Home> | Warehouse IT | >Hardware | >A new dimension for driverless transportation |
ARTICLE
A new dimension for driverless transportation
12 December 2012
Ceiling-based laser scanning is the best lift truck option in terms of navigation and cost savings, argues Mark Weymouth, md of Leuze Electronic UK Driverless transportation systems (DTS) are becoming increasing popula
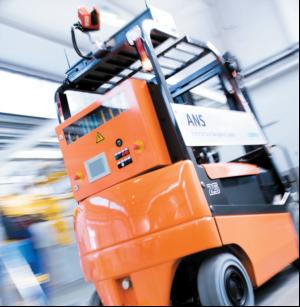
Ceiling-based laser scanning is the best lift truck option in terms of navigation and
cost savings, argues Mark Weymouth, md of Leuze Electronic UK
Driverless transportation systems (DTS) are becoming increasing popular for material handling in a wide range of industries because of the cost savings they offer.
Navigation commonly relies on optical scanning, usually horizontally, using reflector marks mounted on the building's structure or adjacent machines and structures. Siemens, however, is using Leuze Electronic's ROD 4 laser scanner for guidance using 3D laser scanning from the hall's ceiling, adding a new dimension: both navigationally and economically.
The cost reductions offered by driverless transportation systems come primarily from automatic operation removing the need for human operators. However the costs associated with the planning of these systems are relatively high. Usually, depending on the navigation system that is used, structural changes are necessary in the surrounding environment. These can include induction loops or magnets in the floor, or reflectors for laser scanners that normally scan over an area two dimensionally.
The flexibility of the system to allow later changes to routings or tasks is largely influenced by the technology used. Therefore production-related changes or structural changes, such as changes in racking, or the location of adjacent machines can lead to unforeseen disturbances in the transportation system, which can only be rectified with modifications.
Siemens' Autonomous Navigation System (ANS), takes driverless corridor supply vehicles to new dimensions. Both the spatial plane used for navigation, namely the hall ceiling, as well as to the cost effectiveness, achieved through lower installation costs, because no navigation aids need be installed on the floor, walls or system parts. ANS provides flexibility for future route changes in production environments.
The navigation system developed by Siemens is based on laser distance measurement technology from Leuze Electronic. For years, area scanning distance sensors have been developed and produced here that supply 2D depth information with a detection angle of 190°. They facilitate the detection of width, position and orientation of disruptive objects, for example during overshoot detection in high-bay warehouses over distances of up to 50 metres. Furthermore, such devices are typically used for 3D contour measurements, gripper positioning, access controls or collision detection, as well as for the positioning of travelling transport systems.
The fast, pulse propagation time technology of the ROD 4 enables the detection of 3D profiles that can be generated by means of swivelling or a linear feed motion of the measurement object or of the laser scanner relative to one another. For the navigation of driverless transportation systems, the laser scanner is mounted on a swivel motor on the top of the vehicle. This is used to capture a spatial representation of the surrounding environment, in this case, the hall ceiling, which then serves as the basis for free navigation.
The measurement principle used here is the pulse propagation time technique, which emits individual light pulses in short intervals. The time difference between the transmission and reception of a light pulse can be used to calculate the distance to an object that reflected the light. The evaluation occurs nearly independent of the shape, colour and structure of the scanned object. The system benefits from the ROD 4's high immunity to interference against environmental influences. The captured data is directed via a high-speed interface to the primary computer for the position calculation.
"The new 3D laser navigation system can be installed on a wide range of different types of indoor vehicles, from lift trucks to industrial trucks," explains engineer Walter Beichl, the project manager responsible for ANS at Siemens. "We are able to attain a navigation quality that is sufficient for most logistics requirements," Beichl adds. The precise values for positioning and travel accuracy are, however, always dependent on the surroundings and on the used vehicles.With forklifts, for example, a positioning accuracy of ±30 millimetres can be achieved, for industrial trucks, an accuracy of ±5 millimetres.
Compared to conventional DTS installations, the installation effort associated with the Autonomous Navigation System with the ROD 4 laser scanner is much lower. Travel routes are taught by means of a so-called teach-in concept, i.e. a manual teach-in journey. In this way, route changes can be integrated at short notice and in just a few minutes.
