Bespoke straddle carrier for drainage firm
JKH Drainage takes 35t capacity straddle carrier from Combilift to cope with increased volume of raw materials and finished products.
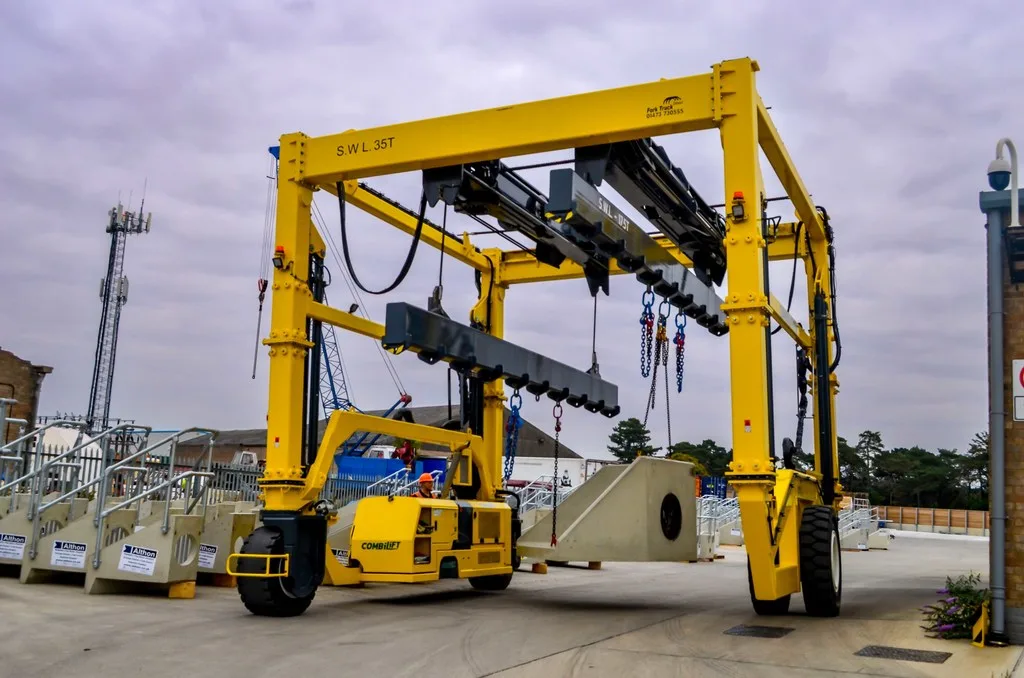
MANAGING DIRECTOR Daniel Prince explains: “Growth this year was at around 30% and we expect this to continue due to ongoing large infrastructure projects.”
When a move to a new site was in the planning stages, Daniel and his team looked at options for handling the heavier and bulkier products when they are demoulded inside the casting facility and taken to external storage areas. These currently weigh in at around 8.5t, but will soon increase to 12t in a single cast, so extra lift capacity needed to be factored in to any new equipment. Gantry cranes were initially considered but quickly discounted as they would have taken up too much of the already limited vertical space.
“We can move smaller, standard castings with our regular forklifts,” said Daniel, “but once you get above around 6t, or for bespoke oversized products that can have a footprint of 2.5 x 4m, this gets problematic as load stability becomes an issue. We therefore investigated the potential of a Combi-SC straddle carrier as recommended by Jimmy Pascavage of Fork Truck Direct.” Each Combi-SC is a bespoke unit to accord with the varied requirements of a customer’s specific application, and it took a fair bit of liaison between Daniel, Jimmy, Combilift’s SC specialist Stephen Wells and engineers at Combilift’s factory to come up with the final specs for JKH’s machine.
Largest castings
With a telescopic facility, the SC’s closed height of 5.5m enables it to pass through the 5.8m high doorway, where it has just enough clearance in the 6m roof space to lift the largest castings and take them to the outside storage areas. Chains can be connected to various points on the two side shifting beams mounted on the top of the frame and the full open telescopic height of 8.1m offers plenty of room for castings to be rotated and set down at the most suitable storage angle. The remote control model chosen by JKH offers very good all round visibility for one operator without the need for banksmen. Diesel power was considered the most suitable as the Combi-SC spends around 75% of its time working outdoors across the extensive site.
A compact counterbalance design Combi-CBE model is used mainly indoors for moving bundles of raw materials such as steel bar around the production area. Its multidirectional capability enables 8m lengths to be easily manoeuvered around confined spaces and tight corners, and a spreader bar was also supplied to allow stable handling of certain materials that are prone to flex when transported.
“These two products from Combilift have provided us with a high level of versatility when handling products indoors and out, as well as when we need to load them onto trailers for customer delivery,” says Daniel. “At 1.8 acres, our old site was much smaller, and the extra space represents a vast increase in business opportunities. We currently manufacture around 50t a day, and we wanted to future proof our handling procedures from the outset here, and this is exactly what we have done with the Combi-SC and the Combi-CBE.”
For more information, visit www.combilft.com