ARTICLE
STAN ROBINSON REDUCES PICKING TIME BY 25% USING WAREHOUSE MANAGEMENT SYSTEM FROM SOLARSOFT
12 December 2012
Logistics provider saves two hours per user every day using Solarsoft to increase warehouse efficiency and picking accuracy
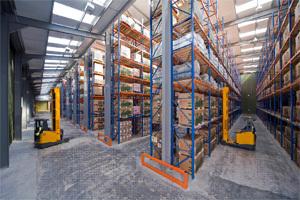
Logistics provider saves two hours per user every day using Solarsoft to increase warehouse efficiency and picking accuracy
Logistics solutions provider, Stan Robinson, today announces it has implemented a new Warehouse Management System (WMS) from Solarsoft to automate its business processes and reduce the amount of time it takes to pick items by 25% - the equivalent of two hours per user each day.
Before implementing the Solarsoft solution, Stan Robinson was operating almost entirely via paper-based systems, Excel spreadsheets and manual processes. However, when one of the company's largest customers advised that it was moving onto the Solarsoft Warehouse Management System, Stan Robinson decided it too would switch to a more efficient, automated solution in order to integrate with the customer and improve its business processes.
Richard Baxter, IT Manager at Stan Robinson explains, “The decision to partner with Solarsoft came when a key customer of ours implemented Solarsoft's WMS and wanted to create a real-time stock movement link with our business. However, as the majority of our processes were paper-based, it made business sense for us to implement the new Solarsoft system in order to integrate with our customer and improve our operations at the same time.â€
Since the Solarsoft system went live in November 2010, Stan Robinson has benefited from increased productivity, better efficiency and more accurate traceability of stock and pallets. Baxter continues, “The new system allows us to track everything in real time which is a huge benefit to us as a business, but is also a key advantage for our customers. Using the system we are able to see exactly what has been picked and when, and this information is fed straight back to the customer in real-time. This means that they too can see when that load has been picked, when it's in transit, when it has been delivered and also when we haven't got enough stock and so require a delivery. This makes our processes far slicker and is saving us on average around two hours per user per day.â€
Baxter adds, “Using Solarsoft we are able to track pallets a lot more easily and can quickly look back into the history of the load or individual pallet to see where it was last located should anything go missing or get damaged. Before Solarsoft, we had to do manual stock takes, which were time consuming and very laborious. Also, if the stock wasn't available when the picker came to collect it, we had no way of knowing when or where it had gone missing. Everything was dependent on people inputting the correct information, and if there was just one wrong character entered then we would have stock discrepancies to resolve too. But with the automated system this no longer happens, which has dramatically increased our accuracies and stock visibility throughout the business.â€
Baxter concludes, “Having experienced such great results with the Solarsoft system, we are now looking to integrate additional functionality, such as Solarsoft Dashboards, which will give us greater analytical capabilities and allow us to share web-based reports with our customers. We're also looking to migrate some of our other large customers onto Solarsoft's Warehouse Management system as this will help to improve our efficiencies even further.â€
Logistics solutions provider, Stan Robinson, today announces it has implemented a new Warehouse Management System (WMS) from Solarsoft to automate its business processes and reduce the amount of time it takes to pick items by 25% - the equivalent of two hours per user each day.
Before implementing the Solarsoft solution, Stan Robinson was operating almost entirely via paper-based systems, Excel spreadsheets and manual processes. However, when one of the company's largest customers advised that it was moving onto the Solarsoft Warehouse Management System, Stan Robinson decided it too would switch to a more efficient, automated solution in order to integrate with the customer and improve its business processes.
Richard Baxter, IT Manager at Stan Robinson explains, “The decision to partner with Solarsoft came when a key customer of ours implemented Solarsoft's WMS and wanted to create a real-time stock movement link with our business. However, as the majority of our processes were paper-based, it made business sense for us to implement the new Solarsoft system in order to integrate with our customer and improve our operations at the same time.â€
Since the Solarsoft system went live in November 2010, Stan Robinson has benefited from increased productivity, better efficiency and more accurate traceability of stock and pallets. Baxter continues, “The new system allows us to track everything in real time which is a huge benefit to us as a business, but is also a key advantage for our customers. Using the system we are able to see exactly what has been picked and when, and this information is fed straight back to the customer in real-time. This means that they too can see when that load has been picked, when it's in transit, when it has been delivered and also when we haven't got enough stock and so require a delivery. This makes our processes far slicker and is saving us on average around two hours per user per day.â€
Baxter adds, “Using Solarsoft we are able to track pallets a lot more easily and can quickly look back into the history of the load or individual pallet to see where it was last located should anything go missing or get damaged. Before Solarsoft, we had to do manual stock takes, which were time consuming and very laborious. Also, if the stock wasn't available when the picker came to collect it, we had no way of knowing when or where it had gone missing. Everything was dependent on people inputting the correct information, and if there was just one wrong character entered then we would have stock discrepancies to resolve too. But with the automated system this no longer happens, which has dramatically increased our accuracies and stock visibility throughout the business.â€
Baxter concludes, “Having experienced such great results with the Solarsoft system, we are now looking to integrate additional functionality, such as Solarsoft Dashboards, which will give us greater analytical capabilities and allow us to share web-based reports with our customers. We're also looking to migrate some of our other large customers onto Solarsoft's Warehouse Management system as this will help to improve our efficiencies even further.â€
MORE FROM THIS COMPANY
RELATED ARTICLES
- No related articles listed
OTHER ARTICLES IN THIS SECTION