Home> | Automation | >Automated handling | >Highly bespoke conveying solution goes through the roof for client |
Home> | Industry Sector | >Food & drink | >Highly bespoke conveying solution goes through the roof for client |
Highly bespoke conveying solution goes through the roof for client
09 January 2019
Two production lines handling an iconic, alcoholic beverage in France had to reach a densely packed palletising area.
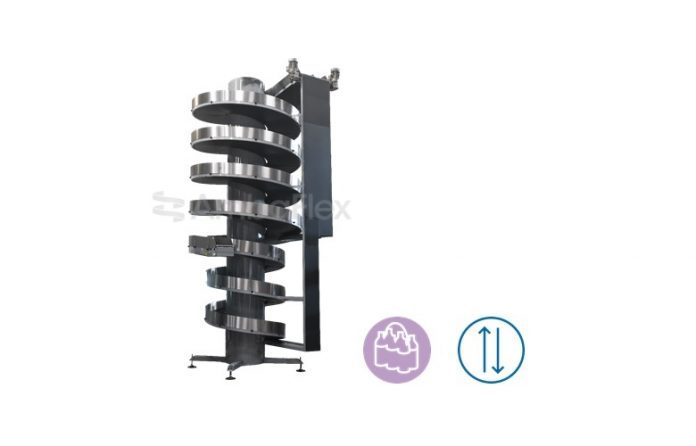
The problem with reaching this area was that they were 50 metres apart and in different sections of the building. And to make matters worse, there wasn’t enough room in the palletising area for a conventional approach with regular conveyors.
After looking at all the options, they decided that the most efficient way to get the filled carton boxes to their final destination was by going through the roof. After which the cartons had to travel through a tunnel for 50 meters and descend again, down into the palletising area.
Getting the two lines up to the roof was relatively easy and done by two standard AmbaFlex SV SpiralVeyors. The short journey through the tunnel on a regular conveyor wasn’t a big deal either. Getting both lines down again in the packed palletiser room was a different story. With so little room to work in, there was only enough space for one compact spiral, but both lines needed a separate outfeed and at different heights.
To solve this issue, AmbaFlex came up with a dual lane spiral called the SV x configuration with separate outfeeds at different heights. Essentially serving as two spirals but only taking the amount of floor space of one.
Instead of just offering a technical product AmbaFlex aims to work with the customers to look at the most efficient way to add value to a production line and propose a true solution.