New class of air purification systems
Q&A with Ben Simons, Zehnder Clean Air Solutions.
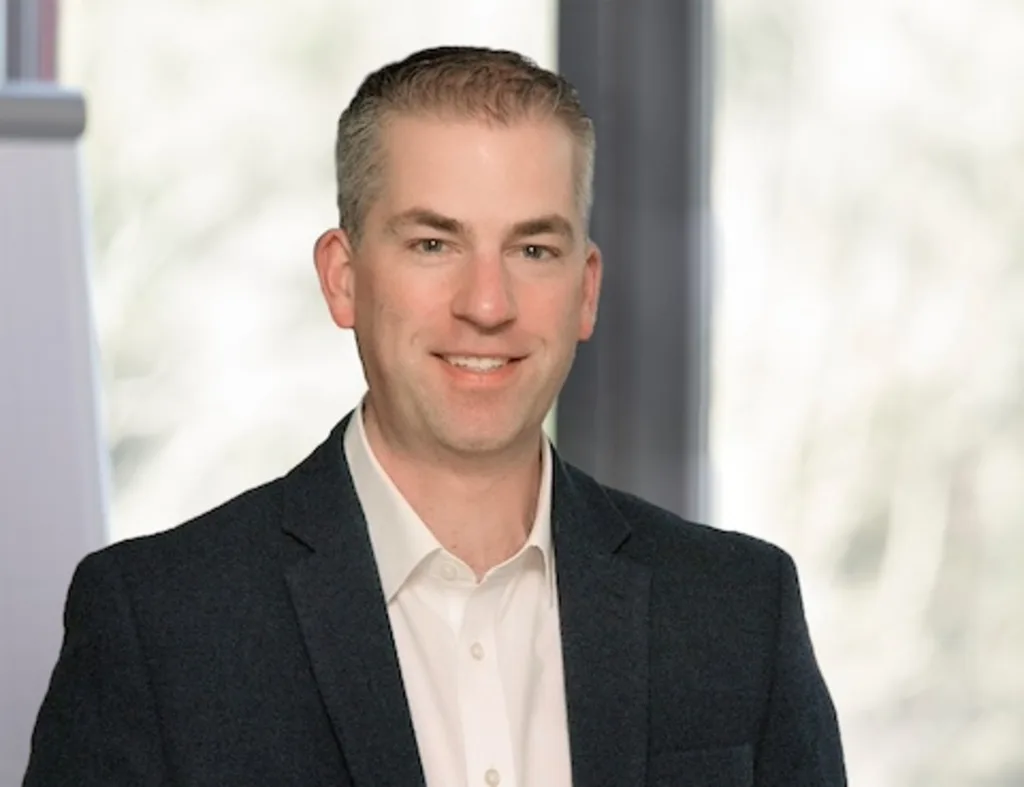
Q Firstly, who are Zehnder Clean Air Solutions?
A The story of Zehnder Clean Air Solutions is in many ways the story of many successful businesses in the logistics industry, firstly curiosity leading to an accidental discovery, which in turn led to the creation of whole new class of air purification systems.
It all started in the late 1990’s when an elderly Swedish filtration engineer was playing the filter fibres and worked out that by laying them vertically to the airflow rather than weaving them horizontally that he could hold a capture a huge amount more dust than with a conventional filter. By accident the Flimmer Filter was born. But frankly, to begin with he didn’t know what to do with it, so with family and friends they began to ask around, to see who may have dust problems locally. One of their very first cases was a distribution centre for a bakery who had chronic dust caused by the forklifts, concrete floors and poor ventilation. They had to spend team cleaning boxes before they were shipped from their ambient or frozen area and it was taking up time and money they could ill afford.
However, by twinning the Flimmer Filter with a fan to move the air, they found they could attract that airborne dust into the filter and so reduce the dust present in their work areas by a huge amount. This meant they were able to get the staff onto more productive tasks rather than cleaning, but also improved the whole image and hygiene of the site. It also meant their employees were able to work in a healthier environment which as we know from many studies over the years really benefits morale and productivity.
