More than picking
Autonomous Mobile Robots (AMRs) can accomplish far more in the warehouse than you think, as our recent webinar from leaders in the field Geek+ Robotics illustrates.
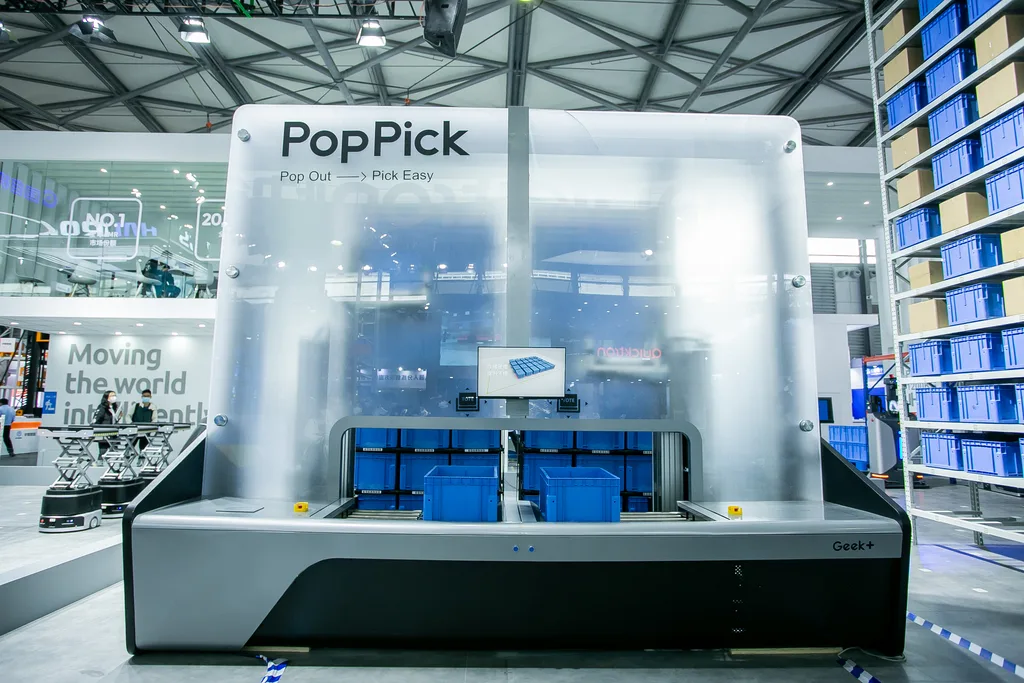
WHEN AMRS burst on to the scene a few years ago they provided a cost-effective, high throughput, modular and scalable way to revolutionise picking operations.
The benefits are the same today – low-cost and quick set-up, reduced exposure to the labour shortage, and greater efficiencies – but did you know that AMRs from Geek+ Robotics have matured into a sophisticated full spectrum of solutions?
These tackle warehouses processes including sortation, replenishment, cross-docking, high-density storage and more.
This webinar highlights the range of solutions and what they can do for your warehouse operations.
One example is the recently launched Sky-Storage & Ground-Pick solution, which combines ultra-high storage density to highly flexible picking. Four-way shuttles and P800 picking robots take advantage of vertical warehouse space without sacrificing picking speed.
{EMBED(1237638)}
Another is how Geek+ AMRs simplify cross-docking operations, where whole pallets are received and directly put away and picked without unstacking.
This is not just a hardware story. Geek+ Robotics robots are backed up with sophisticated AI-driven software that analyses and implements the right solution for you.
With over 500 global industry leaders as customers, the AMR pioneer has the data needed to power AI-driven insights and the real-world experience to implement seamlessly.
The robotic solutions can also be provided on a Robotics-as-a-Service (RaaS) basis to further help with affordability.
Simon Houghton, head of sales and marketing for UK and Ireland at Geek+ delivered the webinar.
Audience feedback
The webinar generated a lot of interest and questions from attendees.
One attendee asked about integrating Geek+ robotics with existing IT in the warehouse.
Simon Houghton said: “For goods-to-person systems, we have integrated with all of the off the shelf WMS providers, as well in-house WMS, and even companies that don’t have a WMS and are sending us across CSV files. We are very flexible in integrating with warehouse operations.”
Another topic that came up a number of questions was maintenance.
{EMBED(1237639)}
Simon explains: “Actually an AMR doesn’t hold that many parts, say 20-25 serviceable parts. It typically consists of a single shell aluminium chassis, drive wheels, some sensors, a battery. So as long as these serviceable parts are regularly maintained, typically there would be a visit every six months, the robots generally don’t go wrong too much.
“The good news with the system is that if one robot does go down, there is no single point of failure, the process will continue until you can resolve the issue with the robot.”
“For system and network issues, we have 24/7 coverage and response times that can as fast as 10 minutes.
“We do try to put in failsafe systems such as UPS, so if the power goes down, you can keep running. If IT systems go down, we can operate from the cloud.
“Generally maintenance is very low. You can train up users on site to provide basic maintenance. There should be minimal downtime.
“That’s one contrast to a complex conveyor based system. In that type of installation, a fault it can halt the whole system until it is resolved, but with a multi-robot AMR system, the remaining robots can continue to work while the problem is being resolved.”
Our attendees were also keen to know what applications best suited the robots. The AMRs are versatile and will suit a very wide range of operations.
Simon explains: “We have the robots deployed in eComm, 3PLs, grocers, but also in perhaps non-typical businesses, such as vaping companies, businesses processing returned mobile phones and much else.”
One attendee asked if the AMRs need to be used with specific racking and shelving solutions or if they can work with any storage format?
“It depends on the system,” says Simon. “Shelf to person systems do require a system that is engineered to work with the AMRs, for example, they’d have QR codes on the underside of the shelves. The fixed racking solutions, such as the tote-to-person systems, will use pretty much standard tote racking, although a couple of minor modifications are required at the lowest level. In those kind of applications, we would work be working with UK suppliers to source those solutions.
“The same applies to the pallet-to-person systems. Standard product is used with some small modifications required.”
Simon answers many more questions in the webinar session, which is available now on demand.
Simon concluded: “We have recently established a UK head office and demo centre in Daresbury near Warrington. So if you’d like to discuss an implementation, get in touch and we can set up a meeting there on at your premises.”
You can watch the webinar and Q&A session online at https://bit.ly/3dVRb9Y
There is no cost but registration is required.
{EMBED(1237636)}