Home> | Lift trucks | >Counterbalance | >Productivity boost promised |
ARTICLE
Productivity boost promised
12 December 2012
The Automated Order Picking lift truck solution from Toyota is innovative and proven. It is a must-see for managers looking to slash waste from the picking process. Toyota has refined the concept of lift truck automatio
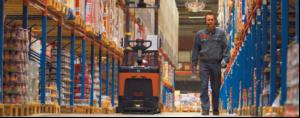
The Automated Order Picking lift truck solution from Toyota is innovative and proven.
It is a must-see for managers looking to slash waste from the picking process.
Toyota has refined the concept of lift truck automation with an order picking solution that promises significant productivity gains, as well as reduced numbers of accidents and damage in the warehouse.
The product allows pickers to focus on the pick while the truck automatically and independently moves to the correct location.
Toyota sees the product cutting down waste in the picking process, which is an increasingly significant issue given the rise in picks needed and in complexity of picks due to e-commerce. The manufacturer estimates that 40% of the cost in the warehouse comes from picking and of this figure 50% is caused by travel, with search accounting for 20%.
The Automated Order Picking (AOP) solution has been installed with some customers since 2008 and Toyota been working on the concept since then. It is now marketing the solution more broadly. The price premium for the automated lift trucks is not being released but Toyota insists that productivity gains more than balance out capital investment costs.
Andrew Elliott, executive vice president of marketing, Toyota Material Handling Europe says: "The rise of online shopping has created greater need for picking of individual orders, and this places great demands on the business in terms of storage, order picking and automation.
"AOP will cost more money to buy but customers need to take holistic view and look at total cost. The investment in trucks will be compensated for by savings in other areas." Toyota is already seeing interest in the solution from big retailers in the UK but Elliott sees a wide number of applications for the technology.
"It is interesting that the technology can be mixed with manual trucks. Previously it had to be a completely automated warehouse. This gives us a greater spectrum of possibilities with companies of different sizes in a variety of applications." The mixed use scenario is important as not all picks are suitable for automation, for example, if there are long distances between picks, other options may be more efficient.
Toyota is collaborating with Swedish firm Kollmorgen on the mapping and IT technology that is ported on to the truck. The technology can be integrated into a number of Toyota vehicles.
Making much better use of personnel was a key driver in the development of the product. Eliminating the wasted labour time traditionally involved in order picking - driving trucks to and from despatch areas and taking care of battery charging - is allowing increases in productivity of up to 40% in pilot installations, according to Toyota.
"When you think about it, the main contribution that the human makes in order picking is identifying and picking the right goods," explains Hans Larsson, who is head of the Logistic Solutions & Development team at TMHE. "Accompanying a truck over longer distances is a waste of human talent and we have technology that can easily take care of that part of the process." The concept is built on the type of guidance system launched by Toyota some ten years ago with the laser-guided BT Autopilot range. Laser-guided trucks avoid the upheaval and inflexibility of wire-guided installations, and safety is assured with sensors and careful speed management.
The integration of the guidance system with the customer's warehouse management system (WMS) is the latest breakthrough, with pick-by-voice delivering instructions to the human pickers to complete the process.
Essentially the concept is based on the human picker being instructed to go to a picking position to select certain goods, while a truck is already sent to the same point to transport the items picked. Ultimately the control system will calculate the most efficient route plan.
Larsson continues: "The pilot site, installed in 2008, is the Swedish retailer Coop, within the largest distribution centre in northern Europe. Here they are reporting productivity gains of 40%. Other sites around Europe are showing similar gains in productivity. This has dramatic implications for the industry with huge potential for cost reduction."
Toyota has refined the concept of lift truck automation with an order picking solution that promises significant productivity gains, as well as reduced numbers of accidents and damage in the warehouse.
The product allows pickers to focus on the pick while the truck automatically and independently moves to the correct location.
Toyota sees the product cutting down waste in the picking process, which is an increasingly significant issue given the rise in picks needed and in complexity of picks due to e-commerce. The manufacturer estimates that 40% of the cost in the warehouse comes from picking and of this figure 50% is caused by travel, with search accounting for 20%.
The Automated Order Picking (AOP) solution has been installed with some customers since 2008 and Toyota been working on the concept since then. It is now marketing the solution more broadly. The price premium for the automated lift trucks is not being released but Toyota insists that productivity gains more than balance out capital investment costs.
Andrew Elliott, executive vice president of marketing, Toyota Material Handling Europe says: "The rise of online shopping has created greater need for picking of individual orders, and this places great demands on the business in terms of storage, order picking and automation.
"AOP will cost more money to buy but customers need to take holistic view and look at total cost. The investment in trucks will be compensated for by savings in other areas." Toyota is already seeing interest in the solution from big retailers in the UK but Elliott sees a wide number of applications for the technology.
"It is interesting that the technology can be mixed with manual trucks. Previously it had to be a completely automated warehouse. This gives us a greater spectrum of possibilities with companies of different sizes in a variety of applications." The mixed use scenario is important as not all picks are suitable for automation, for example, if there are long distances between picks, other options may be more efficient.
Toyota is collaborating with Swedish firm Kollmorgen on the mapping and IT technology that is ported on to the truck. The technology can be integrated into a number of Toyota vehicles.
Making much better use of personnel was a key driver in the development of the product. Eliminating the wasted labour time traditionally involved in order picking - driving trucks to and from despatch areas and taking care of battery charging - is allowing increases in productivity of up to 40% in pilot installations, according to Toyota.
"When you think about it, the main contribution that the human makes in order picking is identifying and picking the right goods," explains Hans Larsson, who is head of the Logistic Solutions & Development team at TMHE. "Accompanying a truck over longer distances is a waste of human talent and we have technology that can easily take care of that part of the process." The concept is built on the type of guidance system launched by Toyota some ten years ago with the laser-guided BT Autopilot range. Laser-guided trucks avoid the upheaval and inflexibility of wire-guided installations, and safety is assured with sensors and careful speed management.
The integration of the guidance system with the customer's warehouse management system (WMS) is the latest breakthrough, with pick-by-voice delivering instructions to the human pickers to complete the process.
Essentially the concept is based on the human picker being instructed to go to a picking position to select certain goods, while a truck is already sent to the same point to transport the items picked. Ultimately the control system will calculate the most efficient route plan.
Larsson continues: "The pilot site, installed in 2008, is the Swedish retailer Coop, within the largest distribution centre in northern Europe. Here they are reporting productivity gains of 40%. Other sites around Europe are showing similar gains in productivity. This has dramatic implications for the industry with huge potential for cost reduction."
MORE FROM THIS COMPANY
- Toyota’s vision for the future of truck design
- Get hands-on with Toyota
- New picking system leads the way in automation
- Toyota to emphasise fleet management at IMHX
- Toyota Material Handling apprenticeship programme
- Pallet Truck Plus offers full support
- Keeping the focus on safety
- Stability, confidence and safety
- Toyota gets closer to its customers in the North West
- Taking the sustainable option
OTHER ARTICLES IN THIS SECTION