Choose your racking supplier carefully
With your warehouse’s success heavily dependent on your racking, SEMA explores what you should you look for in a supplier?
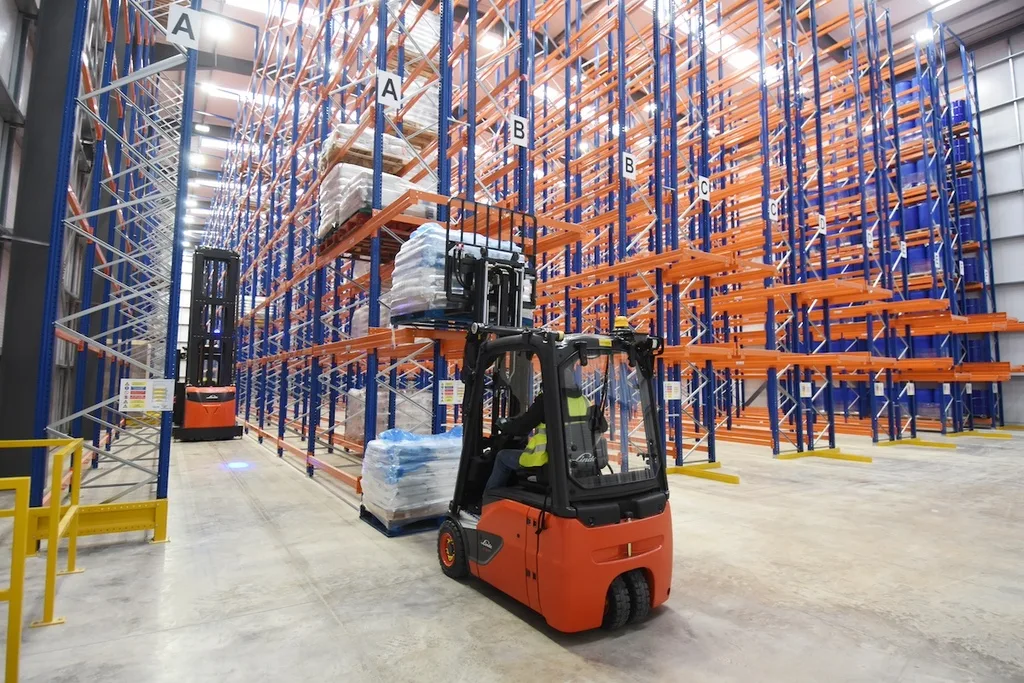
IF YOU’RE planning a new warehouse or looking to upgrade your current facility, one of the first decisions you’re likely to consider is what storage equipment to install.
While warehouse owners may only think in terms of how much stock it can hold, the design of your system plays a far greater role. Your racking is a long-term investment and getting it designed, manufactured and installed to your exact requirements will enable it to become the workhorse of your workhorse.
How can warehouse racking boost productivity?
Before selecting any storage solution, it’s essential to understand the specific challenges and objectives of your operations. Conduct a thorough analysis of your warehouse to identify any potential bottlenecks, inefficient picking processes or underutilised space. You also need to look at how many pallets or products will pass through the warehouse and the type of stock you are holding.
The next step is for your supplier to take this information and design a storage layout that addresses your requirements while also enabling stock to move seamlessly through the warehouse. From the moment stock arrives at the bay door, heads to the racking and packing zone before leaving for despatch, the journey should avoid any sticking points. Get this right and you can speed up the process while also reducing the chance of stock damage. The design should also consider requirements for any equipment used to speed up processes such as automation and AI. Your racking should be compatible with any new technology while also allowing enough space between the aisles to allow the transporting or lifting of products.
Can your racking reduce costs?
There is no escaping that investing in new racking for your warehouse is a significant financial commitment. There are always companies out there offering ‘cheap’ solutions, but making the wrong decision can significantly impact the cost-effectiveness of your structure.
Aside from the cost savings that can be made by improving processes and speeding up order pick times, the design of your structure can boost your budget in several other areas. Smart racking design can significantly reduce operational expenses. For instance:
- Stock Protection
Lost or damaged stock is a wasteful expense, and you need to minimise both happening. The correct type and design of racking should ensure your stock sits securely on the shelves, is easy to locate and can be picked without increasing the risk of damage.
- Accident Prevention
Knocks and bumps to your racking structure from handling equipment and forklift trucks are almost inevitable. Damage to your racking can impact heavily on the safety of your structure and therefore must be repaired. If your equipment is constantly getting damaged the cost of repairs can soon add up. The design of your racking should calculate aisle widths and turning radii to minimise the chances of an impact.
- Maintenance
At some point over its lifetime, your racking will need repair work due to everyday wear and tear. While these are unavoidable, it is possible to reduce unnecessary repairs. Design the racking for its intended purpose with an installation that meets the manufacturer’s specification, and it will minimise wear and tear and reduce repair frequency.
- Business Growth
One last area for consideration when looking at how your racking can be cost-effective is through the flexibility of your structure. A system designed for growth should enable you to expand or modify your storage layout as your business evolves and avoid the costs associated with moving or replacing your racking.
Warehouse safety
As the warehouse owner, you are responsible for the safety of your racking system. Engaging with a supplier who cuts corners, doesn’t prioritise safety or doesn’t meet the latest industry standards can lead to costly consequences. It can increase the risk of your racking failing which will put your employees at risk.
While many racking suppliers showcase safety accreditations such as ISO, CHAS, and SafeContractor, these certifications primarily demonstrate compliance with general health and safety standards rather than expertise in racking design and installation. Within the UK, racking guidance can be found in both ‘HSG76 Warehousing and Storage: A Guide To Health and Safety’ and SEMA Codes. While it is not a legal requirement for suppliers to follow these standards if an accident did occur and the HSE were to take enforcement actions they would, in all likelihood, reference these documents, in conjunction with the legislation detailed above, as a framework to bring action against your business.
Is your racking supplier meeting all the areas we’ve covered? When designing the structure, are they working with either the SEMA Code or the European Code EN 15512? Have they got the correct insurance documentation in place? Do they know the latest industry standards? It’s important you check their credentials, for the safety of your workplace.
Why should you work with a SEMA member?
Working with a SEMA member can save you a lot of the legwork that goes into checking the skills of your supplier. SEMA was formed over 50 years ago by racking manufacturers who wanted to provide a benchmark for the industry. Today, the association is formed by SEMA-approved manufacturers, suppliers of racking equipment and suppliers of complementary safety measures.
Membership with SEMA isn’t bought—it’s earned as a mark of excellence. To join, SEMA Members undergo independent audits that check their work meets the highest industry standards. Through the process, we check they are working to SEMA and industry standards, conform to over 40 regulations, health and safety requirements, industry standards and legislative requirements. The audit also checks each supplier has the correct legal and insurance documentation in place. To ensure they continue working to our high standard, we repeat the process every three years. Any company that fails to meet our standards is asked to leave.
SEMA is made up of Approved manufacturing and supplier members. The work of each member is interrelated which enables our supplier members to have privileged access to the technical departments of our manufacturing members and qualifies them to conduct work on behalf of SEMA Manufacturer Full Members.
Whether you worked with one of our Manufacturing or Approved members, through their SEMA badge you can be confident you have a supplier who is meeting the highest levels of safety and quality. The next time you’re looking to install new or upgrade your racking, why not avoid making an expensive mistake and get in touch with one of our SEMA Members?
For more information, visit www.sema.org.uk