Home> | Automation | >Conveying components | >New Synchronous Drum Motor: energy-efficient and powerful |
ARTICLE
New Synchronous Drum Motor: energy-efficient and powerful
12 December 2012
The new space-saving 80mm diameter Interroll Synchronous Drum Motor is the most powerful, energy-efficient generation of drum motors ever developed, enabling one drive system to suit all needs and speeds (0.01 m/s up to
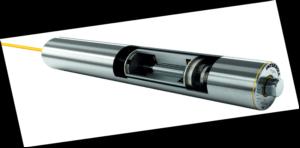
The new space-saving 80mm diameter
Interroll Synchronous Drum Motor is
the most powerful, energy-efficient
generation of drum motors ever developed,
enabling one drive system to suit all needs and
speeds (0.01 m/s up to 4.5 m/s). Easy-to-install,
this is the most eco-friendly drive solution for
belt conveyors in the areas of food processing,
packaging, checkweighing, automotive, logistic
and many more industrial applications.
Unlike externally mounted geared motors with secondary transmission, the new Synchronous Drum Motor easily integrates within a conveyor due to its all-in-one design and compact size.
The planetary gearbox transfers 92-95% of the available electric motor power directly linear to the conveyor system, providing a total output efficiency of up to 82%. This means that the mechanical power loss in comparison to other drum motors or conventional motors with secondary transmission is dramatically reduced.
This energy saving drive solution offers excellent start-stop performance, optimum torque at all speeds, a maximum acceleration/braking performance and low operating drum temperature of approx 45° C, making them ideal for conveying temperature sensitive or perishable goods, whilst also reducing the risk of bacteria propagation. These drives require zero maintenance and can be installed in wet and high pressure wash down applications.
Acceleration from zero to 100 percent can be achieved in milliseconds and when fitted with a servo drive and feedback system, this can be increased up to 151 m/s2 depending on the motor type and load. Intermittent movements on conveyor systems for pick and place, filling or cutting as well as discharge operations or automated check-in terminals can be significantly speeded up.
Precision control with Interroll IFIIP55 Frequency Inverter When used with Interroll's new Frequency Inverter IFI-IP55 and vector control, the performance of conveyor belt systems can be substantially enhanced to provide a greater flexibility in respect of acceleration, deceleration, braking and soft start and stops. Easy-to-install and ready to operate immediately, Interroll's IP55 Frequency Inverter for decentralised deployment is the most cost-efficient solution available.
Whether conventional rubber, PVC or PU belts, plastic modular belts, steel wire belts, chain drives or timing belt applications, Interroll can offer the drive system to suit all applications.
For further information contact: Liam Preston Drives & Rollers: Interroll Ltd., Brunel Road, Earlstrees Industrial Estate GB-Corby, Northants, NN17 4UX Tel: (01536) 748531 Fax: +44(0) 1536 748 515 e.mail: [email protected] Website: www.interroll.com
Unlike externally mounted geared motors with secondary transmission, the new Synchronous Drum Motor easily integrates within a conveyor due to its all-in-one design and compact size.
The planetary gearbox transfers 92-95% of the available electric motor power directly linear to the conveyor system, providing a total output efficiency of up to 82%. This means that the mechanical power loss in comparison to other drum motors or conventional motors with secondary transmission is dramatically reduced.
This energy saving drive solution offers excellent start-stop performance, optimum torque at all speeds, a maximum acceleration/braking performance and low operating drum temperature of approx 45° C, making them ideal for conveying temperature sensitive or perishable goods, whilst also reducing the risk of bacteria propagation. These drives require zero maintenance and can be installed in wet and high pressure wash down applications.
Acceleration from zero to 100 percent can be achieved in milliseconds and when fitted with a servo drive and feedback system, this can be increased up to 151 m/s2 depending on the motor type and load. Intermittent movements on conveyor systems for pick and place, filling or cutting as well as discharge operations or automated check-in terminals can be significantly speeded up.
Precision control with Interroll IFIIP55 Frequency Inverter When used with Interroll's new Frequency Inverter IFI-IP55 and vector control, the performance of conveyor belt systems can be substantially enhanced to provide a greater flexibility in respect of acceleration, deceleration, braking and soft start and stops. Easy-to-install and ready to operate immediately, Interroll's IP55 Frequency Inverter for decentralised deployment is the most cost-efficient solution available.
Whether conventional rubber, PVC or PU belts, plastic modular belts, steel wire belts, chain drives or timing belt applications, Interroll can offer the drive system to suit all applications.
For further information contact: Liam Preston Drives & Rollers: Interroll Ltd., Brunel Road, Earlstrees Industrial Estate GB-Corby, Northants, NN17 4UX Tel: (01536) 748531 Fax: +44(0) 1536 748 515 e.mail: [email protected] Website: www.interroll.com
MORE FROM THIS COMPANY
- Smart pallet movers for manufacturing logistics
- Carton Versi Flow converts pallet racking into dynamic carton flow store
- Optimum solution for 24V DC conveyor technology
- New oil-free drum motor
- Interroll sorters an eCommerce solution
- Space saving unit promises low noise operation and extended belt lifetime
- Interroll couriers favour with express parcel sorting
- New chief technology officer for Interroll
- Greater power & efficiency
- Maximum flexibility with optimised Carton Wheel Flow
OTHER ARTICLES IN THIS SECTION