Automated palletisation for Mindful Chef
In 2022, BS Handling Systems completed the design, manufacture and installation of pick-to-light conveyor lines at the specialist retailer’s distribution hub in Redditch.
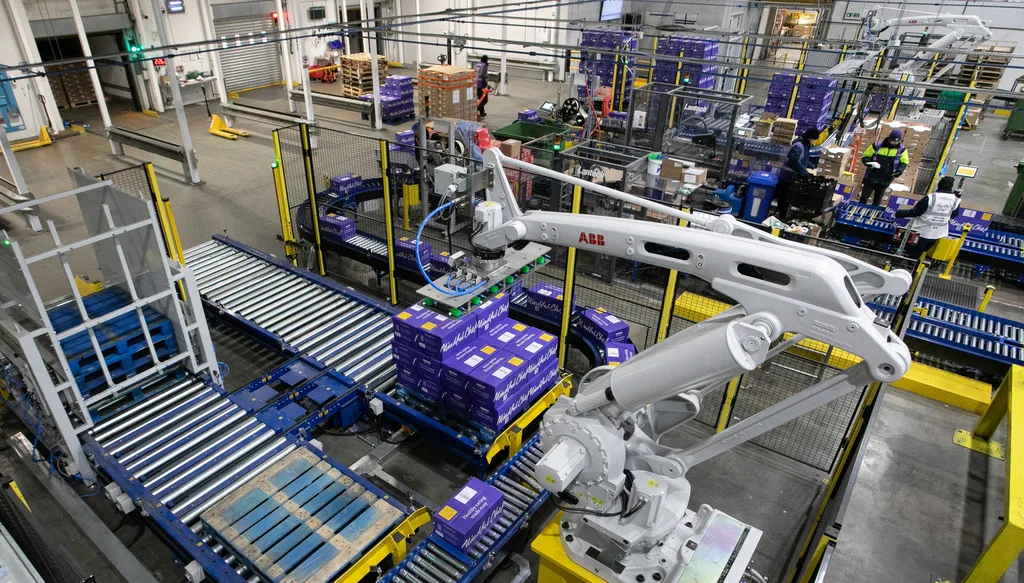
THE SUCCESS of the project led Mindful Chef to commission BS Handling Systems to deliver phase two of its development plans, an automated palletisation solution at the end of the pick-to-light lines.
Mindful Chef head of operations Matthew Maxwell explains: “Phase one was designed to increase throughput performance and reduce error rates in the picking process. With phase two, the key objectives were to reduce or remove manual handling operations at the end of the lines and further increase throughput speeds.”
Before phase one was completed, Mindful Chef had already started thinking about adding more automation to the end of the pick-to-light lines. With phase one the company achieved a throughput increase of around 30%. To cope with this increase it required two operators at the end of each line to manually lift the boxes off and palletise them prior to loading into a trailer for despatch.
Removing these manual handling elements at the end of each line would have several benefits:
- Reduce the number of operators required to meet increased throughput.
- Eliminate the health and safety risks to operators.
- Run continuously and accurately without the need for breaks.
- Improve the mental health of operators by giving them less repetitive tasks.
Matthew Maxwell again: “As part of our due diligence we visited other sites within the Nestlé group to evaluate their palletising operations. The benefits of automating the palletisation became obvious and so we pushed ahead with phase two of the project.
“A major advantage of working with BS Handing Systems is their flexibility. Even though we’d already committed to the order, they were open to change throughout the process. Following further analysis we decided to have two automated palletisation cells, one for each pick-to-light line.”
Mindful Chef has three box sizes in the operation, small, large, and extra-large. The conveyor indexes boxes which are presented to the robot in pairs if they are small or large, or one extra-large box. The robot picks up two boxes at a time unless they are extra-large (these are picked up one at a time). The robot continues picking up the boxes and stacking them on the pallet using a pre-programmed pallet configuration with eight boxes on each layer.
Maxwell explains: “It continues back and forth stacking the boxes until the pallet is full. It is very quick, extremely accurate and consistent. In terms of throughput we've seen around a 20% improvement with the automated palletisation. On the weekends; we've gone from 400 boxes an hour to nearly 500 an hour. We've also reduced operators at the end of the line from two on the weekend down to zero and midweek from one to zero. The removal of this manual handling element has boosted the team’s morale.
“We were expecting to have a period of at least two or three weeks of teething issues. In reality, however, everything ran smoothly. During peak the cells worked like a dream, stacking up to 12,000 boxes a day on pallets.
For more information, visit www.bshandlingsystems.com