Home> | Warehouse IT | >Hardware | >Eliminating guesswork |
ARTICLE
Eliminating guesswork
12 December 2012
Having the right equipment working to maximum effect in a given storage and distribution system provides efficient, cost-effective load handling and helps companies increase productivity and cope with growth The ever i
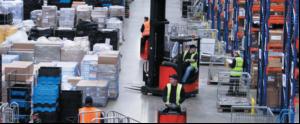
Having the right equipment working to maximum effect in a given storage and
distribution system provides efficient, cost-effective load handling and helps
companies increase productivity and cope with growth
The ever increasing demands of modern warehouses means more than ever that we need to remain close to our customers to understand their needs, as their requirements for a material handling supplier extend beyond just the hardware.
Linde Material Handling has a revolutionary warehouse planning and simulation tool to help its clients achieve maximum return on their investment by allowing warehouse projects to be accurately costed in the early planning stages.
Senior systems support analyst, Steve Porter, explains: "At Linde, we have developed a unique range of consultancy services and systems to meet each customer's specific needs and deliver added value to the customers' supply chain process. Our Stratos 3D warehouse planning and simulation tool is a perfect example of our expertise in action.
"Whether a customer is planning a new greenfield site or extending and modernising an existing facility, Stratos eliminates the guesswork and the risk.Working alongside the customer, our expert consultants use the tool to evaluate the customer's application data, including all projected storage and material flow demands for the facility. They will then use Stratos to identify the optimal storage system and configuration needed using modelling." Stratos is able to analyse all levels of a warehousing project and provide optimum storage layouts as well as a detailed view of the warehouse operation using dynamic simulations of pallet throughputs, order picking rates, truck movements and their consequent energy consumption. It can even be used to review marshalling areas and dock utilisation to control potential bottle necks.
The system will calculate the amount of racking needed to suit a specified layout, as well as both the number and type of truck required for each function. The findings are then rigorously tested and verified against real-time, on-screen simulation sequences of the optimum materials handling solution.
With the details of the loads to be stored, alternative racking layouts can be generated automatically, displayed on the screen and easily adjusted for best fit.
The system then provides 3D visuals of the warehouse to provide the client with a clear schematic overview of the project.
Important dimensional views such as beam heights, overall height of loads, aisle widths and operating clearances are all automatically generated, giving both client and designer an instant, detailed view to work with.
In major projects, after the design concept has been established, Stratos simulation techniques can then be applied to analyse and validate the potential throughput and material flow.
By programming the proposed delivery and despatch schedules and volumes, together with the activity levels of the material handling equipment, a dynamic on-screen simulation of the operation can be viewed verifying storage area and equipment utilisation, energy usage forecasts and delivery-on-time performance against targets.
Porter continues: "Stratos provides a complete overview so that modifications, adjustments and alternatives can be easily assessed to produce the best possible solution for the client's needs. The great benefit of using the system is that it allows our customers to confirm project viability at the planning stage before any commitment to major investment is made."
Stratos in action Linde Creighton first started working with Toolstation in 2008 to explore the material handling needs at its new NDC (National Distribution Centre) site in Redditch. The combination of the right product and business solution was a key factor for this customer. Using dynamic warehouse simulation programme, Stratos, Linde was able to help the customer design and deliver the most effective warehouse layout and right mix of trucks to maximise its productivity, performance and operating cost savings. Linde currently supplies Toolstation with a mixed fleet of over 20 trucks comprising the NDC's workhorse - the low and medium level order picker - as well as high level reach trucks, electric counterbalance, pedestrian powered pallet trucks and specialist very narrow aisle trucks to maximise additional warehouse storage capability in areas of the NDC site. With a product portfolio of over 10,000 catalogue items and a next day delivery customer commitment, product performance, reliability and service support are critical to the operation. Linde Material Handling provides a dedicated team of highly trained engineers to service and maintain the Toolstation fleet to ensure efficient day to day management of the NDC. Adam Keates, operations director, Toolstation says: "When Toolstation designed this warehouse from scratch, the Linde team was involved from the outset with the planning and organisation of our materials handling. One year on, the mix of trucks works perfectly, managing the extensive throughput and the fleet is performing to a very high standard."
