Home> | Automation | >Automated handling | >AGVs right for FMCG job |
ARTICLE
AGVs right for FMCG job
12 December 2012
Palletised raw materials and packaging tackled by AGVs from E&K Automation at UK manufacturer of fast moving consumer goods An analysis carried out by specialist manufacturer E&K Automation compared forklift and convey
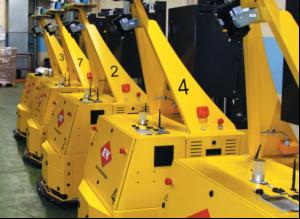
Palletised raw materials and packaging tackled by AGVs from E&K Automation at UK
manufacturer of fast moving consumer goods
An analysis carried out by specialist manufacturer E&K Automation compared forklift and conveyor based AGV concepts and mixed fleets. It was concluded that for a robust, reliable, flexible and resilient transportation system that can automatically handle both 1,200 x 1,000 mm Chep pallets and 1,200 x 800 mm Euro pallets at floor level and at various conveyor heights, the use of two E&K Compact CBI-800 counterbalance fork lift AGVs was optimal.
Each of the two AGV systems deployed used seven laser-guided vehicles of compact counterbalance design. Both AGV systems are independent of each other, although any vehicle can be deployed to work on either system for maximum resilience and flexibility.
This truck format allows pallet transfer positions to be passive, leaving floors clear and free from powered conveyors. It also avoids frames that would otherwise be needed to support a pallet stacker AGV format and wide aisles that would be needed with a straddle stacker AGV.
The counterbalance design also means that palletiser conveyor interfaces do not need to be modified to accept the narrow or wide load-wheel-arms that come with pallet stacker or straddle stacker AGVs.
Operation In essence, both AGV systems at the FMCG factory are designed to take palletised raw materials and packaging from a conveyor system in front of the warehouse to around 85 passive floor positions in the production areas. Surplus material and finished product from central palletiser conveyors are returned into storage, while waste is taken to a compactor. Positioning accuracy of the vehicles relative to each pick or drop location is ± 10mm.
There are three levels of control. In normal mode, vehicles operate automatically under central AGV control. In semiautomatic operation, they can be given instructions through onboard or remote terminals. If operated by hand, the AGV is driven and steered manually via its joystick control, with load handling effected by push button.
Vehicle navigation is by E&K's NAV830 laser triangulation system, which allows even the most complex AGV route including load pick and drop positions to be simply created on a CAD workstation and modified afterwards if necessary. Laser navigation reflectors are fixed to elevated positions on walls, columns or racking. Simulation tools help to optimise the routes, select the optimum number of vehicles and check for conformity with European standards. EK-REPORT provides user-friendly presentations for analysing operating and performance data.
Safety Although the factory and warehouse aisles of the manufacturer are not defined as hazardous, there are safety issues.While the low risk of explosion did not warrant fitting on-board gas detection and shutdown equipment to each of the AGVs, they are all interlocked with factory-wide fire and gas alarm systems and interact with a number of automatic doors.
It was also considered expedient to incorporate features on the vehicles to lessen the chance of product damage that could result in gas being leaked into the warehouse or factory aisles, as well as other measures to guard against ignition of any leaked gas that may be present.
E&K Automation fitted AC motors to power the drive, steer and lift on the battery powered vehicles, avoiding DC motors with their potential risk of sparks from the brushes. To maximise safety during travel, three laser scanners are employed, one at the front, one at the rear and another at high level to detect obstacles on the circuit. Electrically conductive tyres are employed to aid the dissipation of static electricity.
To ensure the AGV knows the precise position of its forks when a pallet is transferred or transported, two rotary encoders are fitted on the lift mast, rather than the normal one. Additionally, each fork tip includes a photoelectric sensor and there's a further sensor on the forks carriage to detect that the pallet is fully on board the AGV.
Three battery charging bays have been provided in each AGV system to automatically top up vehicle power. In some AGV environments, charging contacts are set into the floor but in this installation, they are mounted on the wall. This approach avoids having the battery contacts close to any leaked gas that might collect at floor level and also removes the need for disruptive building work.
In addition to the obstacle-detecting laser scanners at front and rear, pressure-sensitive strips stop the vehicle immediately an obstruction in the AGV's path is touched.Multi-colour status lamps, amber turn-indicator lamps, two types of audible warning device and four emergency stop buttons are standard equipment.
About 70 pallets per hour are transported by each system, 24x7, and pallets weigh up to 1.25 tonnes. The AGVs drive at speeds of up to 1.5 m/s, travel up and down ramps and cross a roadway, so safety is paramount.
