Home> | Warehouse Storage | >Warehouse storage | >The case for live storage |
ARTICLE
The case for live storage
12 December 2012
Item storage will determine how well product flow can be maintained, says Edward Hutchison, managing director of BITO Storage Systems Order picking is the most labour-intensive and costly activity in most warehouses
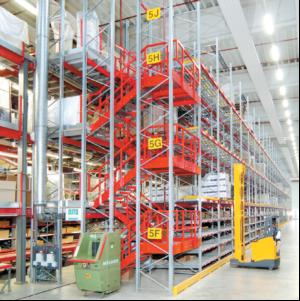
Item storage will determine how well
product flow can be maintained, says
Edward Hutchison, managing director of
BITO Storage Systems
Order picking is the most labour-intensive and costly activity in most warehouses - accounting for as much as 55% of the total warehouse operating cost. This alone is a good reason to choose a mode of storage that gives maximum efficiency; add the demands of optimum availability of goods, fast access and on-time delivery within the shortest possible lead time and it becomes imperative.
Space constraints are another factor. Lean practice may require consolidating all stock into a single site. Alternatively, it may require space for picking growing numbers of product lines and SKUs without acquiring a new building. Either way it means devising a way of holding the maximum number of products within the minimum footprint.
Yet this system must also be flexible enough to adapt to changing circumstances, as stock profiles are increasingly prone to change due to shorter product line life cycles and more fickle markets.Many companies will also experience big swings in picking activity during seasonal peaks.
Will conventional pallet rack-based storage systems support an order picking system that can meet all of these demands? Increasingly companies are finding that they can't and are instead opting for live storage.
For small item picks in particular, the trend is moving away from traditional static shelving and longspan racking, towards dynamic carton live storage. This is because carton live provides a dense storage system that allows faster picking and reduced manpower, as well as improved space saving and organisation.
Storage density comes from concentrating cartons into flow lanes.With carton live, goods are fed into the system at the rear to flow down roller tracks in an inclined lane to be presented at the front on the pick face. Once a carton at the pick face is empty it is simply taken away to allow a full carton sitting right behind it in the lane to flow down on the roller tracks and take its place, therefore ensuring products are constantly available at the pick face. Being a First in, First Out (FIFO) system, carton live storage enables easy control of time critical products ensuring stock is not sitting around longer than it should be.
Carton live storage system not only maximises the number of products that can be held on a given footprint, it also gives a compact pick face. This is because sufficient quantities of fast moving products can be lined up in the flow lanes rather than, with conventional racking systems, occupying locations on the pick face. A greater number of fast moving SKUs can, therefore, be located within a shorter distance, thus picking zones can be smaller to reduce picker travel times and increase productivity.
This means carton live is particularly suitable for applications with a wide range of SKUs and product lines.
For fast moving items in particular, conventional pallet rack based order picking, with its single, or even double deep, bays cannot provide enough locations at the pick face to hold sufficient stock without resorting to multiple replenishment runs from a bulk store. The alternative would be a very long pick face to accommodate sufficient numbers of locations for the fast mover. This of course means increasing travel distances for the picker. As with replenishment this incurs time and cost.
The live storage principle applies not just with cartons, of course, but with pallets also and solutions will often combine a mix of carton and pallet live. Pallets in a live system are ideal for holding large quantities of small items or extremely fast moving items. Picking straight from a pallet load not only saves time decanting these products into cartons, but also a single product line might need to occupy a whole level of flow lanes.
Where you have combined carton and pallet live systems, the pallet lanes - for faster moving goods - are located on the bottom level with the carton lanes above, creating a balanced work load in each pick zone.
The improvements in working efficiency made possible by a carton live storage system will more than compensate for higher initial investment. For example, by providing within a short distance a greater density of pick locations for products, a saving on floor space in the region of 15-20 per cent, when compared to conventional storage, is a reasonable assumption. Products can be located far more quickly in small pick zones than they could by traveling round conventional racking. Depending on the application, travel times for order pickers can be improved by up to 66 per cent. Furthermore, because the goods move unassisted into the picking position, order pickers can rely on a constant availability and are not left waiting for replenishment.
