Global shocks and local responses
Nick Petschek outlines how supply chains can build adaptability amid geopolitical uncertainty.
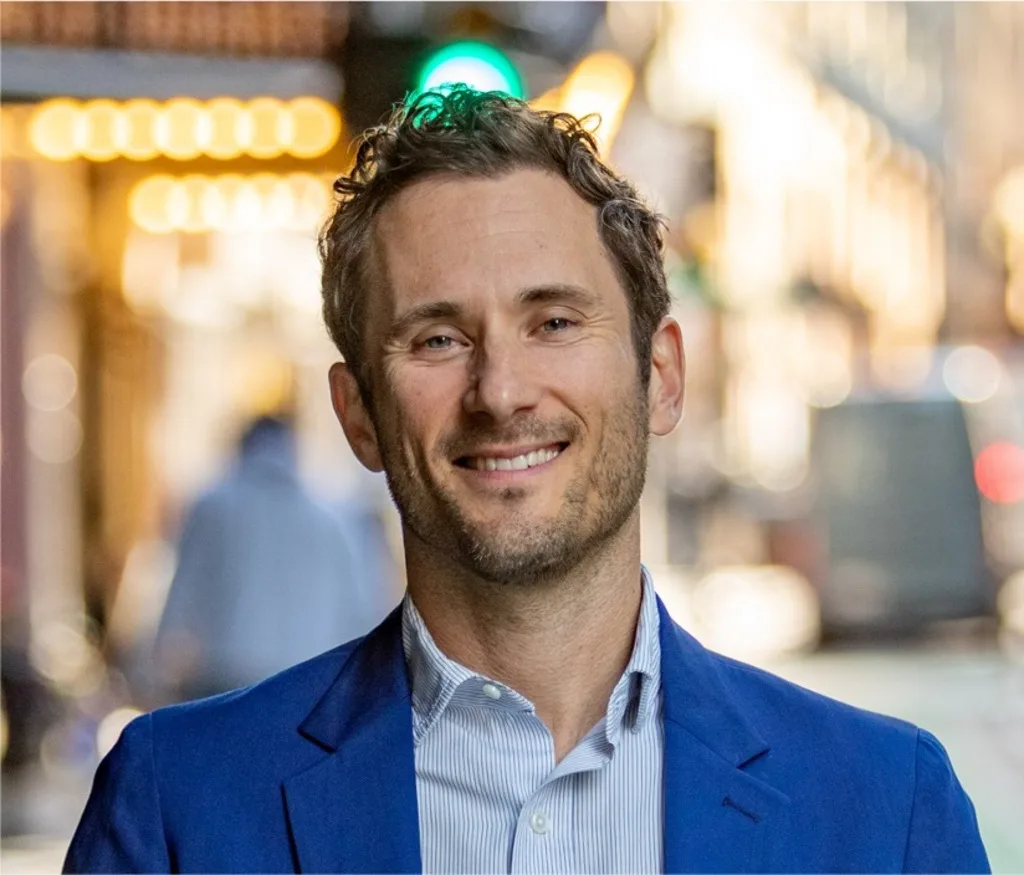
THE WORLD’S supply chains are once again under the microscope. According to a recent survey by The Conference Board, 85% of large company executives plan to make significant changes to their supply chains—an increase of 15 percentage points from the previous year and a notable surge compared to the post-pandemic period.
These shifts, driven by fears of trade wars and geopolitical instability, highlight a broader trend: businesses are recognising the limitations of reactive strategies and moving toward more proactive, resilient supply chain models.
While technical measures such as supplier diversification, digital tracking, and inventory optimisation are essential, the people and change management aspect is just as critical. Leaders must ensure their teams are prepared to navigate uncertainty, develop key skills, and avoid falling into ‘survival mode’ thinking.
Preparing for disruptions: a leadership imperative
Adaptability isn’t built overnight. It requires strategic foresight, cultural agility, and operational adaptability. Leaders are critical in shaping how their organisations prepare for and respond to disruptions. Three key strategies stand out:
- Understanding the root issues: Policies such as tariffs and reshoring incentives often dominate discussions around supply chain disruptions. However, these measures frequently mask deeper structural shifts, such as changing consumer demand, the rise of automation, and shifting geopolitical alliances. Beyond operational adjustments, leaders should ensure their teams are equipped with the ability to analyse and adapt to these shifts by fostering a workforce culture that values critical thinking, cross-functional collaboration, and the ability to connect short-term market changes with long-term strategic needs.
