Home> | Automation | >Conveying components | >Watching the wage bill |
ARTICLE
Watching the wage bill
12 December 2012
A rapidly growing budget retailer specified a high bay warehouse extension to keep pace. Increased storage capacity and improved product pick efficiency, while maintaining low labour overheads,was delivered by SSI Schaefe
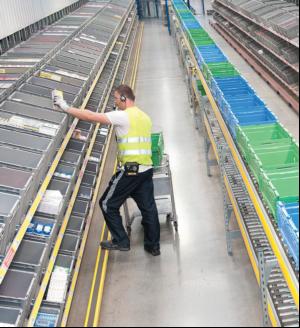
A rapidly growing budget retailer specified a high bay
warehouse extension to keep pace. Increased storage
capacity and improved product pick efficiency, while
maintaining low labour overheads,was delivered by SSI
Schaefer.
TJ Morris, trading as Home Bargains, is one of the UK's leading and fastest growing, privately owned discount retailers with over 300 stores.With plans to expand this number to over 500 stores by 2018, the business shows no sign of slowing down.
Working with supply chain consultants Total Logistics, the company developed a concept for the expansion of the dc at the company's HQ in Gillmoss, Liverpool, to facilitate growth.
With growing business comes growing demand for stock levels and quick turnaround for store replenishment - needing increased storage capacity, and maximum product pick efficiency while maintaining low labour overheads. TJ Morris in conjunction with Total Logistics, selected SSI Schaefer to deliver and exceed those expectations within its existing storage and distribution centre at Gillmoss.
SSI Schaefer were chosen to provide TJ Morris with an optimum solution that would not only address the immediate operational efficiencies but also provide a flexible solution to accommodate future growth within the business.
Close to reaching 'critical mass', the Home Bargains operation required a significant increase in bulk storage capacity - the decision was also made to make the whole picking operation more efficient and operator friendly. To augment the existing storage while accommodating the growing volume of palletised products, a 32 metre high-bay extension to the distribution centre was built.
The new extension, able to house more than 46,000 pallets, has 11 pallet cranes that feed products to more than 1,000 ground level picking locations and deliver replenishment orders to an adjacent miniload crane-based tote storage system, built to hold slower moving items, providing an additional storage capacity of up to 28,000 totes and 804 picking stations.
The storage totes, are provided in two sizes by SSI Schaefer, one to keep stored products and one to ship items out to store. Both pallet crane and mini-load storage areas are served by extensive pallet and tote conveyor systems.
Pallets arrive either pre-labelled or are labelled upon receipt and quickly inducted on to a pallet conveyor system, which has been designed to handle up to 300 pallets per hour. Two pallet checking stations, capable of processing 150 pallets per hour, check weight and identify broken blocks or bottom boards. A conveyor feed system into the high bay is mounted on a mezzanine floor with elevator access in order to avoid any obstruction to the picking operation.
Pallet cranes feed full pallets to casepicking aisles directly below the high bay storage locations, where cases are picked manually. Full pallets are routed by conveyor to the despatch area or to replenish stock in the mini-load storage system.
At the mini-load receiving stations pallets are placed upon hydraulic lifts, ergonomically designed to help operators break down and decant items into storage totes. The storage totes are then placed on a tote conveyor, which delivers direct to a mini-load crane docking station from where they are picked up and put away in the racking via a crane.
Waste cardboard generated by the process is taken away by an overhead belt conveyor to an external compactor.
Product bearing totes are subsequently delivered by the crane to picking locations in flow racks integrated within the miniload racking at ground level.
Operators, fed by a constant supply of conveyed empty totes, voice-pick products to fulfil multiple orders which, when completed, are placed on a takeaway conveyor and sent to a goods-out marshalling area, where they are automatically sorted by despatch route for waiting vehicles.
SSI Schaefer have fully automated both the strapping round boxes and the ink jet printing and application of labels on the strapping. The whole system is effectively controlled and managed using SSI Schaefer's Convey Warehouse Control System.
Joe Morris, operations director, TJ Morris, explains: "Without the expertise and systems technology provided by SSI Schaefer our operation would have struggled to meet the demands placed upon the business by the increased sales of a rapidly expanding store base throughout the UK.