Order picking is the most labour-intensive and costly activity in most warehouses - accounting for as much as 55% of the total warehouse operating cost. This alone is a good reason to choose a mode of storage that gives maximum efficiency; add the demands of optimum availability of goods, fast access and on-time delivery within the shortest possible lead time and it becomes imperative.
Space constraints are another factor. Lean practice may require consolidating all stock into a single site. Alternatively, it may require space for picking growing numbers of product lines and SKUs without acquiring a new building. Either way it means devising a way of holding the maximum number of products within the minimum footprint.
Yet this system must also be flexible enough to adapt to changing circumstances, as stock profiles are increasingly prone to change due to shorter product line life cycles and more fickle markets.Many companies will also experience big swings in picking activity during seasonal peaks.
Will conventional pallet rack-based storage systems support an order picking system that can meet all of these demands? Increasingly companies are finding that they can't and are instead opting for live storage.
For small item picks in particular, the trend is moving away from traditional static shelving and longspan racking, towards dynamic carton live storage. This is because carton live provides a dense storage system that allows faster picking and reduced manpower, as well as improved space saving and organisation.
Storage density comes from concentrating cartons into flow lanes.With carton live, goods are fed into the system at the rear to flow down roller tracks in an inclined lane to be presented at the front on the pick face. Once a carton at the pick face is empty it is simply taken away to allow a full carton sitting right behind it in the lane to flow down on the roller tracks and take its place, therefore ensuring products are constantly available at the pick face. Being a First in, First Out (FIFO) system, carton live storage enables easy control of time critical products ensuring stock is not sitting around longer than it should be.
Carton live storage system not only maximises the number of products that can be held on a given footprint, it also gives a compact pick face. This is because sufficient quantities of fast moving products can be lined up in the flow lanes rather than, with conventional racking systems, occupying locations on the pick face. A greater number of fast moving SKUs can, therefore, be located within a shorter distance, thus picking zones can be smaller to reduce picker travel times and increase productivity.
This means carton live is particularly suitable for applications with a wide range of SKUs and product lines.
For fast moving items in particular, conventional pallet rack based order picking, with its single, or even double deep, bays cannot provide enough locations at the pick face to hold sufficient stock without resorting to multiple replenishment runs from a bulk store. The alternative would be a very long pick face to accommodate sufficient numbers of locations for the fast mover. This of course means increasing travel distances for the picker. As with replenishment this incurs time and cost.
The live storage principle applies not just with cartons, of course, but with pallets also and solutions will often combine a mix of carton and pallet live. Pallets in a live system are ideal for holding large quantities of small items or extremely fast moving items. Picking straight from a pallet load not only saves time decanting these products into cartons, but also a single product line might need to occupy a whole level of flow lanes.
Where you have combined carton and pallet live systems, the pallet lanes - for faster moving goods - are located on the bottom level with the carton lanes above, creating a balanced work load in each pick zone.
The improvements in working efficiency made possible by a carton live storage system will more than compensate for higher initial investment. For example, by providing within a short distance a greater density of pick locations for products, a saving on floor space in the region of 15-20 per cent, when compared to conventional storage, is a reasonable assumption. Products can be located far more quickly in small pick zones than they could by traveling round conventional racking. Depending on the application, travel times for order pickers can be improved by up to 66 per cent. Furthermore, because the goods move unassisted into the picking position, order pickers can rely on a constant availability and are not left waiting for replenishment.
MORE FROM THIS COMPANY
- BITO develops sprinkler shelves that let water through
- Shelving sorts out Regatta
- Storage solutions to tackle modern warehouse challenges
- How to achieve high density storage
- PROflow on show
- Retrofitting advantage for order picking
- Alternative option
- More than just a catalogue
- BITO plans new container sizes suited for eCommerce
- Fast track service
OTHER ARTICLES IN THIS SECTION