Home> | Automation | >Automated handling | >Optimum solution for 24V DC conveyor technology |
Home> | Automation | >Conveying components | >Optimum solution for 24V DC conveyor technology |
Optimum solution for 24V DC conveyor technology
22 November 2013
Interroll’s latest ConveyorControl has streamlined the management of 24V drive technology for system integrators, plant manufacturers and end-users, providing for maximum cost efficiency. The overall system can be rapidly installed and commissioned to provide flexible, simple configuration and continuous IP54 protection rating in order to meet the requirements for industrial installations.
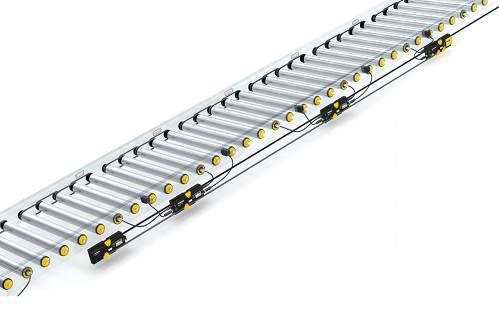
The Interroll ConveyorControl focuses on flexible tote conveyor technology and provides a versatile, smart control solution for continuous and zero pressure accumulation conveyors. The key elements of this solution are its mechanically sound, fast-speed 24 V 'RollerDrives' with inbuilt controls that can be linked to existing stock control software.
The control platform consists of four different modules, a power pack and the Configurator software that are matched for optimum performance. The independent length of standard ASI cable, incorporating piercing technology, provides for rapid, safe and low cost installation on site.
Real Energy Savings
Each zero pressure accumulation roller conveyor is divided into zones, with the length of each zone being determined by the size of the goods to be conveyed. With conventional technology, segmentation of conveyor systems usually involves the use of a central drive for one long roller conveyor, which runs constantly and independently of throughput volumes. This means the system constantly consumes energy and unnecessarily increases the degree of wear and tear on the system, even when nothing is being conveyed.
The Interroll ConveyorControl system, based on individual zones driven by RollerDrives, only activates to power the actual zones when and where there are totes to be conveyed. Such switching on and off of decentralised drives according to need is a key factor in achieving the enhanced energy efficiency of such a conveyor system and reduces the associated time and cost spent on maintenance. Depending on the mechanical components used, a three to four time’s greater lifespan can be expected when a ConveyorControl concept is in place – a significant factor in reducing the overall cost of any system!
Another feature of the RollerDrive option harnesses further energy savings. The re-circulated braking energy resulting from cyclical operation is diverted to other drives within the system. This significantly reduces the primary supply consumption of the accumulating conveyor, while at the same time relieving the thermal pressure on the brushless motor of the RollerDrive. The end result is increased throughput volumes and enhanced overall performance of the logistics centre.
Flexible configuration of the interfaces
Conveniently configurable offline via PC, these new control units make complex, costly PLC programming a thing of the past, as well as simplifying the process of installation and reducing the required commissioning time.
There are two distinct control modules – CentralControl allows ConveyorControl to be configured and all parameters created through a PC interface. Software supplied with this module facilitates adaption to a wide range of conveyor applications. Using preset standard functionality, there is no requirement for timely and costly programming with PLC.
The GatewayControl enables connection to high level control so that ConveyorControl system can be easily integrated in already existing Profibus and Profinet environments. This is made possible with only a simple wiring connection, where many complex connections would have been required previously.
The Configurator is a PC-based graphical user interface for setting all the essential mandatory parameters of the ConveyorControl such as Accumulation logic, direction, speed, etc. and this is all made very simple by connecting the CentralControl to a laptop.
Interroll RollerDrive and ConveyorControl combined provide fast, efficient and reliable drive and control standards in unit conveyor technology. For detailed technical information contact Telephone: 01536 312770 or visit or website www.interroll.com
- Cross belt sorters from Interroll an economical solution
- Quick conveyor assembly with modular concept
- Smart conveying systems optimise tyre manufacturers' material flow
- Centre of Excellence established
- Hilton Campbell appointed new Interroll UK MD
- Integrated drive solutions
- Conveyor solutions for chilled and deep-freeze environments
- Getrag Ford Transmissions gear up with Interroll Dynamic Storage
- Maximum flexibility with optimised new Carton Wheel Flow
- In Dublin’s fair city