Home> | Automation | >Automated handling | >Accurate order picking with an A-Frame |
ARTICLE
Accurate order picking with an A-Frame
12 December 2012
Racking from BITO Storage Systems is playing a key role in maintaining the flow for highly accurate order picking at Alliance Healthcare' s 56,000 sq ft distribution centre in Exeter.
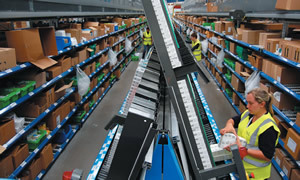
Racking from BITO Storage Systems is playing a key role in maintaining the flow for highly accurate order picking at Alliance Healthcare' s 56,000 sq ft distribution centre in Exeter. BITO has installed a Carton Live Storage (CLS) system to feed both an automated A-Frame picking system and manual pickers building orders for delivery to pharmacies, hospitals and dispensing doctors throughout the south west - twice daily.
Alliance Healthcare' s Exeter Service Centre supplies some 9500 medical product lines and picking has to be quick and accurate. To allow Alliance Healthcare to locate product nearer to where it needs to be picked, BITO integrated its CLS around the picking conveyor loop and A-Frame picker, installed in the new DC by systems integrator Knapp.
The picking process begins when Alliance Healthcare's standalone, company-wide order and delivery system releases orders for picking. It instantly selects the appropriate size tote.
As each tote is barcoded, the system can track them and direct them to the required location. Once despatched onto the transport conveyor, the order's tote goes first to the A-Frame. The tote waits beneath the A-Frame' s dispensing conveyor to receive the fast moving items it requires, which are ejected from the automated picking system.
About 70 per cent of picking at the service centre takes place on the A-Frame; the remaining products are picked manually. Orders requiring products from the A-Frame only are taken directly to despatch. If other items are required for the order, the tote continues to the two manual picking areas: one aisle for medium speed goods, where products are picked directly from the CLS and another aisle for slower goods where products are picked from both CLS and BITO shelving.
When the tote arrives in these areas on the transport conveyor it gets pushed off at the appropriate station onto the picking conveyor, which runs beneath the CLS pick face on one side of each of these aisles.
The picker, wearing a wristmounted scanner with an LCD screen, scans the bin and pick information is displayed on the scanner' s screen, enabling quick and accurate location of the correct product on the flow shelves.
Once picked the tote is scanned again to let the system know the pick is finished at that location.
It goes back to the transport conveyor and continues to the next station. Once the order is complete it goes to despatch where it is put on the required delivery vehicle.
Alliance Healthcare' s Exeter Service Centre supplies some 9500 medical product lines and picking has to be quick and accurate. To allow Alliance Healthcare to locate product nearer to where it needs to be picked, BITO integrated its CLS around the picking conveyor loop and A-Frame picker, installed in the new DC by systems integrator Knapp.
The picking process begins when Alliance Healthcare's standalone, company-wide order and delivery system releases orders for picking. It instantly selects the appropriate size tote.
As each tote is barcoded, the system can track them and direct them to the required location. Once despatched onto the transport conveyor, the order's tote goes first to the A-Frame. The tote waits beneath the A-Frame' s dispensing conveyor to receive the fast moving items it requires, which are ejected from the automated picking system.
About 70 per cent of picking at the service centre takes place on the A-Frame; the remaining products are picked manually. Orders requiring products from the A-Frame only are taken directly to despatch. If other items are required for the order, the tote continues to the two manual picking areas: one aisle for medium speed goods, where products are picked directly from the CLS and another aisle for slower goods where products are picked from both CLS and BITO shelving.
When the tote arrives in these areas on the transport conveyor it gets pushed off at the appropriate station onto the picking conveyor, which runs beneath the CLS pick face on one side of each of these aisles.
The picker, wearing a wristmounted scanner with an LCD screen, scans the bin and pick information is displayed on the scanner' s screen, enabling quick and accurate location of the correct product on the flow shelves.
Once picked the tote is scanned again to let the system know the pick is finished at that location.
It goes back to the transport conveyor and continues to the next station. Once the order is complete it goes to despatch where it is put on the required delivery vehicle.
MORE FROM THIS COMPANY
OTHER ARTICLES IN THIS SECTION