Home> | Automation | >Conveying components | >Optimal flows |
ARTICLE
Optimal flows
12 December 2012
Automated solution from Swisslog for Swedish builder's merchant to store more product in less space, with fewer people needed Dahl Sverige AB (owned by Saint-Gobain) is Sweden's leading trading company for heating and
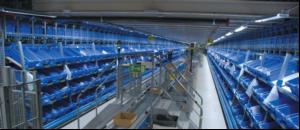
Automated solution from Swisslog for Swedish builder's merchant to store more
product in less space, with fewer people needed
Dahl Sverige AB (owned by Saint-Gobain) is Sweden's leading trading company for heating and sanitation services and industrial / property supplies. Having increased its number of products significantly and achieved escalating growth, Dahl started to outgrow its existing materials handling system and experienced queues forming at both its picking and filling storage areas.
Dahl's business ethic ensures that they constantly improve and streamline their operations and look for new solutions as a natural part of their daily work. Dahl acknowledged the importance of increasing their handling and storage capacity and provided clarification of their exact requirements: A solution which allowed more picking positions, a higher capacity and lower line costs.
This in turn led to them appointing Swisslog to supply an automated facility for customer order picking. Dahl's manual pallet warehouse was torn down and the new facility built in its place, without disrupting production.
The flow of goods at the new facility starts at the inbound goods arrivals area where products are repacked into plastic boxes before being weighed and measured for onward transportation to storage or to the picking area in the miniload facility. Picking takes place either directly into the cardboard delivery boxes or into plastic boxes. Cardboard boxes are erected automatically and are supplied to the picking zones via an integrated conveyor system. Customer order picking of smaller volumes takes place into plastic boxes, while larger order volumes are picked into cardboard boxes with the help of ergonomic picking stations in one of the twelve picking aisles, served by fast miniload cranes.
Picking takes place on two levels in the warehouse; on both the floor level and the mezzanine level. The majority of high frequency products are located in fixed pick positions.Midfrequency products are exposed in the picking station's aisles and once the picking of these products is finished, they are sent back to the crane, allowing a new product box to be exposed in the aisle instead. Completed order boxes are transported by conveyor to the packaging and outbound delivery areas.
Dahl's low-frequency goods are handled in the conventional racking warehouse. The picking and transportation of boxes in and out of the warehouse is handled by Swisslog's WMS solutions:WarehouseManager and AutomationManager (WM/AM). WM/AM controls the picker within each zone with the help of 'Pick-by-Voice' (voice-controlled picking technology).
Pickers select a customer box each marked with a check code for which to pick. They then receive instructions about which products and how many boxes are to be filled.When picking is complete in one zone, the picker places the box onto the conveyor system which automatically transfers it to the next zone. Here, a new picker takes over until the box is ready for outbound delivery. After picking is complete, the box is automatically sealed, wrapped and labelled for secure transport.
It is then transported onwards to sorting prior to outbound delivery.
Aside from increased warehouse capacity, the solution has enabled goods handling costs to be reduced and Dahl's own customer benefits to be increased through more efficient internal logistics. It also allows for shorter lead times, significantly more products on a smaller surface area and increased productivity.
Swisslog's relationship with Dahl has gone from strength to strength, with the appointment of Swisslog for a second (larger) automated warehouse project in 2011. This project incorporates Swisslog's SmartCarrier storage and transport technology, designed for highly dynamic logistics facilities storing totes.
Environmental responsibilities have been fundamental to the design and engineering of this new solution with all aspects of the system ensuring smooth weight optimisation, recuperated energy and efficient usage of motors.
Dahl Sverige AB (owned by Saint-Gobain) is Sweden's leading trading company for heating and sanitation services and industrial / property supplies. Having increased its number of products significantly and achieved escalating growth, Dahl started to outgrow its existing materials handling system and experienced queues forming at both its picking and filling storage areas.
Dahl's business ethic ensures that they constantly improve and streamline their operations and look for new solutions as a natural part of their daily work. Dahl acknowledged the importance of increasing their handling and storage capacity and provided clarification of their exact requirements: A solution which allowed more picking positions, a higher capacity and lower line costs.
This in turn led to them appointing Swisslog to supply an automated facility for customer order picking. Dahl's manual pallet warehouse was torn down and the new facility built in its place, without disrupting production.
The flow of goods at the new facility starts at the inbound goods arrivals area where products are repacked into plastic boxes before being weighed and measured for onward transportation to storage or to the picking area in the miniload facility. Picking takes place either directly into the cardboard delivery boxes or into plastic boxes. Cardboard boxes are erected automatically and are supplied to the picking zones via an integrated conveyor system. Customer order picking of smaller volumes takes place into plastic boxes, while larger order volumes are picked into cardboard boxes with the help of ergonomic picking stations in one of the twelve picking aisles, served by fast miniload cranes.
Picking takes place on two levels in the warehouse; on both the floor level and the mezzanine level. The majority of high frequency products are located in fixed pick positions.Midfrequency products are exposed in the picking station's aisles and once the picking of these products is finished, they are sent back to the crane, allowing a new product box to be exposed in the aisle instead. Completed order boxes are transported by conveyor to the packaging and outbound delivery areas.
Dahl's low-frequency goods are handled in the conventional racking warehouse. The picking and transportation of boxes in and out of the warehouse is handled by Swisslog's WMS solutions:WarehouseManager and AutomationManager (WM/AM). WM/AM controls the picker within each zone with the help of 'Pick-by-Voice' (voice-controlled picking technology).
Pickers select a customer box each marked with a check code for which to pick. They then receive instructions about which products and how many boxes are to be filled.When picking is complete in one zone, the picker places the box onto the conveyor system which automatically transfers it to the next zone. Here, a new picker takes over until the box is ready for outbound delivery. After picking is complete, the box is automatically sealed, wrapped and labelled for secure transport.
It is then transported onwards to sorting prior to outbound delivery.
Aside from increased warehouse capacity, the solution has enabled goods handling costs to be reduced and Dahl's own customer benefits to be increased through more efficient internal logistics. It also allows for shorter lead times, significantly more products on a smaller surface area and increased productivity.
Swisslog's relationship with Dahl has gone from strength to strength, with the appointment of Swisslog for a second (larger) automated warehouse project in 2011. This project incorporates Swisslog's SmartCarrier storage and transport technology, designed for highly dynamic logistics facilities storing totes.
Environmental responsibilities have been fundamental to the design and engineering of this new solution with all aspects of the system ensuring smooth weight optimisation, recuperated energy and efficient usage of motors.
MORE FROM THIS COMPANY
- The eco-friendly logistics of the future
- Axiom Telecom builds robot-based warehouse
- Keeping an eye on the big picture
- The essential guide to choosing the right warehouse automation partner
- Single CDC delivers supply chain efficiencies for Wärtsilä
- White Paper Download: Return Logistics
- DB Schenker Logistics takes on first CarryPick solution
- Swisslog cements number one slot
- Food firm selects Swisslog for new automated distribution centre
- Swisslog’s CarryPick installed for toy retailer
OTHER ARTICLES IN THIS SECTION