Home> | Automation | >Conveying components | >Dynamic picking solution |
ARTICLE
Dynamic picking solution
12 December 2012
A combination of vertical picking towers, sortation conveyors, RF barcode scanners and WMS provided industrial products supplier ERIKS UK with an order fulfilment solution at its seals warehouse in Dudley Chess Logist
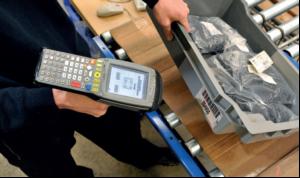
A combination of vertical picking towers, sortation
conveyors, RF barcode scanners and WMS provided
industrial products supplier ERIKS UK with an order
fulfilment solution at its seals warehouse in Dudley
Chess Logistics Technology integrated a solution for Eriks around its Empirica application to manage all warehouse, stock and picking operations dynamically and in real time while also providing a seamless link with existing business applications.
"This highly efficient solution supports our business and manages the complete stock control and picking process so that we fulfil the maximum number of orders every day," says Peter Timbrell, Logistics Director at ERIKS UK. "It helps us provide the very high levels of information, quality of service and product availability expected by our customers." ERIKS serves the OEM (original equipment manufacture) and MRO (maintenance repair operations) sectors and this presents some challenges to the picking operation which relies on many stock and customer-focused parameters to maintain the high level of customer service. OEM orders are reasonably predictable but MRO requires adaptability to provide an on-demand service. Some customers are unconcerned with first-infirst- out (FIFO) sourcing but require items made with a specific date range while some want items from a batch they have tested. Some want additional codes or markings applied to products. ERIKS has to meet these requirements while maintaining a high level of operational efficiency with low transaction costs.
At the Seals warehouse, the company stocks upwards of 12,000 product lines and orders can be for single items costing hundreds of pounds for specialist applications through to thousands of lower cost items for high volume manufacturing. Order picking has to be flexible enough to cope with both extremes and everything in between. The company despatches to an average 240 sites every night which includes deliveries despatched direct to the customer and to its own network of branches around the UK and Ireland.
In the new facility, six Hänel vertical picking towers ("Lean Lifts") are positioned along the centre of the building to make full use of the 12 metre height. Stock is stored on trays which are brought down to the picking face automatically acting on instructions received directly from the WMS. Pick-tolight technology then indicates the location of the correct item. A conveyor and sortation system provided by Keymas runs from the picking face to order rework and assembly areas at the front of the building.
Picking and other tasks are managed using hand-held RF terminals which issue instructions to warehouse staff and scan barcodes at various points to verify actions.
This equipment is driven by the Empirica WMS which sends pick instructions direct to the Lean Lifts and prioritises and balances the picking sequence across all six towers.
While the operative is retrieving an item from one machine the others are transferring trays to the pick face. The picker moves from machine to machine, directed by "next task" instructions on their RF terminals. This ensures no time is wasted waiting for an item to be available and minimises the walking between machines for maximum productivity and efficiency.
"We envisaged two operatives would work three towers each," says Peter Timbrell. "But it was soon clear that one person could manage all six and they now only spend half their time on picking tasks.
In the previous operation four people spent all their time on order picking." The system recognises when complete orders cannot be fulfilled from the Lean Lifts and instead directs the warehouse team to pick directly from bulk. This avoids complexity and duplication of tasks.
Picked items are placed in a bag and a label generated by Empirica is attached.
Customers' own part numbers can be included but only relevant information is printed. This avoids the inclusion of blank lines or spaces which could lead customers to assume information is missing. The bag is placed in a bar-coded tote bin and directed through the sortation system to one of two locations. The first is for completed orders and the second for items that require additional rework prior to delivery (customising). Rework forms an increasing proportion of the total service and added value offered by ERIKS. It can include special packaging, additional spot codes or the application of holographic labels used by some customers in their own quality assurance.
The entire system is driven by a hierarchy of priorities and tasks managed dynamically and in real time by Empirica.
Stock orders have a lower priority than customer orders but emergencies always take precedence. The prioritisation also ensures that orders not required to be despatched that day are held back until the next, freeing resources for those that can be delivered. Putaway and stock checking are always a lower priority which means that these tasks are only allocated when there are no outstanding orders.
Chess worked with Hänel's UK distributor Industore to write the interface which directs the Lean Lifts and liaised with Keymas to source information needed to drive the sortation system. The company set up the RF network, configured the hand-held scanners and provided training to the ERIKS staff.
Empirica also provides an interface between the warehouse operations and ERIKS' ERP system to ensure a seamless and automatic transfer of information with main business software applications.
