Home> | Automation | >Conveying components | >Huge automated retail revamp |
ARTICLE
Huge automated retail revamp
12 December 2012
Swisslog has implemented a sustainable logistics solution for major European retailer dm-drogerie markt, with CaddyPick a technical highlight With around 2,400 branches in 11 countries, dm-drogerie markt (dm) is one of
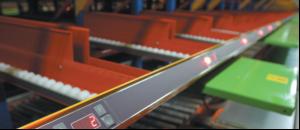
Swisslog has implemented a sustainable logistics solution for major European
retailer dm-drogerie markt, with CaddyPick a technical highlight
With around 2,400 branches in 11 countries, dm-drogerie markt (dm) is one of Europe's leading retailers. In fiscal year 2009/2010, the Group employed some 36,000 staff and generated sales exceeding MEUR 5,600. Swisslog's business relationship with the retailer dates back to 2003, when it was contracted to build a distribution centre in Germany to meet the demands arising from dm's double-digit sales growth.
As dm-drogerie markt continued to record growth on the same scale, it commissioned Swisslog as general contractor for a new distribution centre. The new facility, located near Cologne is now one of the largest and most modern facilities around, covering an area of approximately 50,000m2. The new distribution centre's logistics data is impressive with up to 1.1 million order lines processed and 4,500 pallets sent out every day. The facility has attracted a great deal of interest not only from a logistics point of view, but also due to the retailer's corporate culture, which attaches great importance to sustainability issues and workplace quality.
The distribution centre has been distinguished for both and is also a benchmark in financial terms, being dm's largest single investment and also Swisslog's most extensive project ever.
The material handling solution The distribution centre is split into two different operating areas, each with systems handling bulk boxed goods and small parts, with associated goods receiving operation and a high bay warehouse. The 33-metre tall high bay warehouse holds stock for the small parts operation and has 14,000 pallet locations available, which are managed by seven stacker cranes.
The part of the building reserved for boxed goods offers space for 24,000 pallets and is equipped with 13 stacker cranes. Swisslog's CaddyPick system is utilised in the picking zone which is one of the technical highlights. An electric monorail system with an overall length of around 5.5 kilometres connects approximately 5,000 picking stations. The operators pick directly to delivery pallets which are transported on specially constructed suspended units. The CaddyPick system combines elements of the man-togoods and zone-to-zone procedures and enables a highly efficient workflow with a high picking accuracy.
The goods receiving operation consists of nine sorting lines that differ by their degree of automation. At the start of every line, the cartons are first removed from the pallet either manually or automatically by industrial robots. Next, the tops of the cartons are removed either by a cutting machine or manually by an operator.
Depending on the size and article type, one or more opened cartons are placed on a plastic tray or deposited into a container.
These trays or containers are sent to the small parts picking zones via conveyors. There they are stored in a reserve zone with over 100,000 storage locations before being pushed into free picking locations. In the picking zones, picking is carried out using a zoneto- zone principle. The picking containers are transported by conveyor within the zone-to-zone system and are presented to the operators at one of 222 pick zones. Pick-by-light displays show the operators how many articles from which location they should place in the picking container. The order container is guided automatically through the aisles until it is completely filled. During peak days, dm can pick over one million order lines in the small parts zone using this approach.
The full picking container is conveyed automatically to a buffer module underneath the picking aisles where it remains until all of the containers, which make up a pallet, arrive. The picking containers which sequentially leave the buffer, are automatically stacked in four towers, and are then placed on a Euro pallet. The load is secured by straps and conveyed to a goods dispatch station.
From there the pallets are loaded by forklift truck onto a waiting swap-body transporter.
The software solution The flow of materials throughout the entire logistics centre is controlled by Swisslog's AutomationManager. This manages all warehousing, transport and auxiliary equipment and also interfaces with dm's warehouse management software and ERP system. In addition, Swisslog also implemented the SPOC (Single Point of Control) visualisation system. This supervisory tool provides dm operatives with a real-time graphical overview of the current status of all conveyor systems, stacker cranes and other equipment. The visualisation considerably simplifies troubleshooting technical faults and thus contributes to the high availability of the entire facility.
An investment for the future For dm, the new logistics centre is not only a success from economic and technical perspectives; it is also a success environmentally. The ecological sustainability that is firmly anchored in dm's business culture was implemented in the project.
Buildings are heated with CO2-efficient wood chips, while energy-efficient motors in material handling, solar panels on the roof, optimal utilisation of vehicles and the bundling of transports guarantee savings of more than 5,000 tons of CO2 a year.
