Get your trucks connected
JUNGHEINRICH IS equipping all newly ordered vehicles produced in its European factories with telemetry units as standard.
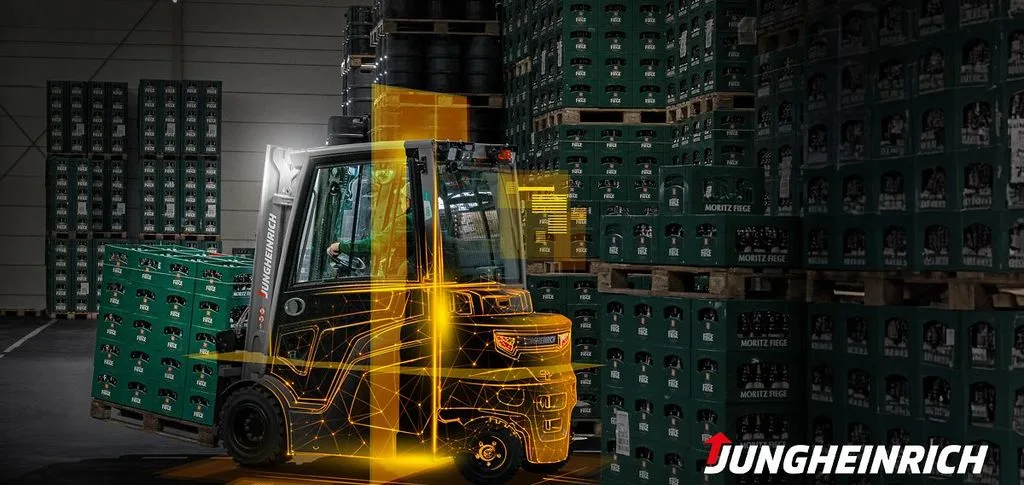
Jungheinrich vehicles are therefore fully network-capable ex works and ready for intelligent integration in the warehouse. With the help of the Jungheinrich FMS fleet management system, customers can use this data to optimally use their fleet.
Jungheinrich customers will now receive the Jungheinrich fleet management system starter kit free of charge when purchasing a new vehicle. The starter kit has the five core functionalities of inventory management, location management, user management, operating hours and the Call4Service customer service.
In inventory and location management, the fleet management system provides an overall overview of the size and composition of the fleet at a local and global level. The operating hour forecast helps to coordinate operations and enables the rapid identification of vehicles with particularly high or low usage. Using the Call4Service function, customers can contact Jungheinrich customer service at any time via the Jungheinrich FMS and receive a comprehensive overview of open and completed service calls.
“Data is one of the most valuable resources in the warehouse today. We are now making this data easy and efficient to use for our customers,” says Christiane Pilz, head of main segment digital products at Jungheinrich. “Connectivity is an essential key to further optimising intralogistics. By processing information better and faster with our Jungheinrich FMS, we are making our customers’ warehouses even more efficient.”
Thanks to the telemetry units, Jungheinrich customers receive real-time data about the condition and usage of their vehicles using the Jungheinrich FMS in order to optimally control their fleet. Data transfer to the Jungheinrich Cloud usually takes place via a mobile phone connection, but can also be implemented via WLAN.
“If our customers agree to share the usage and vehicle data of their forklift trucks with us, this also provides us with important insights into the real use of the industrial trucks. This allows us to tailor our range of solutions to our customers’ needs even more flexibly, individually and attractively,” says Pilz. “These include, for example, remote diagnostics to specifically reduce or avoid downtimes through more efficient service or intelligent energy solutions as the basis for cost- and consumption-optimised energy management.”
For more information, visit www.jungheinrich.co.uk