Home> | Automation | >Automated handling | >Firm fined after arm severed |
ARTICLE
Firm fined after arm severed
12 December 2012
A Suffolk-based animal feed manufacturer has been fined after a worker lost his arm when it became entangled in a conveyor. Christopher Brennan, 35, from Norwich, was attempting to clear a blockage on a conveyor at
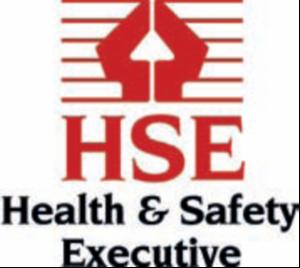
A Suffolk-based animal feed
manufacturer has been
fined after a worker lost
his arm when it became
entangled in a conveyor.
Christopher Brennan, 35, from Norwich, was attempting to clear a blockage on a conveyor at the Burston Mill site of BOCM Pauls, when his right arm became entangled and was severed just below the elbow. Since the incident on 20 September 2011 he has been unable to work.
Norwich Magistrates' Court heard that BOCM Pauls had failed to provide a safe system of work for production staff to clear blockages on conveyors and there were no guards to prevent access to the unblocking hatch.
The Health and Safety Executive (HSE) prosecuted the company after its investigation found that blockages happened regularly but there were inadequate methods for clearing them. In addition, isolators for the conveyors' power supply were located out of reach with no safe means to access them.
Christopher Brennan, 35, from Norwich, was attempting to clear a blockage on a conveyor at the Burston Mill site of BOCM Pauls, when his right arm became entangled and was severed just below the elbow. Since the incident on 20 September 2011 he has been unable to work.
Norwich Magistrates' Court heard that BOCM Pauls had failed to provide a safe system of work for production staff to clear blockages on conveyors and there were no guards to prevent access to the unblocking hatch.
The Health and Safety Executive (HSE) prosecuted the company after its investigation found that blockages happened regularly but there were inadequate methods for clearing them. In addition, isolators for the conveyors' power supply were located out of reach with no safe means to access them.
MORE FROM THIS COMPANY
- Lack of planning and supervision behind heavy lifting injury
- Worker falls through warehouse roof
- Worker pinned after door collapse
- Overhead crane worker suffers life threatening injuries
- Workers burned when crane spilled 300 tonnes of molten steel at Tata
- Spark from forklift causes explosion at waste firm
- Worker seriously injured in warehouse roof fall
- Associated British Ports fined after 600kg bag falls on employee
- Warburtons fined nearly £2 million after conveyor injury
- Operator killed in loading operation
OTHER ARTICLES IN THIS SECTION