The ever increasing demands of modern warehouses means more than ever that we need to remain close to our customers to understand their needs, as their requirements for a material handling supplier extend beyond just the hardware.
Linde Material Handling has a revolutionary warehouse planning and simulation tool to help its clients achieve maximum return on their investment by allowing warehouse projects to be accurately costed in the early planning stages.
Senior systems support analyst, Steve Porter, explains: "At Linde, we have developed a unique range of consultancy services and systems to meet each customer's specific needs and deliver added value to the customers' supply chain process. Our Stratos 3D warehouse planning and simulation tool is a perfect example of our expertise in action.
"Whether a customer is planning a new greenfield site or extending and modernising an existing facility, Stratos eliminates the guesswork and the risk.Working alongside the customer, our expert consultants use the tool to evaluate the customer's application data, including all projected storage and material flow demands for the facility. They will then use Stratos to identify the optimal storage system and configuration needed using modelling." Stratos is able to analyse all levels of a warehousing project and provide optimum storage layouts as well as a detailed view of the warehouse operation using dynamic simulations of pallet throughputs, order picking rates, truck movements and their consequent energy consumption. It can even be used to review marshalling areas and dock utilisation to control potential bottle necks.
The system will calculate the amount of racking needed to suit a specified layout, as well as both the number and type of truck required for each function. The findings are then rigorously tested and verified against real-time, on-screen simulation sequences of the optimum materials handling solution.
With the details of the loads to be stored, alternative racking layouts can be generated automatically, displayed on the screen and easily adjusted for best fit.
The system then provides 3D visuals of the warehouse to provide the client with a clear schematic overview of the project.
Important dimensional views such as beam heights, overall height of loads, aisle widths and operating clearances are all automatically generated, giving both client and designer an instant, detailed view to work with.
In major projects, after the design concept has been established, Stratos simulation techniques can then be applied to analyse and validate the potential throughput and material flow.
By programming the proposed delivery and despatch schedules and volumes, together with the activity levels of the material handling equipment, a dynamic on-screen simulation of the operation can be viewed verifying storage area and equipment utilisation, energy usage forecasts and delivery-on-time performance against targets.
Porter continues: "Stratos provides a complete overview so that modifications, adjustments and alternatives can be easily assessed to produce the best possible solution for the client's needs. The great benefit of using the system is that it allows our customers to confirm project viability at the planning stage before any commitment to major investment is made."
Stratos in action Linde Creighton first started working with Toolstation in 2008 to explore the material handling needs at its new NDC (National Distribution Centre) site in Redditch. The combination of the right product and business solution was a key factor for this customer. Using dynamic warehouse simulation programme, Stratos, Linde was able to help the customer design and deliver the most effective warehouse layout and right mix of trucks to maximise its productivity, performance and operating cost savings. Linde currently supplies Toolstation with a mixed fleet of over 20 trucks comprising the NDC's workhorse - the low and medium level order picker - as well as high level reach trucks, electric counterbalance, pedestrian powered pallet trucks and specialist very narrow aisle trucks to maximise additional warehouse storage capability in areas of the NDC site. With a product portfolio of over 10,000 catalogue items and a next day delivery customer commitment, product performance, reliability and service support are critical to the operation. Linde Material Handling provides a dedicated team of highly trained engineers to service and maintain the Toolstation fleet to ensure efficient day to day management of the NDC. Adam Keates, operations director, Toolstation says: "When Toolstation designed this warehouse from scratch, the Linde team was involved from the outset with the planning and organisation of our materials handling. One year on, the mix of trucks works perfectly, managing the extensive throughput and the fleet is performing to a very high standard."
MORE FROM THIS COMPANY
- Order picking at medium rack height
- Expansion for Linde
- Stand-on truck for one ton payload
- Used stacker fits the mould
- Flexible trucks for auto and manned use
- Morrisons uses Linde hire trucks to adapt to changing needs
- Long term value offer
- Compact & approved
- Linde 'prepared for Brexit no matter what'
- Linde heavy truck plant in Wales could close
OTHER ARTICLES IN THIS SECTION