Putaway is managed with items allocated to random locations while taking into account the need to balance stock across all six picking towers. The system flags up missing critical information and forces operatives to enter the correct details before they can proceed. Automatic stock checking is configured so that operatives are asked to check stock when no picking tasks are scheduled.
"We believe we could complete eight full checks a year this way," says Peter Timbrell. "It far outweighs anything expected by our auditors."
Chess Logistics Technology integrated a solution for Eriks around its Empirica application to manage all warehouse, stock and picking operations dynamically and in real time while also providing a seamless link with existing business applications.
"This highly efficient solution supports our business and manages the complete stock control and picking process so that we fulfil the maximum number of orders every day," says Peter Timbrell, Logistics Director at ERIKS UK. "It helps us provide the very high levels of information, quality of service and product availability expected by our customers." ERIKS serves the OEM (original equipment manufacture) and MRO (maintenance repair operations) sectors and this presents some challenges to the picking operation which relies on many stock and customer-focused parameters to maintain the high level of customer service. OEM orders are reasonably predictable but MRO requires adaptability to provide an on-demand service. Some customers are unconcerned with first-infirst- out (FIFO) sourcing but require items made with a specific date range while some want items from a batch they have tested. Some want additional codes or markings applied to products. ERIKS has to meet these requirements while maintaining a high level of operational efficiency with low transaction costs.
At the Seals warehouse, the company stocks upwards of 12,000 product lines and orders can be for single items costing hundreds of pounds for specialist applications through to thousands of lower cost items for high volume manufacturing. Order picking has to be flexible enough to cope with both extremes and everything in between. The company despatches to an average 240 sites every night which includes deliveries despatched direct to the customer and to its own network of branches around the UK and Ireland.
In the new facility, six Hänel vertical picking towers ("Lean Lifts") are positioned along the centre of the building to make full use of the 12 metre height. Stock is stored on trays which are brought down to the picking face automatically acting on instructions received directly from the WMS. Pick-tolight technology then indicates the location of the correct item. A conveyor and sortation system provided by Keymas runs from the picking face to order rework and assembly areas at the front of the building.
Picking and other tasks are managed using hand-held RF terminals which issue instructions to warehouse staff and scan barcodes at various points to verify actions.
This equipment is driven by the Empirica WMS which sends pick instructions direct to the Lean Lifts and prioritises and balances the picking sequence across all six towers.
While the operative is retrieving an item from one machine the others are transferring trays to the pick face. The picker moves from machine to machine, directed by "next task" instructions on their RF terminals. This ensures no time is wasted waiting for an item to be available and minimises the walking between machines for maximum productivity and efficiency.
"We envisaged two operatives would work three towers each," says Peter Timbrell. "But it was soon clear that one person could manage all six and they now only spend half their time on picking tasks.
In the previous operation four people spent all their time on order picking." The system recognises when complete orders cannot be fulfilled from the Lean Lifts and instead directs the warehouse team to pick directly from bulk. This avoids complexity and duplication of tasks.
Picked items are placed in a bag and a label generated by Empirica is attached.
Customers' own part numbers can be included but only relevant information is printed. This avoids the inclusion of blank lines or spaces which could lead customers to assume information is missing. The bag is placed in a bar-coded tote bin and directed through the sortation system to one of two locations. The first is for completed orders and the second for items that require additional rework prior to delivery (customising). Rework forms an increasing proportion of the total service and added value offered by ERIKS. It can include special packaging, additional spot codes or the application of holographic labels used by some customers in their own quality assurance.
The entire system is driven by a hierarchy of priorities and tasks managed dynamically and in real time by Empirica.
Stock orders have a lower priority than customer orders but emergencies always take precedence. The prioritisation also ensures that orders not required to be despatched that day are held back until the next, freeing resources for those that can be delivered. Putaway and stock checking are always a lower priority which means that these tasks are only allocated when there are no outstanding orders.
Chess worked with Hänel's UK distributor Industore to write the interface which directs the Lean Lifts and liaised with Keymas to source information needed to drive the sortation system. The company set up the RF network, configured the hand-held scanners and provided training to the ERIKS staff.
Empirica also provides an interface between the warehouse operations and ERIKS' ERP system to ensure a seamless and automatic transfer of information with main business software applications.
Putaway is managed with items allocated to random locations while taking into account the need to balance stock across all six picking towers. The system flags up missing critical information and forces operatives to enter the correct details before they can proceed. Automatic stock checking is configured so that operatives are asked to check stock when no picking tasks are scheduled.
"We believe we could complete eight full checks a year this way," says Peter Timbrell. "It far outweighs anything expected by our auditors."
MORE FROM THIS COMPANY
OTHER ARTICLES IN THIS SECTION