Home> | Automation | >Automated handling | >Error-free picking |
Home> | Automation | >Automated storage | >Error-free picking |
Home> | Automation | >Picking & sortation | >Error-free picking |
Error-free picking
20 June 2018
Fashion brand Marc Cain is benefiting from automation supplied by KNAPP.
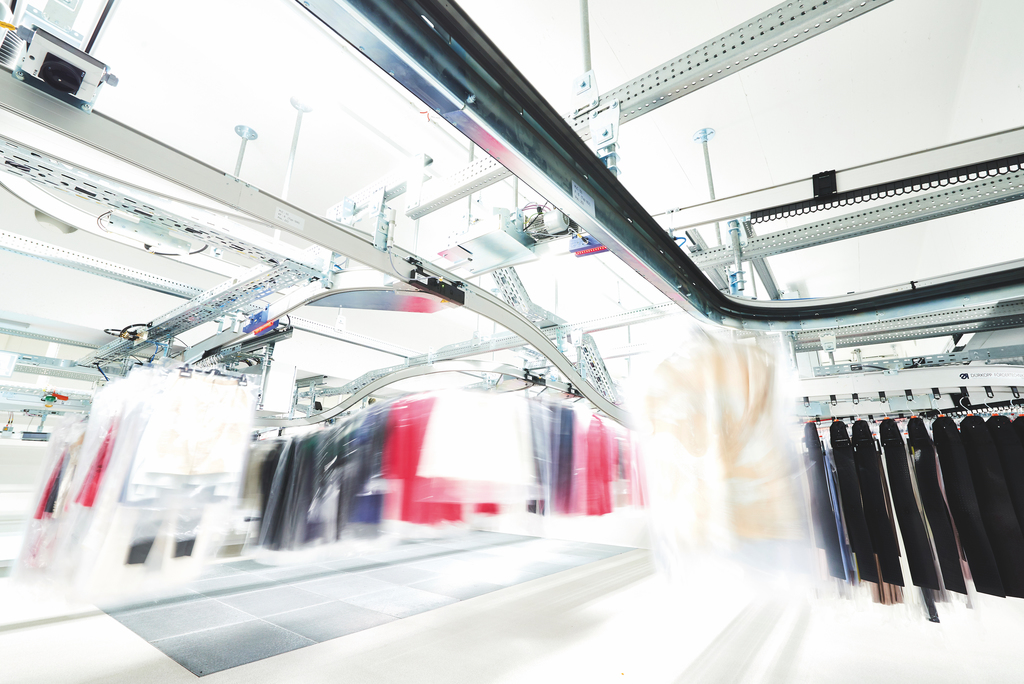
The international women’s fashion brand recently invested around 35m euros in its logistics capacity, including automated warehouse systems from KNAPP worth 12m euros.
Construction of the distribution centre centralised six facilities at the Bodelshausen site. “This was desperately needed,” explains logistics manager, Robert Boland, “as we had well and truly reached the limits of our capacities in the regional warehouses.” As a result order lead times for returns and new items were long.
Integrated solution
Measuring almost 100m in length by 74m in width and standing 18m tall, the building has a footprint of 7,100 sq m, with mezzanine floors providing a usable floor space of some 24,500m². Inside, a combination of KNAPP’s OSR Shuttle solution and the roll adapter technology of KNAPP subsidiary, Dürkopp Fördertechnik, allow Marc Cain’s complete range of flat-packed and hanging goods to be handled seamlessly. KNAPP also supplied its KiSoft WMS and KiSoft WCS software to control the integrated solution.
Textiles know-how
Over three million items of clothing pass through the warehouse each year and up to 35,000 articles are picked on a daily basis. On the decision to choose KNAPP as the logistics automation supplier, Boland says, “We were looking for someone who understood textiles who could offer us an all-in-one solution. With KNAPP, the whole package of technology, software and references just fitted.”
Error-free picking
Flat-packed items are supplied in foldable crates, developed especially for Marc Cain, which can be lidded, sealed and strapped. At goods-in, the delivered quantity of items is verified by weighing the containers, with checks carried out if the weight does not correspond with the expected quantity. The goods are then scanned and transported by conveyor to KNAPP’s OSR Shuttle system.
This automated store features over 84,000 storage locations for flat-packed goods and serves the ergonomically designed order picking stations, where all goods are supplied within optimal reach and view of warehouse staff. The Pick-it-Easy Shop workstations have been specifically designed to cater for the demands of the fashion and retail sectors. The system suggests a suitable size of carton into which the goods should be picked, while pick-to-light displays and touch screens ensure efficient and error-free order processing.
RFID coding
Expanding B2C
Marc Cain’s B2C sales have grown rapidly. During peak periods, up to 1,250 packages are shipped daily. Online orders containing luxury items are packed with particular care at special Sort & Pack stations, where the goods are wrapped in tissue paper and dispatched in premium-quality cartons with Marc Cain branding, together with an added gift.
- Grocery leader makes heavy automation investment
- First Fastbox installed by KNAPP
- Nice and Easy does it
- Open Shuttles display swarm intelligence
- Half a million storage locations
- KNAPP making complexity simple at IntraLogisteX
- Large-scale automated operation for 3PL
- Apprenticeship success
- Designed to minimise lifetime costs
- Future-oriented design