Transition from diesel to electric
Windsor partners with National Trench Safety in support of its strategic transition from IC to electric materials handling equipment.
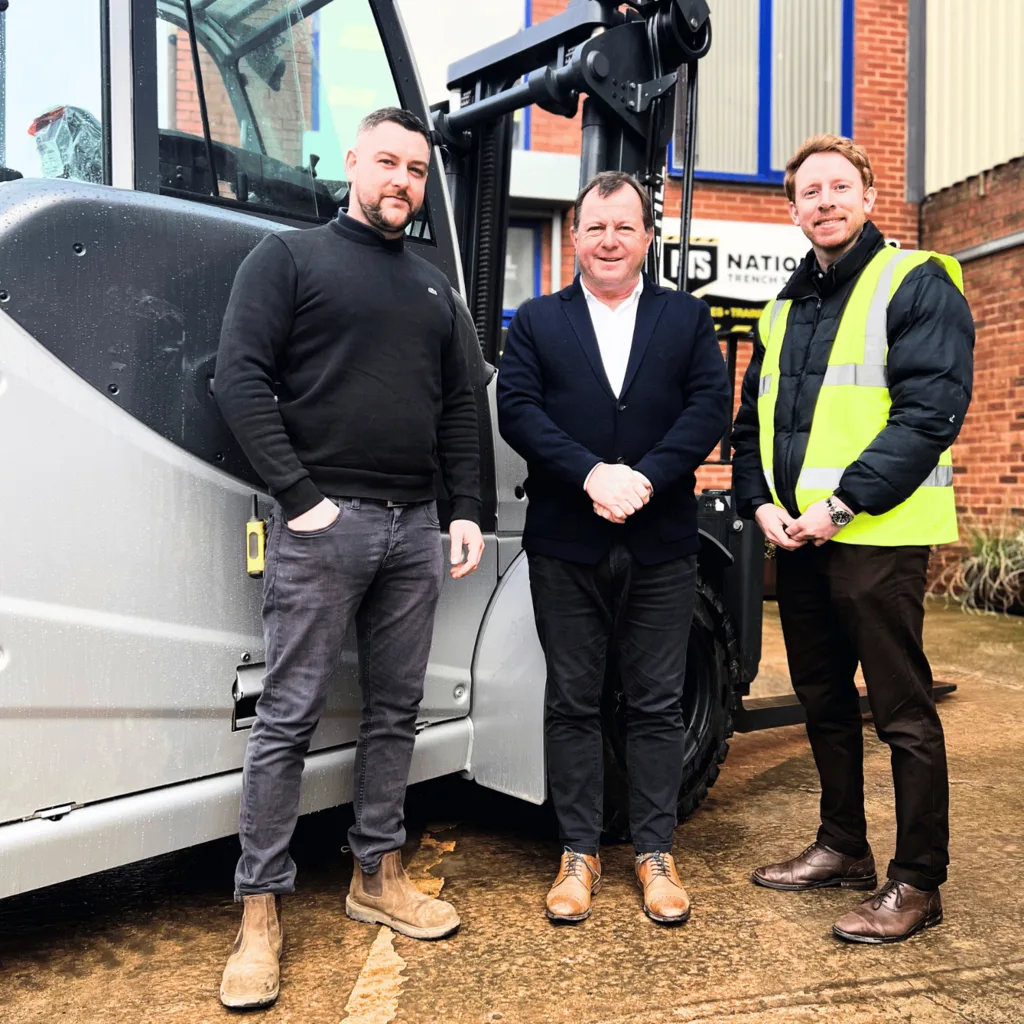
THE SHORING specialist upgraded their diesel-powered forklifts as they undertook a strategic transition from diesel to electric-powered forklifts in pursuit of their commitment to moving towards a net zero carbon footprint.
The rising cost of diesel is another factor in NTS’s decision to move to equipment that better aligns with improved operational efficiencies, reduced environmental impact and lowering costs
NTS managing director Patrick Flannery takes up the story.
“Without question, operations like NTS are motivated by these three core areas when making decisions. This doesn’t come without challenges. It was important that the appropriate due diligence was conducted before any change was implemented, and Windsor’s approach wholly supported this.”
Technological advancements in both lead acid and lithium powered equipment have led to a significant shift in customers opting for an electric powered alternative over the historically favoured IC truck. To this end, due to demanding site conditions, NTS could not compromise on shift run times, reliability or durability so these were all important considerations when going through the varying options available to them.
Once it was identified that operational efficiencies could be maintained, if not improved, the companies then looked to see if total cost of ownership can be reduced.
Windsor’s Wakefield branch sales manager Kieran Douglas explains: “Initial conversations took place with Patrick Flannery and Karl Clayton. Working with the team, we collated information regarding the trucks runtime and carried out a site survey. From here, we provided a fuel calculation along with total cost of ownership which showed big cost savings.”
Once this had been identified, the next step was to look at both lead acid and lithium options and given the requirements of this truck, lead acid was the preferred choice; with a lower upfront cost, the ability to withstand operational requirements along with a well-established recycling infrastructure.
{EMBED(1286403)}
Kieran continues: “At Windsor, we are fortunate enough to have access to demo equipment across our entire core product range which allows customers to see whether or not there will be an operational impact when making the switch. After a successful demo of a STILL RX60-80 paired with a Fronius charger it was found that the truck was more than capable of handling the runtime and withstanding the challenging site conditions.
“The demo was so successful two trucks were ordered, with the second truck being utilised at the new Coventry facility. We provided short-term electric options to operate on site until the new units were delivered.”
The STILL RX60-80 delivers powerful acceleration and lifting capabilities, ensuring optimal efficiency in material handling operations. Constructed with robust materials, the forklift excels in challenging environments, providing a long-lasting and reliable performance.
Complementing the electric forklifts, Windsor Materials Handling recommended the Fronius battery charger for its efficiency, reliability, and advanced charging technology. Fronius chargers are renowned for their robust construction, ensuring durability in demanding industrial environments.
The collaboration between Windsor and NTS resulted in a successful transition from diesel to electric forklifts, achieving substantial fuel savings and cost reductions. The adoption of the STILL RX60-80 and Fronius charger actively supports NTS in their mission to achieve net-zero emissions, showcasing Windsor Materials Handling's commitment to delivering sustainable and high-performance materials handling solutions.
For more information, visit www.windsor-mh.co.uk