Drive solutions for forklifts, AMRs and AGVs
Bonfiglioli’s participation in LogiMAT reflected its focus on key trends emerging in the intralogistics sector.
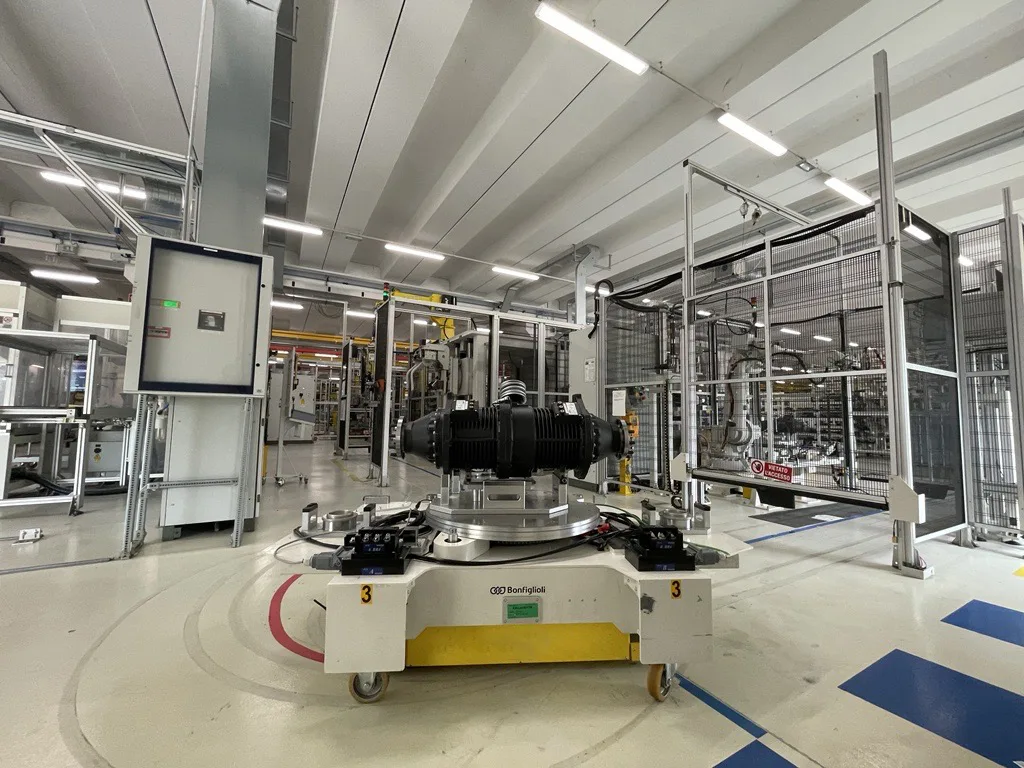
THESE SOLUTIONS include the continuous improvement of battery-powered motors, the rise of autonomous guidance for warehouse machines – with the development of customised systems for AGVs and AMRs –, and the sensorisation of machines and drives for more accurate machine performance monitoring and the integration of predictive maintenance functions.
Bonfiglioli presented its Logistics Automation systems showing a wide range of systems conceived for warehouse equipment, AMRs, forklifts, smart conveyors and automatic storage systems.
For the intralogistics sector, Bonfiglioli develops comprehensive systems featuring mechanics, electric motors and electronics dedicated to (counterbalanced) forklifts/lift trucks and warehouse machines. Especially for the former, Bonfiglioli is one of the leading manufacturers of drives. Te high-efficiency, low-noise electric planetary drive of the 600F Series and the 610 electric dual drive dedicated to heavier machines and capable of increasing the precision of the machine, making the maneuverability easier in tight spaces, is showcased and coupled with high performance electric motors – BPM – for material handling vehicles. Compared to traditional induction or asynchronous motors, permanent magnet motors ensure an efficiency improvement of 10-15%, which results in lower battery consumption, thus extended autonomy. In terms of power, these motors range from 1 to 100 kW, moreover, their transmissions are particularly low noise, thanks to the power honing technology applied to the hard fine finishing of gear profiles.
Selcom
For forklifts, a DC/DC converter and a TFT touch screen engineered by Selcom are showcased. Selcom has also designed and developed the electronic board integrated in the wheel group present at the booth. Part of the Bonfiglioli Group, Selcom specialises in the design, production and sale of custom high tech electronic solutions, such as motion controllers, PLCs, sensors, displays and inverters for drives and power transmission gear motors, which meet the highest market standards. Selcom’s solutions include the integration of controls into electrical driving cabinets, being the result of its extensive experience in designing products not only tailored to individual customer needs, but also capable of anticipating market trends and demands.
