Five steps for racking that boosts warehouse productivity
Anyone working within the logistics sector will be all too aware of the challenges facing the industry. You need a warehouse that performs at peak efficiency, can maximise storage capacity, increase productivity and boost turnover.
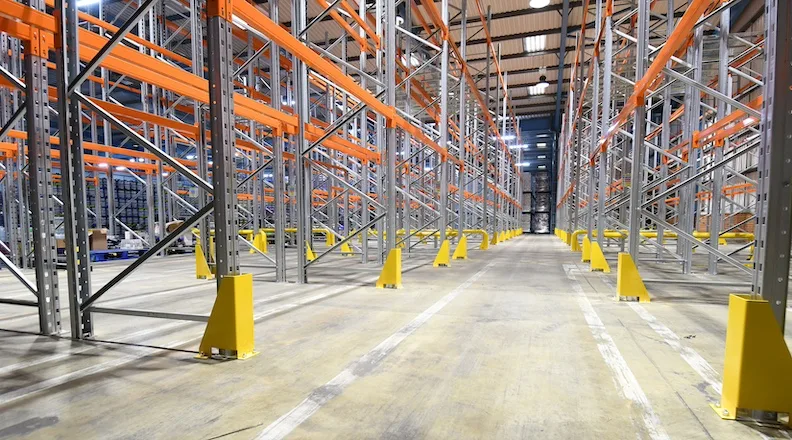
MEETING THIS wish list of requirements is no small task, yet a solution can be found when you design, install and maintain the right type of racking for your business.
As a leading voice within the racking industry, here at Storage Equipment Manufacturer’s Association (SEMA) we know there are five simple steps warehouse owners should address when looking at their racking.
Step 1: The right racking for the job
A warehouse is, in most cases, an empty box waiting to be filled with storage equipment and stock. As the backbone of your warehouse, your choice of racking can provide a significant boost to your productivity and profitability.
Yet, in today’s modern warehouse, the logistics industries has become busier than ever. Warehouses are running at full capacity and there is increased pressure for your racking to perform to ever higher levels:
- Changing dynamics: warehouse units now range anywhere from a micro hub that manages last-mile delivery orders to a 3PL or 4PL big shed. Storage system requirements can go from a few simple shelving units to large-scale racking reaching 20m in height.
- Maximising your space: while standard pallet racking is the most commonly used storage equipment within the warehouse, they are not the only option. There are plenty of options available that can provide solutions for your space for example, multi-tier racking can efficiently fill the height of your warehouse while drive-in systems offer high-density storage within a smaller footprint.
- Automation: advanced technology has become a regular sight within the industry. Yet implementing it to maximise productivity and create gains requires careful planning with your racking supporting any automation, conveyors or Warehouse Management Systems (WMS) to deliver on maximum results.
- Multiple warehouse tasks: not only does a warehouse need to process orders but, as a multi-functional space, it needs to encompass additional tasks. Racking should enable you to create zoned areas that seamlessly complete different tasks such handling returns, meeting stricter recycling standards or effectively managing stock fluctuations.
- Safety: while juggling these multiple requirements your racking must also help your business to stay safe. You need a racking solution that provides a safe working space for employees so they can expect to arrive at work and go home safely at the end of each shift.
Step 2: choose your supplier carefully
This growing complexity of the modern warehouse means your racking is not a decision to be taken lightly. You need a system which has been precision-engineered and designed to boost the performance of your warehouse.
The problem for warehouse owners is that the racking market is a competitive industry. While suppliers may have impressive-looking websites and images of previous work, it doesn’t provide guarantees. It won’t tell you if their racking design will meet your exact requirements, ensure you meet your legal requirements while also ticking the health and safety boxes.
So how do warehouse owners find a supplier they can trust?
This is where SEMA can help. We were established over 50 years ago to provide clarity to the industry and save warehouse owners the leg work of checking their suppliers’ credentials.
Formed by racking manufacturers and supplier companies, the association is open to anyone who can demonstrate their commitment to meeting high levels of safety and quality standards. A member can only join SEMA as an approved member once they have passed an in-depth audit which checks the supplier covers five key areas. It determines if they are working to industry regulations, SEMA Design standards and relevant Codes of Practice. It also checks they conform to health and safety requirements, have the correct insurance in place and reduce their environmental impact. SEMA members also commit to using SEIRS installers and SEMA Approved Racking Inspectors (SARI).
