refer to as a “soft roi”, including improved warehouse safety and less time to train newcomers – especially an advantage during peak season.
How has Locus developed its portfolio?
We have focused on further maturing our products regarding navigation, reliability, and the ability to operate fleets of several hundred bots. We now have customers sites with well over 1,000 bots. This maturity allowed us to evolve our software suite based on customer requirements. The comprehensiveness of our solutions speaks to a growing number of customers that want interoperability – one integration platform to solve multiple challenges instead of managing several vendors. Feedback from our customers regarding higher payloads and new use cases led to us introducing two new robotic form factors in the shape of Vector and Max to ship alongside our existing Origin autonomous mobile robot (AMR).
Tell us about LocusOne.
The key thing about LocusOne is that all our robots operate under one single platform. It makes it easy to deploy and manage large numbers of AMRs, including different form factors, together as a single orchestrated fleet. LocusOne also allows our customers to run diverse tasks such as picking, putaway, point to point and more – all in one warehouse under the same platform. LocusOne includes data-driven, actionable insights such as real-time dashboards. You can scale easily, allowing you to start with one use case and then expand to the next one with different payloads and volumes.
Can you tell us about your partner network in the UK?
In the UK as well as worldwide, our approach is to educate partners who have an existing customer base to determine where Locus could add value and we work with WMS partners for the integration. We are implementing the solution ourselves for consistent customer experience and proximity to the customer.
How does Locus Robotics use AI?
One example is navigation. Our AMRs automatically learn efficient travel routes in a warehouse, maximising overall efficiency. As robots continue to learn on the floor, they share information across the fleet, continually optimising routes to increase productivity and reduce worker fatigue.
How can you help end users with the integration challenge?
The team here at Locus have a lot of experience in integrating into different systems and equipment, plus we have the benefit of all that data to understand what works well. LocusOne can be integrated with sortation and packaging systems, for example. In one recent deployment we have our Origin bots controlling a cold store door to access a pick location. Our bots with conveyor tops can also integrate with conveyors to control loading and unloading or on-demand packing.
For more information, visit locusrobotics.com