Almost as a by product of the navigation system, ANS performs obstacle detection.While this is not a secure obstacle detection system in the sense of personnel protection, static obstacles are detected and a braking operation is initiated.
Driverless transportation systems (DTS) are becoming increasing popular for material handling in a wide range of industries because of the cost savings they offer.
Navigation commonly relies on optical scanning, usually horizontally, using reflector marks mounted on the building's structure or adjacent machines and structures. Siemens, however, is using Leuze Electronic's ROD 4 laser scanner for guidance using 3D laser scanning from the hall's ceiling, adding a new dimension: both navigationally and economically.
The cost reductions offered by driverless transportation systems come primarily from automatic operation removing the need for human operators. However the costs associated with the planning of these systems are relatively high. Usually, depending on the navigation system that is used, structural changes are necessary in the surrounding environment. These can include induction loops or magnets in the floor, or reflectors for laser scanners that normally scan over an area two dimensionally.
The flexibility of the system to allow later changes to routings or tasks is largely influenced by the technology used. Therefore production-related changes or structural changes, such as changes in racking, or the location of adjacent machines can lead to unforeseen disturbances in the transportation system, which can only be rectified with modifications.
Siemens' Autonomous Navigation System (ANS), takes driverless corridor supply vehicles to new dimensions. Both the spatial plane used for navigation, namely the hall ceiling, as well as to the cost effectiveness, achieved through lower installation costs, because no navigation aids need be installed on the floor, walls or system parts. ANS provides flexibility for future route changes in production environments.
The navigation system developed by Siemens is based on laser distance measurement technology from Leuze Electronic. For years, area scanning distance sensors have been developed and produced here that supply 2D depth information with a detection angle of 190°. They facilitate the detection of width, position and orientation of disruptive objects, for example during overshoot detection in high-bay warehouses over distances of up to 50 metres. Furthermore, such devices are typically used for 3D contour measurements, gripper positioning, access controls or collision detection, as well as for the positioning of travelling transport systems.
The fast, pulse propagation time technology of the ROD 4 enables the detection of 3D profiles that can be generated by means of swivelling or a linear feed motion of the measurement object or of the laser scanner relative to one another. For the navigation of driverless transportation systems, the laser scanner is mounted on a swivel motor on the top of the vehicle. This is used to capture a spatial representation of the surrounding environment, in this case, the hall ceiling, which then serves as the basis for free navigation.
The measurement principle used here is the pulse propagation time technique, which emits individual light pulses in short intervals. The time difference between the transmission and reception of a light pulse can be used to calculate the distance to an object that reflected the light. The evaluation occurs nearly independent of the shape, colour and structure of the scanned object. The system benefits from the ROD 4's high immunity to interference against environmental influences. The captured data is directed via a high-speed interface to the primary computer for the position calculation.
"The new 3D laser navigation system can be installed on a wide range of different types of indoor vehicles, from lift trucks to industrial trucks," explains engineer Walter Beichl, the project manager responsible for ANS at Siemens. "We are able to attain a navigation quality that is sufficient for most logistics requirements," Beichl adds. The precise values for positioning and travel accuracy are, however, always dependent on the surroundings and on the used vehicles.With forklifts, for example, a positioning accuracy of ±30 millimetres can be achieved, for industrial trucks, an accuracy of ±5 millimetres.
Compared to conventional DTS installations, the installation effort associated with the Autonomous Navigation System with the ROD 4 laser scanner is much lower. Travel routes are taught by means of a so-called teach-in concept, i.e. a manual teach-in journey. In this way, route changes can be integrated at short notice and in just a few minutes.
Almost as a by product of the navigation system, ANS performs obstacle detection.While this is not a secure obstacle detection system in the sense of personnel protection, static obstacles are detected and a braking operation is initiated.
MORE FROM THIS COMPANY
- Leuze introduces LiDAR laser scanners
- Stay flexible safely
- Coded magnetic safety
- Free machine safety training in Croydon
- World-first for volume measurement
- Sensors key for automated high-bay warehouse
- Easier identification of containers and trays
- Leuze training workshop reaches Cheshire
- Free workshops on machine safety
- 2D-code readers get automation rolling
OTHER ARTICLES IN THIS SECTION