- Scenario planning and agile decision-making: Organisations must adopt a dynamic approach to risk assessment. Leaders should engage in scenario planning to anticipate different geopolitical outcomes, regulatory shifts, and economic fluctuations. This is not just about logistics—it’s about ensuring teams have the right mindset, communication structures, and leadership support to pivot effectively when challenges arise. Agile decision-making thrives in an environment where employees are empowered to think proactively, rather than waiting for top-down directives during crises.
- Strengthening local resilience while maintaining global flexibility: Many businesses are moving away from single-source dependencies and embracing a hybrid approach that balances global efficiency with regional adaptability. However, true resilience extends beyond supplier diversification—it hinges on the leadership’s ability to cultivate a workforce that can navigate complexity, manage uncertainty, and maintain trust across global and regional partnerships. Equipping employees with skills in adaptive problem-solving and cross-cultural relationship management is just as critical as investing in diversified logistics solutions.
Supply chain resilience
Building supply chain resilience requires more than just operational tweaks—it demands a shift in workforce capabilities. The most effective teams will blend technical expertise with strategic and relational skills to navigate uncertainty.
Hard skills:
- Data analytics and digital supply chain management – The ability to interpret supply chain analytics and leverage predictive modelling tools will be crucial for forecasting risks and optimising decision-making.
- Regulatory and trade compliance expertise – As trade policies become more unpredictable, companies need experts who can monitor regulatory changes and ensure compliance across multiple jurisdictions.
- Supplier and logistics network optimisation – Technical knowledge in supplier diversification, inventory management, and logistics operations will be fundamental in mitigating supply chain shocks.
Soft skills:
- Adaptability and crisis management – In a world where supply chain disruptions are increasingly the norm, employees must be able to think on their feet, adjust strategies in real time, and maintain composure under pressure.
- Cross-cultural negotiation and relationship management – With shifting trade alliances, businesses will benefit from leaders who can engage in complex negotiations, identify joint value in cross-border partnerships, and foster long-term supplier relationships rather than transactional arrangements.
- Collaborative problem-solving and systems thinking – Leaders who can break down silos and encourage integrated, enterprise-wide decision-making will be better positioned to develop resilient supply chain solutions.
Avoiding survival mode
Many businesses, when faced with crises, shift into survival mode—focusing narrowly on short-term cost-cutting, reactive decision-making, and risk avoidance. While these measures may provide temporary relief, they can also hinder long-term growth and competitiveness. To navigate uncertainty successfully, organisations need to adopt a more strategic and forward-thinking approach.
One critical shift is moving away from a zero-sum mindset. Trade tensions and supply chain disruptions often stem from the assumption that gains must come at another’s expense. However, companies that prioritise collaboration—through strategic partnerships, co-investment in supply chain technology, or shared risk agreements—are more likely to achieve long-term stability.
Balancing agility with efficiency is another key factor. Traditional supply chain models have long prioritised cost reduction, yet companies focused solely on lean operations often become highly vulnerable to disruptions. Organisations that build flexibility into their supply chains—through diversified networks, adaptable logistics strategies, and proactive planning—will be better positioned to absorb shocks without compromising operations.
Finally, resiliece should be embedded across all levels of an organisation. Encouraging employees to think proactively, challenge assumptions, and propose innovative solutions fosters a culture of preparedness. This shift, supported by clear communication and an adaptive mindset, ensures resilience becomes a core organisational capability rather than a reactive response to crises.
The path forward
The evolving geopolitical landscape will continue to challenge global supply chains in unpredictable ways. Organisations stuck in survival mode—reacting to crises with short-term fixes—will struggle to keep pace. Instead, leaders should shift their teams into thrive mode, equipping them with the skills and mindset to anticipate disruptions, adapt with agility, and drive innovation. By embedding resilience into culture, decision-making, and operations, businesses can transform supply chain volatility into a long-term competitive edge.
Nick Petschek, MD EMEA, Kotter International
For more information, visit www.kotterinc.com