"Expanding our storage capability and automating the most labour-intensive areas of our distribution operation has enabled us to expand and future-proof our operation without the need for continual investment in additional labour."
TJ Morris, trading as Home Bargains, is one of the UK's leading and fastest growing, privately owned discount retailers with over 300 stores.With plans to expand this number to over 500 stores by 2018, the business shows no sign of slowing down.
Working with supply chain consultants Total Logistics, the company developed a concept for the expansion of the dc at the company's HQ in Gillmoss, Liverpool, to facilitate growth.
With growing business comes growing demand for stock levels and quick turnaround for store replenishment - needing increased storage capacity, and maximum product pick efficiency while maintaining low labour overheads. TJ Morris in conjunction with Total Logistics, selected SSI Schaefer to deliver and exceed those expectations within its existing storage and distribution centre at Gillmoss.
SSI Schaefer were chosen to provide TJ Morris with an optimum solution that would not only address the immediate operational efficiencies but also provide a flexible solution to accommodate future growth within the business.
Close to reaching 'critical mass', the Home Bargains operation required a significant increase in bulk storage capacity - the decision was also made to make the whole picking operation more efficient and operator friendly. To augment the existing storage while accommodating the growing volume of palletised products, a 32 metre high-bay extension to the distribution centre was built.
The new extension, able to house more than 46,000 pallets, has 11 pallet cranes that feed products to more than 1,000 ground level picking locations and deliver replenishment orders to an adjacent miniload crane-based tote storage system, built to hold slower moving items, providing an additional storage capacity of up to 28,000 totes and 804 picking stations.
The storage totes, are provided in two sizes by SSI Schaefer, one to keep stored products and one to ship items out to store. Both pallet crane and mini-load storage areas are served by extensive pallet and tote conveyor systems.
Pallets arrive either pre-labelled or are labelled upon receipt and quickly inducted on to a pallet conveyor system, which has been designed to handle up to 300 pallets per hour. Two pallet checking stations, capable of processing 150 pallets per hour, check weight and identify broken blocks or bottom boards. A conveyor feed system into the high bay is mounted on a mezzanine floor with elevator access in order to avoid any obstruction to the picking operation.
Pallet cranes feed full pallets to casepicking aisles directly below the high bay storage locations, where cases are picked manually. Full pallets are routed by conveyor to the despatch area or to replenish stock in the mini-load storage system.
At the mini-load receiving stations pallets are placed upon hydraulic lifts, ergonomically designed to help operators break down and decant items into storage totes. The storage totes are then placed on a tote conveyor, which delivers direct to a mini-load crane docking station from where they are picked up and put away in the racking via a crane.
Waste cardboard generated by the process is taken away by an overhead belt conveyor to an external compactor.
Product bearing totes are subsequently delivered by the crane to picking locations in flow racks integrated within the miniload racking at ground level.
Operators, fed by a constant supply of conveyed empty totes, voice-pick products to fulfil multiple orders which, when completed, are placed on a takeaway conveyor and sent to a goods-out marshalling area, where they are automatically sorted by despatch route for waiting vehicles.
SSI Schaefer have fully automated both the strapping round boxes and the ink jet printing and application of labels on the strapping. The whole system is effectively controlled and managed using SSI Schaefer's Convey Warehouse Control System.
Joe Morris, operations director, TJ Morris, explains: "Without the expertise and systems technology provided by SSI Schaefer our operation would have struggled to meet the demands placed upon the business by the increased sales of a rapidly expanding store base throughout the UK.
"Expanding our storage capability and automating the most labour-intensive areas of our distribution operation has enabled us to expand and future-proof our operation without the need for continual investment in additional labour."
MORE FROM THIS COMPANY
- Quick ROI promised
- Wms gives picking technology a voice
- Pick and Pack for Longchamp
- Fast and flexible storage & retrieval
- North West appointment
- High bay offers relief
- SSI Schaefer with broad CeMAT offering
- Putting safety first
- Component supplier gets a lift
- Office Depot optimises order processing in DC retrofit
OTHER ARTICLES IN THIS SECTION