Meeting tough challenges head on
It was no picnic when Europa Warehouse opened a huge new facility during the pandemic, especially as it included a significant automated component. Europa Worldwide Group chief operating officer Dionne Redpath talks to Logistics Matters editor Simon Duddy about how the firm worked through the challenge.
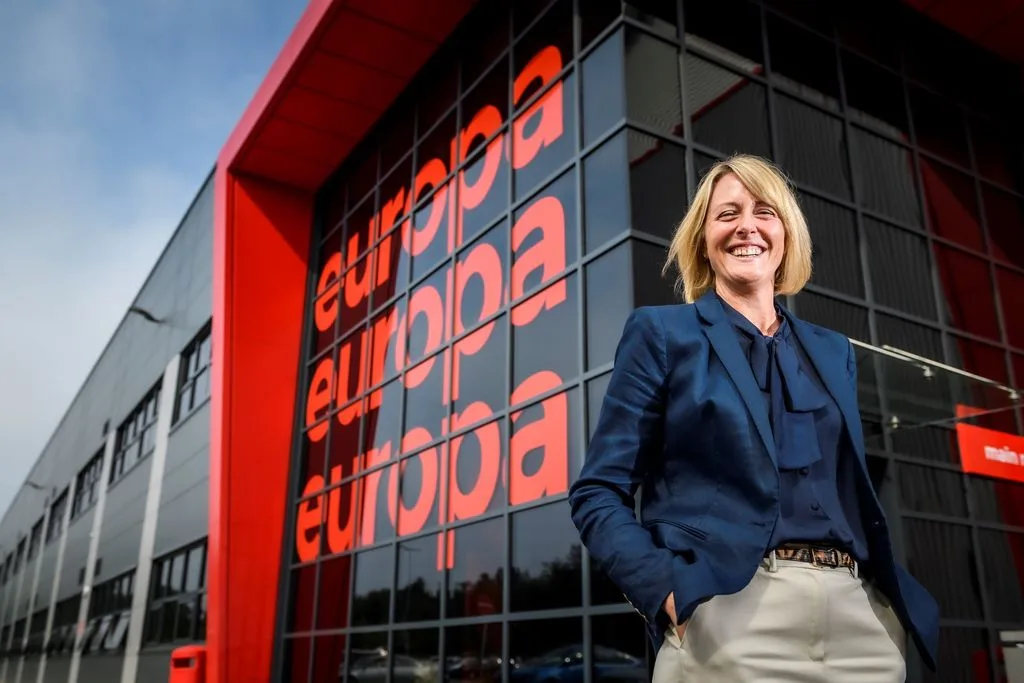
COMPLETING ITS Corby site right in the middle of the Covid-19 pandemic, when social distancing was being enforced was a massive challenge. Fortunately, Europa was given frontline worker dispensation because it was providing crucial services, not least a contract to provide the NHS with PPE.
As well as the construction element, the existing workforce from the previous site in Northampton, a considerable distance away, had to be migrated to the new site.
Dionne explains: “We had to hit the ground running because, as we took early occupancy, we were bringing product into the building. NHS PPE was coming on to this site as the racking was being erected. Operating in that environment, you can imagine the challenge placed upon our people. It was really demanding.”
That is not all. As an operator with considerable clients in the drinks industry, the pandemic driven boom in alcohol sales led to additional challenges. At the height of the pandemic, Europa had 4-500 people working on site to keep up with demand.
“In addition to Covid, there was Brexit,” says Dionne. “The availability of labour locally proved to be very challenging. So every day, we were trying to fulfill customer requirements with, not far off, a whole new team. I'm going to say this is candidly as I can, we could have done a better job of looking after our teams.”
Engagement
This led Europa to rapidly ramp up engagement initiatives with employees in Corby. This included boosting the skills of managers and team leaders, starting an Employee of the Month scheme and introducing the I hear a Whisper campaign. The latter allows employees to highlight when colleagues are going above and beyond, and ensures they get recognition and reward.
Dionne explains: “During the pandemic, the agency contingent could pick and choose wherever they wanted to work from one day to the next. We have had to work hard to ensure our pay and conditions are at the right level to retain people. I think our reputation in the market has dramatically improved as a result.”
Dionne also praised the way Europa is organised, with HR and finance specialists supporting leaders on a site-by-site basis.
“Having a HR business partner on site means you have got somebody with real expertise in all matters HR to support the site management team,” she says.
“We’ve been doing it for a few years and it's been very successful. I know my guys really value having that expertise as part of their team and they can focus on customers, their team and deliverables.”