Step 3: Inspection, inspection, inspection
Once your racking is in place and loaded, it needs looking after. Not only will this help you to improve the longevity of your racking, and maximise your ROI, but it is also a Health & Safety Executive (HSE) requirement. Your warehouse racking is classed as work equipment and under the Provision and Use of Work Equipment (PUWER) and HSG76 Warehousing and Storage: A Guide to Health and Safety you are required to maintain the structure.
A lot of warehouse owners are aware of their requirement to get an Expert Inspection. This inspection should be conducted at least once a year by a qualified professional. However, you should be aware that there are two types of professional rack safety inspection available – a damage report or a report by a SEMA Approved Racking Inspector.
A damage-only report provides you with a damage list and possibly the location of the damaged areas. However, a SARI report goes into greater detail and provides useful information for warehouse owners. It will look at the suitability of the storage equipment and mechanical handling equipment, load stability, rack configuration and compatibility of the racking. It will then provide a list of issues with timescales for corrective action.
Step 4: In-house Inspections
The racking inspection process doesn’t start and end with the Expert inspection. If you look at HSG76 they follow the guidance set out by SEMA by recommending you conduct regular in-house inspections.
The process starts with any employees working in areas with racking. They are in the ideal position to quickly spot issues or signs of damage on the racking. They should receive training which equips them with the skills and knowledge they need to identify different racking damage.
You will then need to nominate one of your employees to conduct the Regular Inspection. They will take on the role of Person Responsible for Racking Safety (PRRS) and at least once a week they will perform a visual inspections which checks Load Notices are fixed to the racking, maximum loads are never exceeded, correct usage and look for signs of rack damage. They will also maintain a written record of the inspection which will form part of your official maintenance documentation. To prepare them for the role, send them on training such as our Racking Safety Awareness course.
Remember, Regular Inspections are your responsibility and you could risk harsh penalties by the HSE if you fail to meet your obligations.
Step 5: Training, training, training
At SEMA, we know training is the cornerstone to delivering on racking that boosts your warehouse. After all, if your racking doesn’t work as intended or has to be put out of action due to damage, it will be costly for your business. That is why we have developed training courses covering key stages over your racking’s lifetime.
Our courses cover three key areas:
Racking in use:
Our Rack Safety Awareness course is for your employees who work in areas with racking. It has been designed to provide the skills and knowledge they need to carry out their duties safely and conduct inspections. The one-day course covers types and frequency of inspections, responsibilities of users and suppliers, legislation, recording an inspection, potential damage levels, understanding load notices and action points. We run two courses that cover either pallet racking or cantilever racking.
Racking installation and repair
When your racking company supplies your equipment, the design will come with critical information that ensures the stability and safety of your structure. The racking installers must accurately follow this specification. The problem is, a lot of installers within the industry still ‘learn on the job’ which means they may never have learnt the correct installation techniques. To solve this problem, SEMA set up SEIRS which is a training scheme for installers of racking equipment.
The course trains racking installers on correct installation methods in accordance with SEMA standards, manufacturer specifications and codes of practice. They must also attend a refresher course every five years. This means any installer holding a SEIRS card can prove they have the skills and knowledge to safely and correctly install your racking.
Racking inspection
Expert racking inspections are crucial for keeping your racking safe, ensuring it continues working as intended and avoiding unnecessary repair costs. To address these key areas, you need to rely on the expertise of your racking inspector. This is an who is qualified in their profession and has a knowledgeable understanding of racking structures.
To provide a benchmark for the industry, we set up our SARI qualification which is for professionals who conduct third-party rack inspections and want to uphold a high-quality standard in their work. Inspectors can only earn their qualification once they have completed an intensive three-day training course and successful completion of both a written examination and practical assessment. To ensure SARIs continue to meet our high standards they must commit to ongoing Continuous Professional Development (CPD).
If you would like more information on getting new racking or maintaining your current storage equipment, why not get in touch for more information by visiting www.sema.org.uk or emailing enquiry@sema.org.uk.