Quick and easy options
Demand for warehouse space is outstripping supply and with no relief on the horizon, temporary buildings have been elevated to the status of essential strategic option for any warehouse operation that needs to pivot quickly.
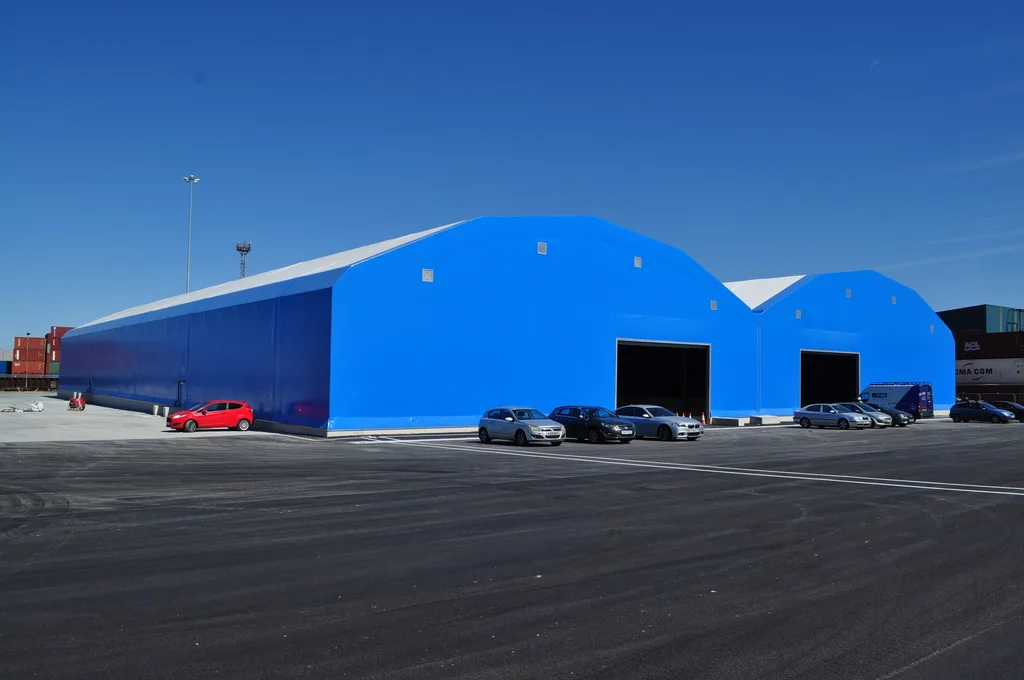
THE UNPRECEDENTED pressure we’re seeing on warehouse space shows no sign of abating. Savills recently reported vacancy rates below 3% and predicted rents will rise by around 26% over the next three years. At the same time new build has stalled, with landlord LondonMetric’s strategy director Andrew Smith indicating in a recent Savills podcast that rising interest rates, coupled with inflation and rising construction costs, have led to a decline in warehouse spec build, meaning developers will wait until occupiers are prepared to pay higher rents before ramping up new build again.
This makes the use of temporary buildings more important than ever in the warehouse and logistics market.
CopriSystems managing director Rate Colenso confirms this: “We’ve not seen pressure like this on warehouse space in our 30+ years in this industry and if you’re a business looking to expand in a rapidly evolving, highly unpredictable environment, you’re probably having to frequently and quickly re-evaluate how you can future-proof your strategy.”
So, how do temporary buildings help?
Rafe continues: “With traditional bricks and mortar, a five-year lease is not long but many businesses don’t have the money to commit to those timescales or the certainty that they can fix themselves to one specific location. Our structures are carefully and individually designed to lead a dynamic life so they can be relocated or modified to suit a business’ ever-changing needs.”
{EMBED(1238359)}
Disruption is the new normal and much of the supply chain has moved from just-in-time to just-in-case. With occupiers facing so much unpredictability, temporary and conventional warehouse buildings need to be designed in a manner that offers maximum adaptability and flexibility.
Rafe adds: “The trend for on-demand warehousing addresses what’s happening right now, but be sure to choose a building solution that can be easily modified without compromise when responding to altered circumstances.”
As well as the trend for on-demand warehousing, Rafe has also noted a shift away from consolidation and dependence on one big warehouse, with occupiers in the distribution industry looking to ensure that supplies to smaller towns can be covered from more than one location, at least for the time being.
Installation advice
While installing a temporary building is much faster and easier than a conventional building, there are a number of factors to consider for optimal implementation.
Roder’s Nick Sheldrick asks: “What’s going inside? If the building is for production, it’s worth opting for an insulated structure to maintain temperature, to look after your workforce and equipment, and reduce running costs.
“For secure storage where temperature isn’t a factor, a steel clad building with an inner roof cover to reduce condensation will normally suffice. While with transit goods or loading operations on a secure site, a simple weatherproof canvas covered unit or open canopy will do the job and last a long time.”
Also consider how much useable space you need.
Nick continues: “For a racked storage, space utilisation may be as high as 80%, and ensuring you have the right footprint to begin will save time and money later. Same goes for eave height: if you’re considering racking, then eave heights are available to suit for a very modest increase in cost.
“Warehouses are getting bigger and modular warehouses are no exception. Our own standard eave heights, previously topping out at 6.2m, now run to 8.2m; meanwhile while a 30m maximum clear span is still typical, we have recently installed clear spans as wide as 50m.”
Long-lasting structures
Although the solutions are classed as temporary or semi-permanent, they frequently last a very long time. Rubb tensile fabric structures can achieve a 25+ year design life. CopriSystems recently learned of a customer inheriting one of its canopies, which is 28 years old, and still going strong.
Rubb Buildings sales executive Steph Coyle, explains: “If you have not already considered semi-permanent fabric structures to facilitate growth, then it is definitely an option worth exploring. Many companies are unaware of the design capabilities our custom design tensile fabric structures can achieve, they are designed to suit wind and snow loadings to the geographic location of the site, just as a traditional building would be, with a 25+ year design life. As well as being suited to general storage space our buildings can be designed to achieve high level specification for requirements with temperature and humidity control systems, so although the solutions are classed as semi-permanent, they can still achieve specific configuration to suit the operational requirements of many businesses, we work across many sectors including storage, ports, aviation, sports and nuclear.”
Workflows
For those users concerned about maintaining workflows between the conventional and modular structures, Aganto managing director Andy Butters has advice.
“It is common for us to link the temporary building to permanent structures,” he says. “This means the occupier has the benefit of better flow of processes whether its warehouse flow, production line or cross-docking which becomes quite seamless, and also offers security and protection of goods from the elements.”
Andy has seen a big upturn in demand, that he puts down to being able to offer short to long term solutions at fixed rates.
“This way we bring value to businesses that need flexibility in operation, but certainty in terms of budgeting,” he explains.
{EMBED(1238360)}
Andy sees a temporary building as particularly attractive to companies that are lucky to have land adjacent to a building that would suit a temporary building and is not being used for anything purposeful.
“We take a very consultative approach, less sales focused, you come to us with the problem and then we’ll tailor a solution and guide you through the process,” adds Andy.
Looking to the future, what innovations are we seeing in the temporary building sector? Andy says there has always been a big focus on safety with structures.
“Suppliers are always looking at ways to reduce costs but safety has to be at the forefront. In terms of environmental impact, we are also always looking at new materials to help retain temperature.
“The same goes for the size and shape of the structures. Gone are the days when the product comes in a certain shape, size and spec, and that is it.”
This feature highlights a number of options and suppliers that can help you add flexibility to storage and operations. No matter your reason for considering these structures, one thing is certain, ‘temporary’ does not mean poor quality.