Automation
While the pandemic brought workforce issues to a head, the work Europa has done from an automation perspective has been very effective in this regard.
Dionne explains: “Before we had that automated kit up and running, we would need three times more people. With a manual solution only, we might not fulfill all of the requirements for the day, even when operating night shifts.”
Europa embarked on its automation journey soon after it moved into the building. The system is based around a fixed automation installation from PSB Intralogistics and it gives Europa the ability to be able to pick significant numbers of complex, high-SKU orders with very little labour input. It allows Europa to store product in totes in the mini-load and has the capability to achieve 100k picks per day.
“We have a dedicated engineering team to make sure that the machinery runs smoothly, because it's very important that we minimise downtime,” says Dionne.
“You need a level of expertise to operate that successfully. We've nurtured that and the team does a brilliant job for us.”
When implementing a £12 million fixed automation system, it is unrealistic to expect it to work perfectly from day one. Europa had the expected teething problems and, while it picked its first bottle in August 2021, the initial period of use was challenging.
Dionne takes up the story.
{EMBED(1255934)}
“As I became more closely involved in the division, I felt very passionately that we had to completely get to grips with it.
“We got down on paper a list of every single component, part or process that needed to be improved, and in our snappily entitled Get the Automation Monkey Off Our Back Meetings, which became known as our Monday Monkey Meetings, we would tackle these.
“We called time on that process in June 2022. From then we’ve hit really sensational numbers for our customer.”
Before the automated system was managed through lots of meetings by committee, with rooms full of people. The key to the monkey meetings was taking that down to a much smaller group of people who were ready to take responsibility for solving each issue. The streamlined meetings provided a laser focus, prioritising issues, discovering what obstacles stood in the way and assigning ownership to solve problems.
It is understandable with a high stakes new implementation to have all of the stakeholders present, in case you miss something. It was a brave management process tweak to pivot to a smaller team that could quickly action necessary improvements. But it paid off handsomely at Corby.
Dionne enthuses: “It was a breakthrough moment, as people were empowered and trusted to go away and make their respective actions work. It allowed us to move very swiftly forward. The team deserve all of the kudos for that.
{EMBED(1255933)}
“It sounds silly, but giving it a daft name, helped. It sticks in peoples’ minds. Secondly, it makes quite an arduous task, not exactly fun, but it gave it a new energy. People had been involved with the automation project for a long time, and had done a great job, but more was needed.”
Dionne has spearheaded such demanding projects before, notably Europa Flow, for the Road Division, which was launched in response to Brexit, allowing customers to use DDP (Delivered Duty Paid) incoterms when shipping to Europe.
Europa Road had very little customs expertise as a business before, and had to build that capability from scratch.
Dionne explains: “We set up a team in the UK and facilities in France and Belgium. We got global VAT accreditation, global VAT numbers, all of the customs and software processes etc. We built up a really slick process.
Europa is best known for its road services and is a new kid on the block on the warehouse side.
Dionne adds: “We are not scared to invest and innovate. There is more that we can do at the Corby site and in 2022, the Warehouse division announced its intention to grow footprint by a new building every two to three years. The market has changed since but that is something we have our sights set on.”
Nursery
One avenue for growth is targeting the shared user market. To tackle this, Europa has developed a nursery warehouse. Situated on a mezzanine at the Corby site, this provides a shared user space for smaller eCommerce customers. It allows businesses to utilise the scale of a larger building, but with costs aligned to a small business.
Dionne explains: “It's one thing if you are a Marks and Spencer and you need to take your own bespoke facility. But if you're not in that place and you don't want the hassle and expense, it’s a good option, particularly for eComm businesses as they are often dealing with high levels of volatility in orders and forecasts.”
In another example of looking to the future, Europa is a silver sponsor of Generation Logistics. The initiative is driven by industry bodies working in partnership and aims to attract the next generation of talent to the logistics sector, to fill the vast number of exciting roles that are opening up.
{EMBED(1255932)}
Dionne explains: “I think the logistics sector has had its profile raised. During Covid-19, key workers in the warehouse and on the road helped keep the country on track.
“Generation Logistics is really capitalising on that increased awareness of the sector generally, and targeting a younger audience. What is logistics? It's maths, it's science, it’s IT also. We have 90 developers working for us. I think logistics is a great sector for a management trainee.”
As we have seen in this article, logistics does not lack exciting roles with complex, high-stakes challenges to test the bright, young minds of the future.
For more information, visit www.europa-worldwide.com