And the rest as they say is history, that customer told others and the business grew very organically in Sweden, so much so that in 2007 the Zehnder Group purchased the business and turned it into Zehnder Clean Air Solutions. A lot has changed since then but the same principles apply today as they did back then – we are problems solvers for our customers and we innovate with our technology in order to achieve that.
Q So what does your business look like in the UK?
A Well after Zehnder took over and invested, the business grew rapidly, to the point where in Sweden the category of ‘industrial air cleaning’ is recognised as a normal investment for most logistics organisations. When a new warehouse is built in the Nordics, people tend to ask not ‘do we need air cleaning’ rather they ask ‘which air cleaning provider will we use?’ and that forms to basis of expectations from clients and employees over there. In turn Zehnder transported that business model across the rest of Europe and we’re now present and established in all major markets as well as in the US.
In the UK market specifically, we’ve had great success in the Manufacturing sector where we’ve worked with all sorts of household name clients to protect their workforce and to help them make their production processes more cost efficient. Curiously the one sector that has underperformed compared to other European markets is the logistics industry and the feedback we have is clear – in a highly competitive market people view air cleaning as a luxury which is nice to have but is an extra cost.
That’s why we’ve been taking the message to logistics providers that actually, when you really begin to explore it, that’s not correct – some of our clients actually reduce their costs overall by targeting air cleaning in the areas where it can have the biggest positive impact. Our role is to understand where dust or fumes negatively impact your business, where it adds time and cost and then to put together a solution to fi x it for you. And because we have done this across many markets, many times, we’ve built a wealth of knowledge on how that’s possible.
Q Can you give me some examples?
A Absolutely, we worked with a major third-party provider who had to employ a 5 man hygiene team to keep their client happy about the state of the goods they were packing and shipping for them. We put together a solution, installed our units and as a result we reduced the airborne dust by 75% – that allowed the third-party provider to reduce their hygiene team from 5 to 1 while still maintaining the same standards.
The 4 workers were moved onto packing duties and their business benefitted from hiring less agency staff, meaning our solution not only paid for itself but made them money. There are lots of other similar examples I could share, but the principle is often the same – in line with the trend across the logistics sectors it’s about automating processes which if done well can save time money and help drive productivity.
Q Can you tell us about your recent innovations?
A Yes, we’re really excited about the next generation of air cleaners, the CleanAir Max range that we launched recently and it’s because it’s so closely linked to this topic of automation. We’re now able to install units which are true IIOT (industrial internet of things) meaning they use smart technology to drive themselves, to maximise air cleaning while minimising energy consumption. We have an array of sensors installed within the units to detect all sorts of things as a customer would want so it helps take us from air cleaning to really being able to offer insights into the day to day activities in a site. You see, when dust gets into the air, it doesn’t do it on its own, it is always because it’s created or disturbed by activity. We’ve been able to offer our customers some great insights into what actually takes place in their facilities and to help them identify inefficiencies that were otherwise being missed.
This next step we’ve just take the CleanAir Max has really put us into a new and exciting world as a service provider and possibilities are endless.
Q Are there any other trends you’re seeing?
A Through our international presence, we’re seeing more and more companies diving deeper into ESG, a commitment to sustainability is becoming something that is becoming a core requirement from our customers but also from their customers so we all need to be finding ways to make improvements step by step. That’s where we are very well placed as air cleaning in and of itself as a huge boost to sustainability – by cleaning your air you are reducing pollution and waste some of which can be hazardous. Not only that, you are protecting you workers physical and mental health and showing them that the organsation truly cares about their wellbeing.
Allied to that with the functionality of our new generation of technology, we can help our customers not only reduce their impact but also in data gathering which for many businesses we know is a real headache.
Q If readers are interesting in learning more, what should they do?
A I love to talk about clean air so any of your readers should feel to call me on 07909 533878 or email [email protected] or if they would like a consultation at one of their sites to see how we can help, our team will organise a visit from one of my colleagues locally on 0800 043 0100. ■
ZEHNDER GROUP UK LTD
Concept House, Watchmoor Point Camberley, Surrey, GU15 3AD
Tel: 0800 043 0100