No more hanging around
Highly paid lorry drivers are often compelled to wait for hours at loading bays while warehouse operatives manually load and unload. But safety and efficiency can be improved with automation, says Wouter Satijn.
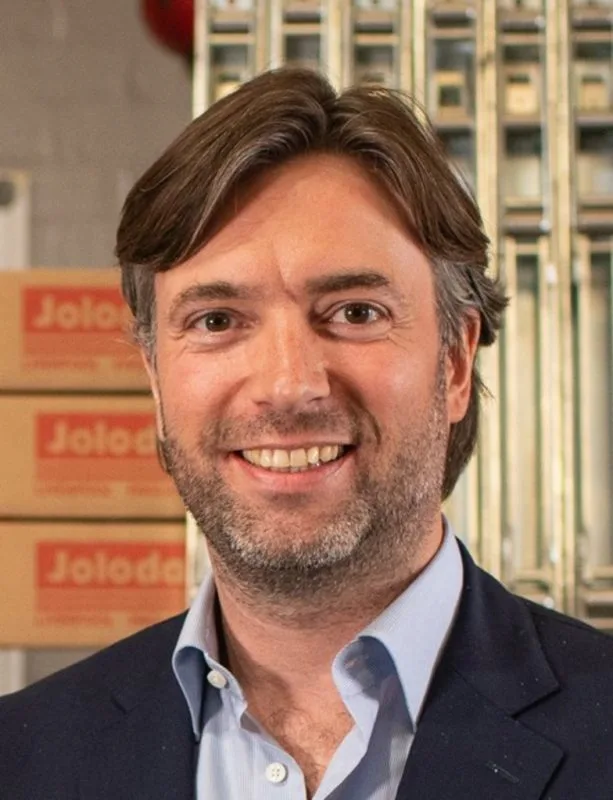
THE WORKING experience has to improve. In addition to the 35 and 45 minutes it takes on average to load or unload a trailer, drivers often have to wait significantly longer for their turn at the loading bay. Automated loading can eradicate driver delay and maximise drive time. It can minimise warehouse operatives’ manual activity and reliance on forklift trucks, radically improving safety. The process is faster and more efficient, allowing warehouse operatives to be relocated to safer, more enjoyable and potentially better-paid areas of the operation. With more certainty about delivery timelines, businesses can explore further optimisation, automation and collaboration to meet environmental goals.
Automating the loading process delivers a rapid ROI and future proofs the business against continuing staff shortages and rising environmental expectations.
Automated loading systems are faster and more efficient – achieving in two or three minutes what typically takes over 30 minutes manually. They also require far fewer people, including forklift and truck drivers, as well as warehouse staff. Automating this part of the logistics process minimises the risk of both accident and product damage, which makes it far safer for employees to unload heavy and dangerous loads – such as lithium-ion batteries and nuclear waste. Damage is also avoided because products are not left outside in the rain during the loading or unloading process, or impaired as they’re manoeuvred in and out of the trailer by stacker or forklift.
Plus, with an automated loading system, fewer forklift trucks are required, reducing costs, minimising the risk of accidents and cutting noise levels. Forklifts, despite their increasing shift to battery power, also have a significant carbon footprint. Cutting numbers improves a business’s environmental standing and frees up valuable space that is no longer required for storage or battery charging. In turn, businesses can increase output by reducing the storage space in the loading dock area. Staff can also be reallocated to other areas of the business – such as picking and packing – where the job is both better paid and more enjoyable, while also adding business value.
For lorry drivers, automated loading completely transforms the experience. Waiting is eradicated – with driver wait time reduced by 85%. For drivers, this improves the day-to-day experience. It ensures more time on the road and reduces the uncertainty and stress associated with meeting delivery deadlines within restricted hours.
Wouter Satijn, sales director, Joloda Hydraroll
For more information visit joloda.com