Ideal for warehouse operations, the EL Series identifies steerable powertrains for pallet trucks, stackers, reach trucks and other types of warehousing machinery requiring high maneuverability in tight spaces. The series is displayed in EL9 and EL 16 sizes, the latter featuring a torque of 2,500 Nm and capable of supporting loads up to 4.5 tons. The EL Series is coupled with permanent magnet motors.
Make way for AMRs
In the applications for warehouse and material handling an important role is played by Autonomous Mobile Robots. For AMRs Bonfiglioli has designed BlueRoll Platform, the precision wheel drive marked a compact and energy-efficient design to ensure prolonged operational cycles. Available in three configurations – Basic, Advanced, and Compact – BlueRoll can be easily installed within axle space and boasts enough torque capacity to move up to about 1 ton per drive wheel. Featuring a compact low voltage precision planetary servo gear motor compatible with electronic drives with 24 or 48-volt batteries, Blue Roll is the ideal solution for easy installation and retrofit, as it adapts to any AMR design. On display is a Helko AMR which is the result of the cooperation between Bonfiglioli and Eureka System S.r.l. and is powered by Bonfiglioli’s motorised wheels and an electric drive in a tailor-made approach.
Low voltage gearmotors
One of the most spotlighted products is the 3-phase synchronous permanent magnet motor of the BMD Series. This low-voltage motor is characterised by compact dimensions and low/medium inertia, it is suitable for high dynamic industrial applications, AMRs and shuttles and at LogiMAT it is showcased in four different sizes, according to their corresponding applications. BMD is brushless, permanent magnet, low-voltage (24 to 48 volts) but highly efficient motor and offers an additional advantage besides low voltage: unlike traditional stepper motors, it is not a DC motor but a three-phase AC motor, delivering exceptional performance and excellent torque values. For material handling operations, where the current trend is to replace fixed conveyors belts with mobile applications, The BMD represents the ideal solution for shuttles: one features a helical bevel gearmotor of the A series and a servo flange: a winning solution because it incorporates a very compact gearmotor, still featuring a helical bevel gear technology, with a low-voltage yet high-efficiency motor. Even the second, larger and more powerful one is composed of a BMD brushless motor and includes a helical parallel shaft gearmotor of the F Series which is an outstanding solution for customers looking for a drive that can maximize mounting flexibility. Finally, the steering group for AGVs/AMRs forklifts, consisting of a BMD motor and a precision planetary gearbox of the MP Series which offers great modularity due to multiple design configurations, wide ratios range, two backlash classes and different optimized lubrications.
Smart conveyors
In the field of logistics, Bonfiglioli offers complete systems capable of supporting post & parcel material handling. For smart conveyors, three helical bevel gearmotors of the A Series are presented on a demo, each of them with three different torque ranges – A10, A20 and A30, respectively coupled with asynchronous IE3 electric motors and synchronous reluctant IE4 motors with sensorized decentralized inverter which has been specifically developed for post & parcel handling systems. The inverter acts as a sort of control unit that communicates with the sensor integrated in the gearmotor, responsible for carrying out the predictive maintenance, i.e. IoT functions. The on-site collected data are then sent to Bonfiglioli’s PC system with Profinet-based fieldbus.
More than a standard: Evox CP platform
Bonfiglioli presented the EVOX CP range, its latest helical in-line gear unit. Thanks to its wide selection of versions and options, EVOX CP can be seamlessly adapted to any machine requirement. EVOX CP combines reliability, ensured by top-quality components, with high mounting flexibility. It boasts a smooth surface and a standard-aligned mechanical footprint that makes it interchangeable with any equivalent product on the market. Another plus is represented by the absence of the oil breather. This means that the gearbox can be mounted in any position with the same oil level, reducing the number of configurations. EVOX CP Series is coupled with the IE3 MXN three-phase asynchronous motor, a compact and globally certified solution delivering modularity and reliability. Moreover, due to its 9-pin terminal box, the MXN motor offers 4 voltage combinations instead of 2, ensuring efficiency and adaptability to all voltage configurations.
Eyes on Axiavert, premium frequency inverter
Last but not least, eyes are also on the premium frequency inverter AxiaVert which is presented in four frame sizes. Thanks to its modular design, AxiaVert is a drive which offers seamless integration into any Bonfiglioli technology and automation networks, as well as compatibility across an extensive range of Fieldbus protocols, both on serial and Ethernet ones, fostering production optimization in accordance with Industry 4.0 standards. Bonfiglioli’s AxiaVert prioritizes functional safety, therefore, it offers all the main safety functions required by the market: STO, SS1, SBC, SLS, SLP, SOS. Its different Functional Safety variants allow to optimize configuration, reducing the need for external safety components and ensuring a safe and controlled operation to minimize standards. Bonfiglioli’s AxiaVert represents the best integration of the Fieldbus EtherCAT FSoE communication, which eliminates significant labor and cabling costs by carrying all safety communication between the inverter and PLC over the fieldbus.