Home> | Automation | >Conveying components | >A to B? More like A to Z |
ARTICLE
A to B? More like A to Z
12 December 2012
Conveying is more than transporting goods from A to B. Knapp UK head of sales & marketing Craig Rollason explains how high quality in design and manufacture can add value An efficient and flexible transport system fo
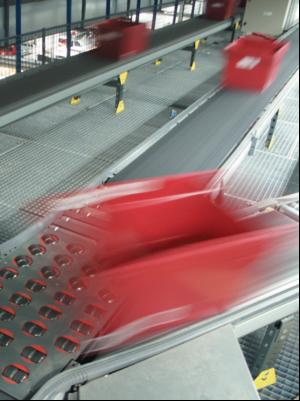
Conveying is more than transporting
goods from A to B. Knapp UK head of
sales & marketing Craig Rollason
explains how high quality in design and
manufacture can add value
An efficient and flexible transport system forms the foundation of almost every logistics solution.With their modular design and various types, conveyors are often the ideal solution to internal transport needs.With belt, roller and chain varieties - including both powered and non-powered sections - conveyor systems can be adapted to suit virtually every application, forming the backbone of most pallet- and totehandling distribution centres. In many cases, they drive the productivity of the whole handling system.
For example, Knapp is installing an automated warehouse system for a client in the cosmetics industry in Brazil that will handle 5 million single unit picks per day - a figure that's simply unthinkable without efficient conveyor systems. Nearer to home, Knapp in the UK has recently delivered the largest pharmaceutical warehouse in Europe - for The Co-operative Pharmacy in Stoke-on-Trent - which handles 420,000 items per day with the help of 3,700 metres of conveyor systems.
Complex handling solutions such as these prove that conveyor sorting technology is a key factor in many of today's conveyor installations, with a plethora of sorting technologies - such as pop-up wheel transfers, pushers and belt transfers - integrated into today's conveyor systems.
To say that advances in conveyor technology over the last 30 years have been significant would be something of an understatement. Conveyors have evolved to meet the demanding environments of modern processing and distribution centres with key features being availability, speed, minimal noise, safety and flexibility. Knapp conveyors can transport unit loads of up to 60kg at speeds of up to 180 metres per minute, allowing the movement of 10,000 totes per hour with noise emission no higher than 58 dBA.
With the focus of the industry shifting to lifetime costs, conveyor manufacturers have improved the ease with which their systems can be installed and maintained. Our conveyor products are now designed in a way that allows them to be prefabricated, fully tested and shipped complete, giving 'plug and play' functionality. Cables are fitted from above for simple installation and there are two separate areas to accommodate cables - one inside and one outside of the product - with maintenancefriendly covers. Our roller conveyor features an interlocking system for rapid replacement of rollers and, where suitable, nondriven modules - which require minimal maintenance - are employed. Identical parts are used, where possible, in order to reduce the spare parts stock. This is a key element in Knapp's Low Complexity Warehouse concept, which aims to reduce the number of technologies used in the warehouse in order to minimise ongoing costs.
Despite advances, clients often see conveyors as a standard product that does not require a high specification.We believe small differences in design can make a large difference to performance. Of course, there is a cost to conveyor specialists in making these incremental improvements.We have consistently invested 12% of turnover in research & development in recent years. Unlike some of our competitors, who have moved their metalworking operations to lower-cost Eastern European sites, we know the value of having our R&D, production, quality management and software teams all on one site at our headquarters in Graz, Austria.
There is no doubt that this kind of investment pays off. Our R&D resulted, for example, in the launch of the OSR system, which integrates conveyors, automated storage and pick-by-light.
The OSR offers four times the number of totes in/out per hour than a conventional ASRS, yet uses 10% less energy.
An efficient and flexible transport system forms the foundation of almost every logistics solution.With their modular design and various types, conveyors are often the ideal solution to internal transport needs.With belt, roller and chain varieties - including both powered and non-powered sections - conveyor systems can be adapted to suit virtually every application, forming the backbone of most pallet- and totehandling distribution centres. In many cases, they drive the productivity of the whole handling system.
For example, Knapp is installing an automated warehouse system for a client in the cosmetics industry in Brazil that will handle 5 million single unit picks per day - a figure that's simply unthinkable without efficient conveyor systems. Nearer to home, Knapp in the UK has recently delivered the largest pharmaceutical warehouse in Europe - for The Co-operative Pharmacy in Stoke-on-Trent - which handles 420,000 items per day with the help of 3,700 metres of conveyor systems.
Complex handling solutions such as these prove that conveyor sorting technology is a key factor in many of today's conveyor installations, with a plethora of sorting technologies - such as pop-up wheel transfers, pushers and belt transfers - integrated into today's conveyor systems.
To say that advances in conveyor technology over the last 30 years have been significant would be something of an understatement. Conveyors have evolved to meet the demanding environments of modern processing and distribution centres with key features being availability, speed, minimal noise, safety and flexibility. Knapp conveyors can transport unit loads of up to 60kg at speeds of up to 180 metres per minute, allowing the movement of 10,000 totes per hour with noise emission no higher than 58 dBA.
With the focus of the industry shifting to lifetime costs, conveyor manufacturers have improved the ease with which their systems can be installed and maintained. Our conveyor products are now designed in a way that allows them to be prefabricated, fully tested and shipped complete, giving 'plug and play' functionality. Cables are fitted from above for simple installation and there are two separate areas to accommodate cables - one inside and one outside of the product - with maintenancefriendly covers. Our roller conveyor features an interlocking system for rapid replacement of rollers and, where suitable, nondriven modules - which require minimal maintenance - are employed. Identical parts are used, where possible, in order to reduce the spare parts stock. This is a key element in Knapp's Low Complexity Warehouse concept, which aims to reduce the number of technologies used in the warehouse in order to minimise ongoing costs.
Despite advances, clients often see conveyors as a standard product that does not require a high specification.We believe small differences in design can make a large difference to performance. Of course, there is a cost to conveyor specialists in making these incremental improvements.We have consistently invested 12% of turnover in research & development in recent years. Unlike some of our competitors, who have moved their metalworking operations to lower-cost Eastern European sites, we know the value of having our R&D, production, quality management and software teams all on one site at our headquarters in Graz, Austria.
There is no doubt that this kind of investment pays off. Our R&D resulted, for example, in the launch of the OSR system, which integrates conveyors, automated storage and pick-by-light.
The OSR offers four times the number of totes in/out per hour than a conventional ASRS, yet uses 10% less energy.
MORE FROM THIS COMPANY
- Support engineers on-site
- Automation facilitates online sales growth
- Response to rapid growth
- British Gas renews with KNAPP
- The adidas Group automates with KNAPP
- KNAPP wins shuttle storage contract with Hugo Boss
- Large-scale automated operation for 3PL
- Clarks' automated warehouse hits 10 year milestone
- KNAPP to focus on horizontal transport at WTG Live
- 1000th SHUTTLE
OTHER ARTICLES IN THIS SECTION