Safety considerations for the handling & storage industry
Thought leadership from P. Airey Tail Lifts & Auto Extract Systems.
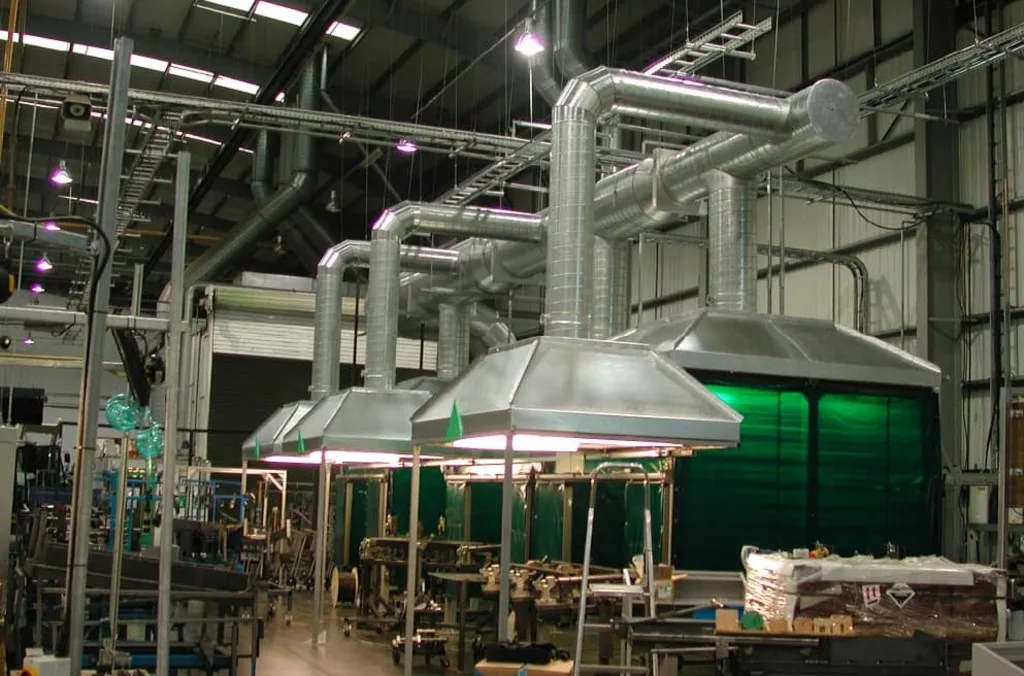
AS A business that works with material handling and storage, it's essential to be aware of workplace health and safety. Whether you are a manager, supervisor or employee, you are responsible for ensuring the safety of yourself and those around you. This industry has several risks, particularly around lifting and transporting heavy materials or handling hazardous substances. Employers should ensure that procedures are in place and that staff understand risks, how to prevent incidents, and what steps to take in the event of an emergency. Employees themselves must follow health and safety regulations, only carry out tasks as part of their contracted duties, and reasonably conduct themselves.
P. Airey Tail Lifts is a UK specialist tail lift provider serving North West and North Wales. Working with leading businesses that use commercial trucks to transport materials, P. Airey Tail Lifts knows all about the importance of keeping people safe in a working environment. They have provided us with some helpful information on the health and safety risks you should be aware of and how you can keep your business safe and compliant.
What Risks Are There?
First and foremost, the use of equipment is one of the biggest dangers to consider. Powered equipment, especially, is hazardous as it can be uncontrollable and cause a severe accident if misused or if it malfunctions. Types of equipment that you may come across often include lifting equipment, vehicles, conveyors, and more. Accidents may involve a person getting trapped, crushed or run over.
In the handling & storage industry, workers will often transport various goods and materials from place to place. Tasks such as this may be completed by using vans, pallet trucks or manual handling. If a load limit is exceeded, then this creates a risk as it can cause equipment to break and goods to fall. If a storage box breaks, the contents can be hazardous to those in the vicinity, especially if it contains heavy or sharp items.
Slips and trips are common workplace accidents that can happen to anyone in every industry. However, it is prevalent in busy environments where workers handle many goods such as boxes and other items. If the job involves working at height, such as in a warehouse, this creates a health and safety risk as falling can seriously injure a person.
Handling chemicals is a critical risk that you should be aware of. Chemicals can be dangerous if it is inhaled or touches the skin. If there is a chemical spillage, this can create a slippery surface. Chemicals should not mix with incompatible chemicals to avoid an unstable reaction or fire hazards. Similar to this point, any flammable item could be ignited and lead to a dangerous explosion.
Tips on Keeping Safe & Compliant
Now that we've talked about some of the top risks associated with your business, it's time to look at some steps you can take to keep yourself and your employees safe and compliant. The first step you should implement is to produce a comprehensive health and safety policy. This policy should identify risks, provide guidelines on safely handling material, and outline responsibilities. Employees should be given a copy of the policy before working for you.
Your employees should receive proper training on procedures and how to use the equipment. It is recommended that they are re-trained every so often to remember how to work safely. Workers should wear protective clothing when working with risk. Clothing can include items like padded gloves, gas masks, eye protection, and helmets.
As we mentioned, one of the biggest dangers is handling chemical materials. Any chemicals should be clearly marked with hazard symbols. Only people trained to do so should work with chemicals. When not in use, chemicals should be stored safely as specified. They should be kept well away from non-compatible chemicals.
Any equipment you use should be well maintained, which is where LOLER comes into force. The Lifting Operations and Lifting Equipment Regulations specifically regulate the use of heavy lifting equipment for work purposes, such as tail lifts, forklift trucks and cranes. The regulations ensure that equipment works as intended and is used correctly by trained and competent personnel to prevent accidents and severe injuries. Companies and their employees have faced serious consequences for not following the regulations, including hefty fines and even imprisonment. The regulations state that equipment must undertake regulation LOLER inspections to ensure there are no faults. LOLER can affect several industries, particularly handling & storage where lifting and transporting materials is a regular task.
Proper ventilation is also critical, bringing us to our last point. Your workplace environment may be filled with harmful airborne contaminants such as dust, mists and fumes. A local exhaust ventilation (LEV) system is highly recommended for industries that handle hazardous materials. The systems can cover many applications, from automotive body shops to manufacturing plants, metalworking workshops, and even school labs. They help create a pollution-free environment and ensure your employees breathe clean air free of harmful contaminants that can cause health problems. According to the Health and Safety Executive, LEV systems must undergo regular LEV testing (at least every 14 months). The test is a thorough examination to ensure the system is working as intended. As LEV systems are vital for extracting and disposing of harmful contaminants, a faulty system can be dangerous if it fails to work properly.