Home> | Automation | >Conveying components | >Automated bar store streamlines production |
ARTICLE
Automated bar store streamlines production
12 December 2012
Since the beginning of 2011, production efficiency has increased significantly at the hot coiling facility of Hanson Springs in Mellor Street, Rochdale, following the installation of a 25-metre-high storage tower from K
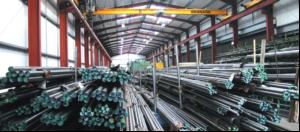
Since the beginning of 2011,
production efficiency has increased
significantly at the hot coiling facility
of Hanson Springs in Mellor Street,
Rochdale, following the installation
of a 25-metre-high storage tower
from Kasto to house the bar from
which the springs are made.
They are used globally for flow control applications in the oil and gas, petrochemical and power generation sectors, all of which are currently buoyant and demanding more springs in faster delivery times.
John Hanson, a director of the company, says: "Whereas it used to take us up to three hours to find material buried at the bottom of conventional racking, bar is now available from the tower within three and a half minutes of calling it up on the computer control screen.
"This is a maximum cycle time; mostly the stock is delivered to the output station much faster.
Previously, we planned our manufacture around bar that was reasonably accessible at any given time. However, if an urgent order came in requiring access to elusive bar, staff had no alternative but to spend time searching for it.
"Using the automated storage and retrieval system, flexibility of production has improved and leadtime is reduced, sometimes dramatically." The typical size of a batch of springs is in the range two- to 50-off, requiring frequent changeover of the coiling plant. Use of this expensive plant is maximised by prompt arrival of cut-to-length steel bar. Fifteen tonnes are processed daily and increased profitability will readily amortise the £1 million investment in the storage tower and associated civil engineering work.
Many additional benefits accrue from enhanced logistics. For example, a 23-ton truck previously took around three hours to unload because the overhead crane progressed with each batch of bar at slower than walking pace along the conventional racking. Stocking the Kasto tower takes 40 minutes - four to five times faster - as the store's input / output station is just inside the door.
Further advantages of the tower store include better security of the raw material, which can only be accessed by PIN code. Another benefit is reduced risk to crane operators, since they less frequently have to reach around bundles of bar on conventional racks to put on lifting straps. Some racks have been retained, however, to store material over 10 metres long - the tower's maximum capacity.
They are used globally for flow control applications in the oil and gas, petrochemical and power generation sectors, all of which are currently buoyant and demanding more springs in faster delivery times.
John Hanson, a director of the company, says: "Whereas it used to take us up to three hours to find material buried at the bottom of conventional racking, bar is now available from the tower within three and a half minutes of calling it up on the computer control screen.
"This is a maximum cycle time; mostly the stock is delivered to the output station much faster.
Previously, we planned our manufacture around bar that was reasonably accessible at any given time. However, if an urgent order came in requiring access to elusive bar, staff had no alternative but to spend time searching for it.
"Using the automated storage and retrieval system, flexibility of production has improved and leadtime is reduced, sometimes dramatically." The typical size of a batch of springs is in the range two- to 50-off, requiring frequent changeover of the coiling plant. Use of this expensive plant is maximised by prompt arrival of cut-to-length steel bar. Fifteen tonnes are processed daily and increased profitability will readily amortise the £1 million investment in the storage tower and associated civil engineering work.
Many additional benefits accrue from enhanced logistics. For example, a 23-ton truck previously took around three hours to unload because the overhead crane progressed with each batch of bar at slower than walking pace along the conventional racking. Stocking the Kasto tower takes 40 minutes - four to five times faster - as the store's input / output station is just inside the door.
Further advantages of the tower store include better security of the raw material, which can only be accessed by PIN code. Another benefit is reduced risk to crane operators, since they less frequently have to reach around bundles of bar on conventional racks to put on lifting straps. Some racks have been retained, however, to store material over 10 metres long - the tower's maximum capacity.
MORE FROM THIS COMPANY
- KASTOecostore entry level metal storage on show at Open House
- Kasto Unitower to star at Mach
- Robotic handling of steel material
- Storage and sawing innovations
- Finding savings
- Productivity boost
- Interest in automation growing
- Storage revamp reduces forklifts used from 15 to six
- Sawing & storage
- Kasto sees promising uptake for high-end automation
OTHER ARTICLES IN THIS SECTION