Summing up the benefits of the installation, Peter Holdcroft, managing director of E&K in Bramley, Hampshire pointed to the importance of automation in allowing Western economies to compete with low-wage countries.
He added: "The flexibility of our latest AGV systems makes them future-proof, enabling extensive modification, upgrading and extension of capacity as circumstances dictate."
An analysis carried out by specialist manufacturer E&K Automation compared forklift and conveyor based AGV concepts and mixed fleets. It was concluded that for a robust, reliable, flexible and resilient transportation system that can automatically handle both 1,200 x 1,000 mm Chep pallets and 1,200 x 800 mm Euro pallets at floor level and at various conveyor heights, the use of two E&K Compact CBI-800 counterbalance fork lift AGVs was optimal.
Each of the two AGV systems deployed used seven laser-guided vehicles of compact counterbalance design. Both AGV systems are independent of each other, although any vehicle can be deployed to work on either system for maximum resilience and flexibility.
This truck format allows pallet transfer positions to be passive, leaving floors clear and free from powered conveyors. It also avoids frames that would otherwise be needed to support a pallet stacker AGV format and wide aisles that would be needed with a straddle stacker AGV.
The counterbalance design also means that palletiser conveyor interfaces do not need to be modified to accept the narrow or wide load-wheel-arms that come with pallet stacker or straddle stacker AGVs.
Operation In essence, both AGV systems at the FMCG factory are designed to take palletised raw materials and packaging from a conveyor system in front of the warehouse to around 85 passive floor positions in the production areas. Surplus material and finished product from central palletiser conveyors are returned into storage, while waste is taken to a compactor. Positioning accuracy of the vehicles relative to each pick or drop location is ± 10mm.
There are three levels of control. In normal mode, vehicles operate automatically under central AGV control. In semiautomatic operation, they can be given instructions through onboard or remote terminals. If operated by hand, the AGV is driven and steered manually via its joystick control, with load handling effected by push button.
Vehicle navigation is by E&K's NAV830 laser triangulation system, which allows even the most complex AGV route including load pick and drop positions to be simply created on a CAD workstation and modified afterwards if necessary. Laser navigation reflectors are fixed to elevated positions on walls, columns or racking. Simulation tools help to optimise the routes, select the optimum number of vehicles and check for conformity with European standards. EK-REPORT provides user-friendly presentations for analysing operating and performance data.
Safety Although the factory and warehouse aisles of the manufacturer are not defined as hazardous, there are safety issues.While the low risk of explosion did not warrant fitting on-board gas detection and shutdown equipment to each of the AGVs, they are all interlocked with factory-wide fire and gas alarm systems and interact with a number of automatic doors.
It was also considered expedient to incorporate features on the vehicles to lessen the chance of product damage that could result in gas being leaked into the warehouse or factory aisles, as well as other measures to guard against ignition of any leaked gas that may be present.
E&K Automation fitted AC motors to power the drive, steer and lift on the battery powered vehicles, avoiding DC motors with their potential risk of sparks from the brushes. To maximise safety during travel, three laser scanners are employed, one at the front, one at the rear and another at high level to detect obstacles on the circuit. Electrically conductive tyres are employed to aid the dissipation of static electricity.
To ensure the AGV knows the precise position of its forks when a pallet is transferred or transported, two rotary encoders are fitted on the lift mast, rather than the normal one. Additionally, each fork tip includes a photoelectric sensor and there's a further sensor on the forks carriage to detect that the pallet is fully on board the AGV.
Three battery charging bays have been provided in each AGV system to automatically top up vehicle power. In some AGV environments, charging contacts are set into the floor but in this installation, they are mounted on the wall. This approach avoids having the battery contacts close to any leaked gas that might collect at floor level and also removes the need for disruptive building work.
In addition to the obstacle-detecting laser scanners at front and rear, pressure-sensitive strips stop the vehicle immediately an obstruction in the AGV's path is touched.Multi-colour status lamps, amber turn-indicator lamps, two types of audible warning device and four emergency stop buttons are standard equipment.
About 70 pallets per hour are transported by each system, 24x7, and pallets weigh up to 1.25 tonnes. The AGVs drive at speeds of up to 1.5 m/s, travel up and down ramps and cross a roadway, so safety is paramount.
Summing up the benefits of the installation, Peter Holdcroft, managing director of E&K in Bramley, Hampshire pointed to the importance of automation in allowing Western economies to compete with low-wage countries.
He added: "The flexibility of our latest AGV systems makes them future-proof, enabling extensive modification, upgrading and extension of capacity as circumstances dictate."
MORE FROM THIS COMPANY
OTHER ARTICLES IN THIS SECTION