Get proactive on safety
The servicing and maintenance of loading bay technology should be top of the list for operator and site safety, says Phil Clark.
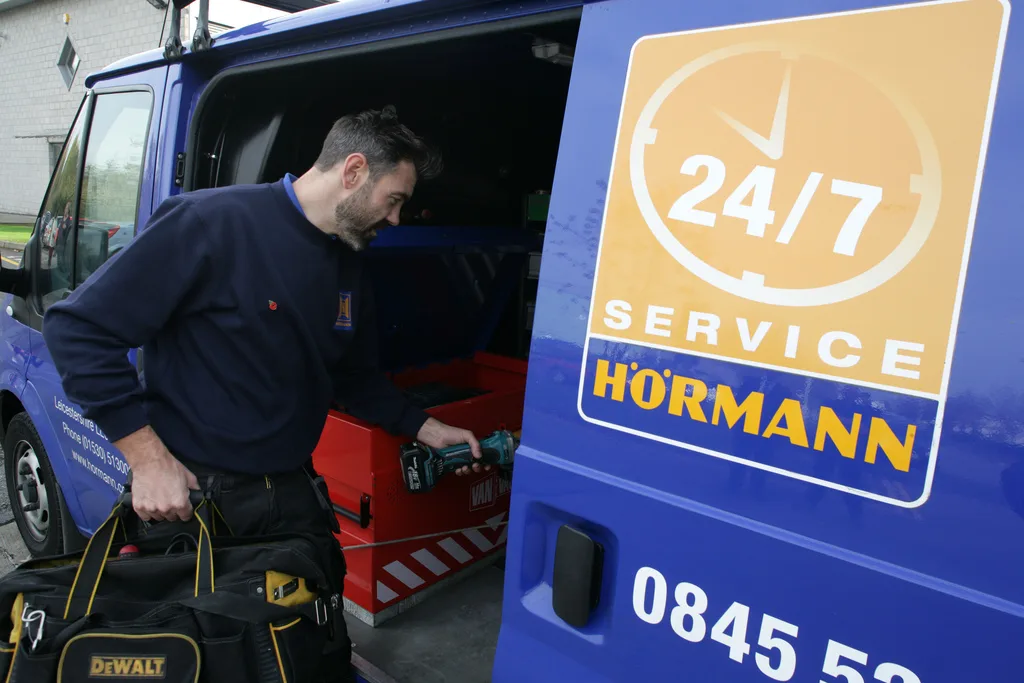
THE NEVER-ENDING growth of online shopping and the increasing need for companies to offer unrivalled delivery options has resulted in relentless pressure to ensure that logistics facilities constantly operate at full capacity and potential downtime is eliminated.
In response to this busy environment, logistics operators should be taking preventative measures to ensure the overall safety and efficiency of their site, with a regular schedule of service and maintenance helping to ensure that any potential faults and issues can be dealt with in a proactive manner.
While the Safety at Work Regulations do not specify a set number of times that industrial doors and loading technology should be serviced, Hörmann UK recommend that servicing should take place at least twice a year, and more often in high usage areas. At Hörmann we are constantly working closely with clients and end-users to develop tailor-made solutions and service programs to suit their specific requirements.
Our standard, bi-annual service consists of a comprehensive check regime that is undertaken to ensure that any potential issues with the technology are unearthed. Ensuring that every aspect of the loading bay is functioning correctly, 30-40 different areas are checked and analysed. From this rigorous procedure, the Hörmann team can provide up-to-date information to improve safety and the overall operation, and if a certain type of fault is occurring frequently, our service engineers can draw on global experience to design and develop bespoke solutions.
{EMBED(1228780)}
To ensure that a warehouse can be back to full operation as soon as possible service teams need to be responsive and be able to attend a property within 2 to 4 hours of a fault or accident occurring. With a nationwide team of engineers available 24/7, Hörmann are ideally placed to respond to the demands of time-critical operations. The Hörmann service team keep a large and varied supply of maintenance consumables in their vans to enable them to fix most issues, but we also recommend that the warehouse site itself keeps a critical spares holding – helping to save time as spare parts do not have to be ordered-in prior to the repair being carried out.
By using a Hörmann service engineer, clients are assured that they are using a specialist who has expert knowledge of the loading systems and doors and will only ever use Hörmann parts, ensuring that complete operational integrity is maintained. As an OEM, all parts are manufactured by Hörmann meaning there is no reliance on third party suppliers. With our systems being open parameter and all technical and service-related information available on-line, clients and trade partners have instant access to vital support information.
While the service engineers are the visible face of the operation they are supported by a dedicated team behind the scenes – a large and experienced department committed to planning, provision of spare parts, technical advice, and training. The launch of our training Academy in 2019 further represents part of our commitment to support the next generation of engineers through free first-class training.
There is no doubt that the logistics industry is set to continue on its impressive growth protectory and is set to become even busier over the coming months and years. Hörmann is in an ideal position to support the market in meeting the demands of this expanding market by providing service and maintenance support that places operator safety at its core.
Phil Clark, industrial service manager, Hörmann UK
For further information, visit hormann.co.uk