Handling and inventory halved
PRECISION ENGINEERING firm Werner Weitner has centralised a large part of its activities in a new factory building.
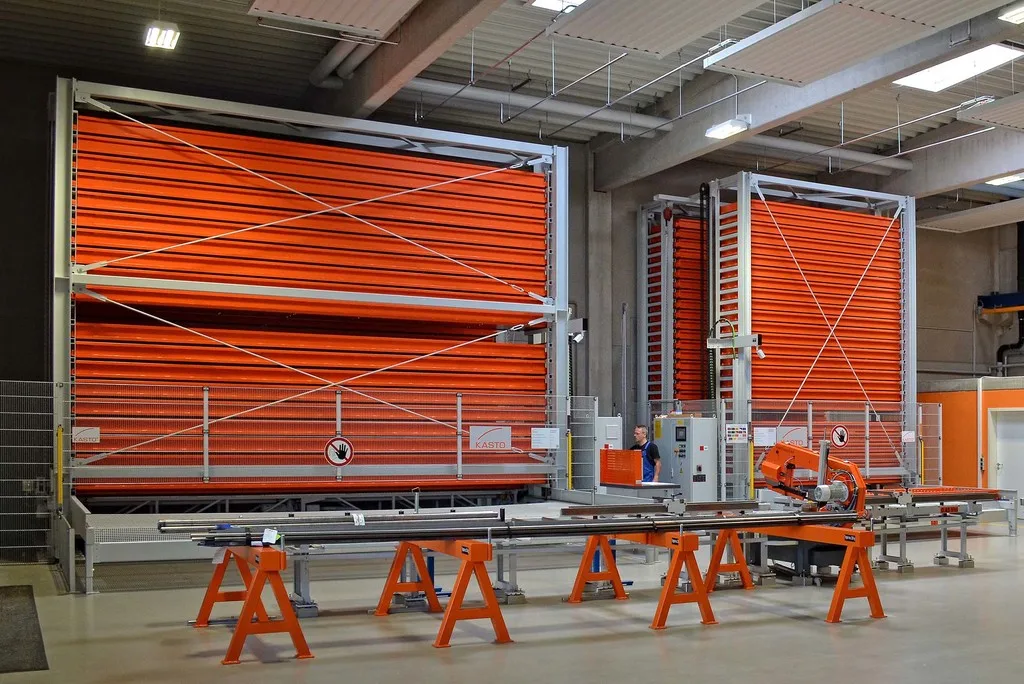
In the process, raw material storage has been updated by the installation of two UNITOWER systems from KASTO, which save time, space as well as improving ergonomics.
The difficulty previously was that logistics had become more and more difficult. The effort needed to transport parts and materials back and forth between the individual manufacturing processes around the site was cumbersome. The problem was compounded by the large variety of materials stored, including steels, alloys, aluminium and resins. As the company's customers expect short delivery times, the materials have to be stored in significant quantities to allow Werner Weitner to respond quickly to orders, which can involve anything from one-off prototypes through to series production.
To optimise efficiency of material flow in the new factory, KASTO recommended installing two freestanding dual tower storage systems. The UNITOWER 1.0 is suitable for storing and retrieving bar stock up to three metres in length, while the UNITOWER 2.0 has the capacity to handle material up to six metres long.
Containing 52 and 41 cassettes respectively, the storage systems provide in a small footprint ample space for raw material. The location of products in the individual cassettes is stored in the warehouse management system. It is connected via a customised standard interface to the manufacturer's proALPHA ERP software and operated either via a control panel directly at the storage system or via a mobile hand-held unit.
Based on the material-to-operator principle, an operating gantry crane supplies cassettes automatically to the output station. Workflow is significantly more ergonomic and assignment errors have been virtually eliminated. The short access times of the UNITOWER enable the company to process pending orders quickly.
On average, approximately 45 cassettes are moved per day. Whereas in the past a piece of material ran through up to eight handling steps on the way to becoming a finished item, thanks to the tower storage systems and more efficient processing, this number has been halved. Moreover, the inventory of raw material stored has also been halved due to the ability to hold it in a central location. It has resulted in less capital tied up in raw material and extra space for value-added activities.
For more information, visit www.kasto.com