Home> | Industry Sector | >Distribution | >Storage revamp reduces forklifts used from 15 to six |
Home> | Industry Sector | >Manufacturing | >Storage revamp reduces forklifts used from 15 to six |
Home> | Warehouse Storage | >Racking & shelving | >Storage revamp reduces forklifts used from 15 to six |
Storage revamp reduces forklifts used from 15 to six
23 May 2016
A Midlands steel stockholder automated its storage, revamping its operations.
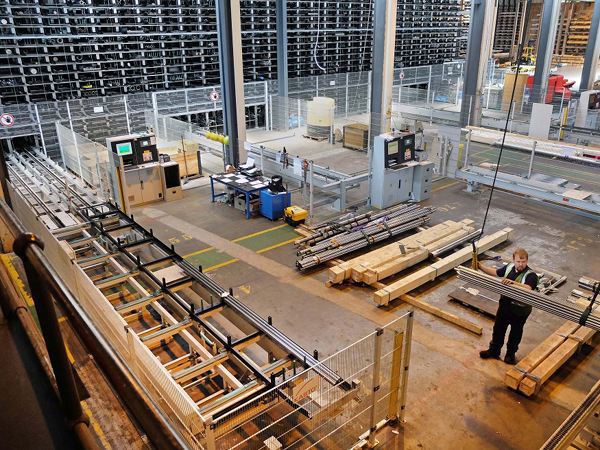
Oldbury-based Bohler-Uddeholm (UK) invested £3 million in a KASTO Uunicompact system and a further £1m in other site improvements.
The computer-controlled storage and retrieval system became operational in the first quarter of 2016, taking over from cantilever racking.
The number of forklift trucks on site has been cut from 15 to 6, reducing overheads, making the working environment safer for personnel and cutting diesel emissions. In addition, warehouse operator costs have been lowered by 15 per cent, with personnel redeployed to other duties.
There has been an 80 per cent saving in floor area. The KASTO store has a 1,000m2 footprint, whereas previously 5,500m2 was required to stock 2,600 tonnes of material, although the new tower can hold double that amount. The freed floor space will be used for added-value processing.
MD Tom Gowans says: “The automated warehouse has already started to raise our competitiveness and will underpin our planned 50% growth in throughput by 2020, increasing turnover from £50 million to £75 million.
“It will also benefit our customers, as we can now ensure same-day picking and despatch for all orders received before noon. In the past, during busy periods, we could not guarantee that. Average lead-time has consequently halved to one-and-a-half days.
“The operational savings from investing in the automated warehouse will be further increased by moving from 24/5 working to a double shift pattern later this year when the new system has bedded in.
“Taking all of the economies into account, return on investment will be within three to five years, depending on the business climate and in particular a recovery in the oil and gas sector, which is an important part of our business.”
The automated storage and retrieval facility is 15 metres high and has been built onto the end of the original warehouse at Oldbury, which is nine metres high. Exterior parts of the extension have weatherproof cladding, including a 26 metre long end wall and the four sides of the tower that are above the nine-metre roof line.
An integrated, overhead gantry crane feeds 12 cassette buffer stations, where operators put material away into store and pick orders. Some material is transferred to 17 automatic bandsaws and on to other machine tools, all of which are now close to the store. Previously, material on racking had to be found by the picker and moved through two bays by lift truck for processing. It entailed significant operational cost disadvantages, health & safety risks associated with manual material movement and potential delays in supplying customers.
- Liebherr upgrades automated metal storage
- Pick-by-light added to automated metal handling
- Productivity boost
- Metal storage
- High storage density
- Steeled for growth
- Kasto unveils storage innovation
- Streamline efficiency for holding and picking metals
- Energy recovery and storage system
- High-density automated storage for steel firm