With around 2,400 branches in 11 countries, dm-drogerie markt (dm) is one of Europe's leading retailers. In fiscal year 2009/2010, the Group employed some 36,000 staff and generated sales exceeding MEUR 5,600. Swisslog's business relationship with the retailer dates back to 2003, when it was contracted to build a distribution centre in Germany to meet the demands arising from dm's double-digit sales growth.
As dm-drogerie markt continued to record growth on the same scale, it commissioned Swisslog as general contractor for a new distribution centre. The new facility, located near Cologne is now one of the largest and most modern facilities around, covering an area of approximately 50,000m2. The new distribution centre's logistics data is impressive with up to 1.1 million order lines processed and 4,500 pallets sent out every day. The facility has attracted a great deal of interest not only from a logistics point of view, but also due to the retailer's corporate culture, which attaches great importance to sustainability issues and workplace quality.
The distribution centre has been distinguished for both and is also a benchmark in financial terms, being dm's largest single investment and also Swisslog's most extensive project ever.
The material handling solution The distribution centre is split into two different operating areas, each with systems handling bulk boxed goods and small parts, with associated goods receiving operation and a high bay warehouse. The 33-metre tall high bay warehouse holds stock for the small parts operation and has 14,000 pallet locations available, which are managed by seven stacker cranes.
The part of the building reserved for boxed goods offers space for 24,000 pallets and is equipped with 13 stacker cranes. Swisslog's CaddyPick system is utilised in the picking zone which is one of the technical highlights. An electric monorail system with an overall length of around 5.5 kilometres connects approximately 5,000 picking stations. The operators pick directly to delivery pallets which are transported on specially constructed suspended units. The CaddyPick system combines elements of the man-togoods and zone-to-zone procedures and enables a highly efficient workflow with a high picking accuracy.
The goods receiving operation consists of nine sorting lines that differ by their degree of automation. At the start of every line, the cartons are first removed from the pallet either manually or automatically by industrial robots. Next, the tops of the cartons are removed either by a cutting machine or manually by an operator.
Depending on the size and article type, one or more opened cartons are placed on a plastic tray or deposited into a container.
These trays or containers are sent to the small parts picking zones via conveyors. There they are stored in a reserve zone with over 100,000 storage locations before being pushed into free picking locations. In the picking zones, picking is carried out using a zoneto- zone principle. The picking containers are transported by conveyor within the zone-to-zone system and are presented to the operators at one of 222 pick zones. Pick-by-light displays show the operators how many articles from which location they should place in the picking container. The order container is guided automatically through the aisles until it is completely filled. During peak days, dm can pick over one million order lines in the small parts zone using this approach.
The full picking container is conveyed automatically to a buffer module underneath the picking aisles where it remains until all of the containers, which make up a pallet, arrive. The picking containers which sequentially leave the buffer, are automatically stacked in four towers, and are then placed on a Euro pallet. The load is secured by straps and conveyed to a goods dispatch station.
From there the pallets are loaded by forklift truck onto a waiting swap-body transporter.
The software solution The flow of materials throughout the entire logistics centre is controlled by Swisslog's AutomationManager. This manages all warehousing, transport and auxiliary equipment and also interfaces with dm's warehouse management software and ERP system. In addition, Swisslog also implemented the SPOC (Single Point of Control) visualisation system. This supervisory tool provides dm operatives with a real-time graphical overview of the current status of all conveyor systems, stacker cranes and other equipment. The visualisation considerably simplifies troubleshooting technical faults and thus contributes to the high availability of the entire facility.
An investment for the future For dm, the new logistics centre is not only a success from economic and technical perspectives; it is also a success environmentally. The ecological sustainability that is firmly anchored in dm's business culture was implemented in the project.
Buildings are heated with CO2-efficient wood chips, while energy-efficient motors in material handling, solar panels on the roof, optimal utilisation of vehicles and the bundling of transports guarantee savings of more than 5,000 tons of CO2 a year.
MORE FROM THIS COMPANY
- Limiting manual lifting
- Chilled out warehousing
- Real world Santa’s little helpers
- Automated high-bay for deep-freeze warehouse
- How automation software transforms food and beverage warehouses
- Swisslog and KUKA unveil new HRI Technology
- Sweet commission
- Light goods conveyor unveiled
- Swisslog to deliver a new automation system for Publix Super Markets, Inc.
- SmartCarrier a hit with Swisslog customers
OTHER ARTICLES IN THIS SECTION