Understanding workplace safety regulations in warehouses
Warehouses are busy, high-risk environments.
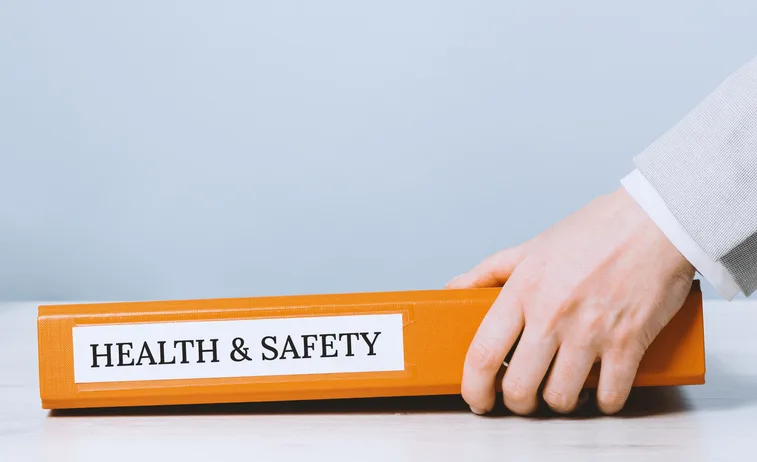
Why warehouse safety is critical
From heavy machinery to manual handling tasks, employees face numerous hazards. It’s critical for warehouse operators to understand and comply with the many workplace safety laws designed to protect workers. Read on for an overview of the key UK regulations that businesses need to be aware of, and the best practices to help them achieve a safer warehouse environment and reduce their potential liability.
Key UK legislation governing warehouse safety
To start, warehouse operators must familiarise themselves with two key laws that set out general responsibilities on employee safety:
The Health and Safety at Work Act 1974 places duties on employers to protect the health, safety, and welfare of their employees.
The Management of Health and Safety at Work Regulations 1999 require employers to carry out risk assessments. They must also put preventive measures in place to minimise workplace hazards.
In addition, the following regulations specifically address warehouse operations:
The Provision and Use of Work Equipment Regulations 1998 (PUWER) require that businesses properly inspect and maintain any equipment, such as machinery and tools, that is used to carry out work. The equipment must also be suitable for the task.
The Manual Handling Operations Regulations 1992 focus on reducing injuries from manual handling tasks such as lifting and carrying heavy loads.
Common hazards in warehouse settings
Warehouse work comes with numerous potential hazards, but there are a few that are particularly prevalent.
Forklift accidents: Approximately 1300 workers are hospitalised every year in the UK for forklift-related injuries, highlighting the need for warehouse operators to provide proper training and safety protocols around forklift use.
Slips, trips, and falls: To reduce these risks, business should follow practices such as ensuring that walkways are clear, cleaning up spills immediately, and installing anti-slip flooring.
Manual handling injuries: To reduce the risks associated with lifting and moving heavy items, provide mechanical aids, and train employees in ergonomic lifting techniques.
Implementing effective safety measures
There are measures that business can put in place to improve warehouse safety. For example, regular risk assessments will uncover potential dangers before they lead to accidents, and provide an opportunity to implement corrective action.
Also, all employees should be given training in how to operate equipment safely, identify hazards, and respond to emergencies.
Additionally, it’s crucial to provide Personal Protective Equipment (PPE) such as high-visibility clothing, safety boots, and helmets. This must be followed up by enforcing its use.
Reporting and managing workplace accidents
It’s imperative that any accidents are reported according to specified procedures.
Under the Reporting of Injuries, Diseases and Dangerous Occurrences Regulations (RIDDOR), it’s mandatory for employers to document serious incidents. This practice helps with investigations and can also spur employers to add preventive measures.
Legal implications of non-compliance
Failure to comply with warehouse safety regulations can lead to lawsuits and fines, or damage to reputation.
Additionally, non-compliance can lead to employees filing a claim for an accident at work. These claims can result in serious financial and operational repercussions for the company.
Warehouse safety leads to efficiency and productivity
Businesses shouldn’t think of warehouse safety as just another legal obligation, or a box to tick. By following regulations, implementing best practices, and fostering a culture of safety, businesses can protect employees while improving productivity, efficiency, and employee morale.