Home> | Lift trucks | >Warehouse | >Jungheinrich upgrades reach truck |
ARTICLE
Jungheinrich upgrades reach truck
12 December 2012
ETM/ETV 214/216 reach truck now features increased mast lifting and lowering speeds together with improved acceleration Features added to the ETM/ETV 214/216 reach truck are said to deliver overall operational effic
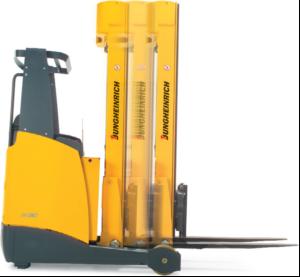
ETM/ETV 214/216 reach truck now
features increased mast lifting and
lowering speeds together with
improved acceleration
Features added to the ETM/ETV 214/216 reach truck are said to deliver overall operational efficiency gains of 10% while energy consumption during a typical shift has been reduced by 10%.
The lift height of the new truck has been raised to 10.7 metres which allows racking with a shelf height of up to 10.5m to be serviced. The truck can lift loads up to 1,600kg while the new model's residual capacity has also been increased so the truck can now lift loads up to 1,000kg to heights of over 10m.
The truck has been designed to operate within the narrowest aisles. The mast is positioned between the support arms which means that a counterweight is not required and the truck can work in aisles as narrow as 2,711mm. A comparable electric counterbalance truck requires an aisle width of more than 3.2m.
To further aid operational efficiency, improvements to the overhead load guard give the driver a clear view of the fork tips and racking surfaces which means loads can be quickly and easily picked up and deposited safely - even high up in the racking.
The operator also benefits from the new truck's larger cockpit and can adjust his or her sitting position for maximum comfort.
The main operating elements are all easily accessible and control pedals are arranged in the automotive style that the operator will be familiar with.
The truck also features a position control system which ensures easy and quick stacking at previously defined storage heights. Load sensors on the truck recognise whether a pallet is at the correct height for put-away or the forks are raised to the appropriate height when retrieving a pallet. This feature means that potentially costly errors during the put-away and retrieval within the storage cube are avoided.
To ensure that the operator does not exceed the weight limit, the truck also features an operation control system which continuously measures the load weight via sensors and synchronises it with the respective lift height of the truck. The driver receives both a visual and audible warning if the truck's residual capacity is exceeded.
Features added to the ETM/ETV 214/216 reach truck are said to deliver overall operational efficiency gains of 10% while energy consumption during a typical shift has been reduced by 10%.
The lift height of the new truck has been raised to 10.7 metres which allows racking with a shelf height of up to 10.5m to be serviced. The truck can lift loads up to 1,600kg while the new model's residual capacity has also been increased so the truck can now lift loads up to 1,000kg to heights of over 10m.
The truck has been designed to operate within the narrowest aisles. The mast is positioned between the support arms which means that a counterweight is not required and the truck can work in aisles as narrow as 2,711mm. A comparable electric counterbalance truck requires an aisle width of more than 3.2m.
To further aid operational efficiency, improvements to the overhead load guard give the driver a clear view of the fork tips and racking surfaces which means loads can be quickly and easily picked up and deposited safely - even high up in the racking.
The operator also benefits from the new truck's larger cockpit and can adjust his or her sitting position for maximum comfort.
The main operating elements are all easily accessible and control pedals are arranged in the automotive style that the operator will be familiar with.
The truck also features a position control system which ensures easy and quick stacking at previously defined storage heights. Load sensors on the truck recognise whether a pallet is at the correct height for put-away or the forks are raised to the appropriate height when retrieving a pallet. This feature means that potentially costly errors during the put-away and retrieval within the storage cube are avoided.
To ensure that the operator does not exceed the weight limit, the truck also features an operation control system which continuously measures the load weight via sensors and synchronises it with the respective lift height of the truck. The driver receives both a visual and audible warning if the truck's residual capacity is exceeded.
MORE FROM THIS COMPANY
- Making best use of space
- Jungheinrich wins contract to build logistics centre
- £6 million short term rental fleet investment
- Jungheinrich UK Systems & Projects division appoints business development manager
- Jungheinrich UK plans to build new facility in the North
- Kombi Stacker will do two shifts on one charge
- Market forces
- Rolling stock
- Jungheinrich presents integrated solutions at LogiMAT 2017
- Driverless vehicle handles pallets
OTHER ARTICLES IN THIS SECTION