Highlighting the hidden element
It is not the component people typically notice first with warehouse robotics, but software is the part that makes it tick. Here, Kane Edwards, Business Development Manager, Locus Robotics brings the hidden element to life.
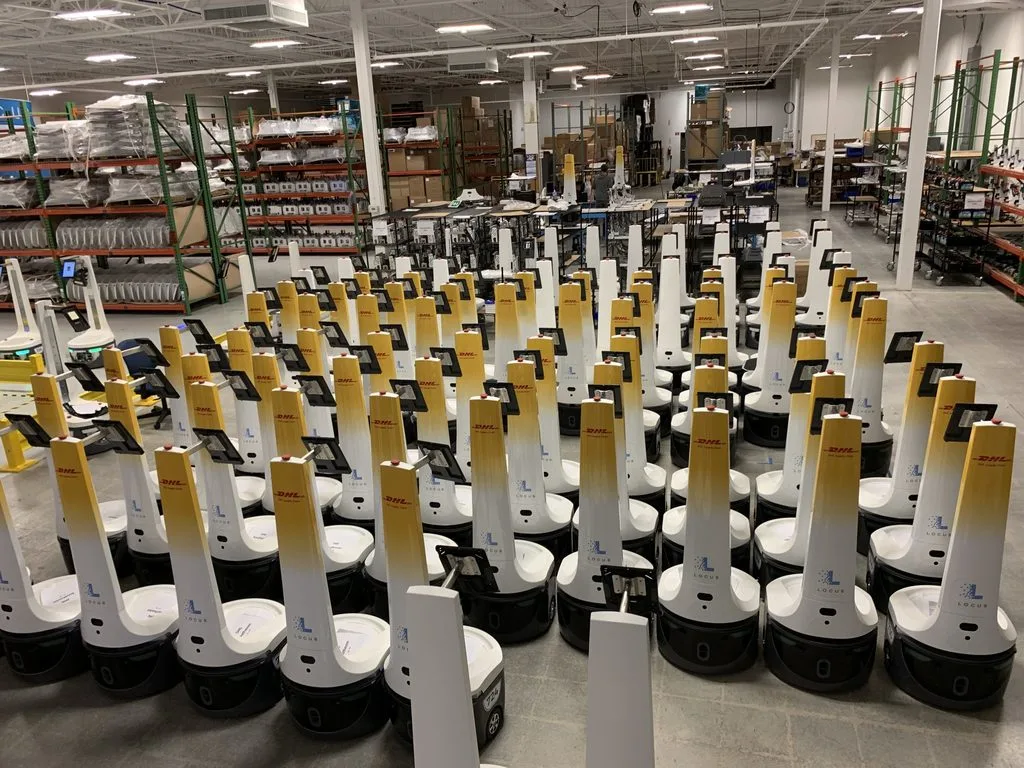
LOCUS ROBOTICS has proven experience in warehouse automation solutions, with more than 15,000 robots in use very day across more than 320 facilities with more than 4 billion units picked to date.
Locus Robotics business development manager Kane Edwards, explains: “We are tried and tested. When it comes to warehouse automation projects, it is important to know you are going in to bat with a partner that has ample experience and an abundance of solutions.”
The Locus automation ecosystem is central to its offering and encompasses an end to end system, with software suites employed with robots with differing payloads. The Origin but is suited to fulfilling lighter items, and Vector is designed for heavier items and for high-productivity material handling applications. In terms of software duties, LocusOne controls the robots helping to autonomously orchestrate robots in the warehouse. LocusHub is where the analytics and insights reside.
Locus Robotics can quickly bring value to brownfield sites, as its robotics fleets can be added to traditional warehouses with a minimum of fuss or disruption.
Kane adds: “We are also want to be a strong consideration for greenfield sites as we can be just as powerful when you are planning your best case future.”
Insights
The value and the power of software over robots is often overlooked. There is so much data generated from modern warehouse systems and analytical software can use this to, for example, help boost morale in the warehouse.
Kane explains: “The robot is important and must be robust, but its the minimum requirement really. We find procurement professionals are often well versed in purchasing racking, conveyors and so on, but are less so when it comes to robotics, and as a result can tend to underestimate the amount of software is involved with robotics.”
Locus Robotics uses the webinar to delve into software in detail, emphasising the importance of data security and making sure your automation vendor can integrate smoothly with your WMS and other software solutions, among many other issues.
“It’s one thing telling a robot what to do, where the efficiency gains come in is when our algorithm takes the range of tasks you need to accomplish and works out the most efficient way to do it.”
You have insights via LocusHub that make live warehouse performance easily viewable remotely, which can be quickly presented to aid decision-making.
The bots are typically equipped with an iPad to provide a user interface, which takes the information provided by the customer’s WMS and is presented in a uniform way that makes sense to the picker. Photos of the product concerned can be presented as well as the location number. There are also gamification tools that can help drive labour productivity throughout shifts. For example, this can be used to problem solve as a shift progresses. If a picker is below expected productivity levels it will show in real time. This might not be related to the picker. It may be that the zone they are in is receiving less orders, and it might be preferable to move the picker to another zone. This decision can be made in real time.
Led by algorithms
Kane adds: “It’s one thing telling a robot what to do, where the efficiency gains come in is when our algorithm takes the range of tasks you need to accomplish and works out the most efficient way to do it.”
The warehouse manager is gathering data as the robots are carrying out the work. You can see the dashboard illustrating how the processes are working, and whether SLAs are being hit. It adds insight to the operation. The picker does not follow the robot, the robot moves from aisle to aisle and different pickers add items to the bot until it is full and goes to the pack station, for example. This way, it cuts out time wasted with pickers walking.
Once it has completed its work at the drop off zones, then the robot cycles back and starts again. It can work the same way, travelling from picker to picker, to replenish shelves.
Flexible and scalable
The system is also flexible and scalable and can work on a Robotics-As-A-Service (RaaS) model.
“We can show you how to add bots and use the software to manage those assets,” says Kane. “How easy is it to scale up for Peak? We can drop a robot in and have it working within three minutes, into the same system as the rest.
“RasS lends itself to an OPEX model and reduces barrier to entry. It’s much more scalable, you can have a core fleet and add in bots when you need them, and then send them back.”
Modular, flexible solutions are very useful if you are not sure how your business will evolve and what your volumes will be. The robotic solution is less of a risk than fixed automation, which thrives on certainty of volume.
In this webinar, Kane tackles how the robots work, how software adds value, how RaaS can work for you, and much more. He also tackles questions from warehouse occupiers on the nitty gritty of using robotics in warehousing.
Catch up On Demand
For more see Kane’s webinar – Warehouse Automation – Software:+ The Power Behind the Robots.
You can register and view for free here.
Watching the webinar will net you CPD points.