ARTICLE
Showing how it's done
12 December 2012
Clipper Logistics has deployed innovative handling solutions to provide value for clients at its new portcentric hub in the North East, which will open later this year. The company's head of portcentric logistics Carl Muir,
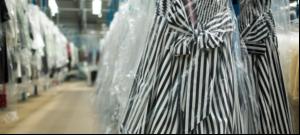
Clipper Logistics has deployed innovative handling solutions to provide value for
clients at its new portcentric hub in the North East, which will open later this year. The
company's head of portcentric logistics Carl Muir, explains how they did it
ClipperLogistics will take its service offering to a new level with a £40 million investment in a purpose-built, cross dock supercentre serving in-store and online channels for multi-users.
Wynyard Park, near Teesport in the north east, will offer portcentric deconsolidation solutions on a new scale when it opens later this year. It's the culmination of years of experience and Clipper believes it's the shape of things to come.
The facility has a footprint of 350,000 sq ft, but with mezzanines the operational space will be well over 1m sq ft.
Clipper's head of portcentric logistics, Carl Muir says there have been a number of lessons learned from operations at the Clipper de-consolidation and e-fulfilment centres of excellence, all of which have been included in the design of Wynyard Park to provide a solution that is both agile and extremely capable.
"The solution has been designed to provide warehouse optimisation and aid team productivity," explains Carl. "The flexibility it will allow is very exciting. We've given a lot of thought to optimising the flow through of products, deploying solutions that give us the benefit of mechanisation with the versatility to change. Our handling solution is designed to meet both current and future challenges arising in the retail environment." As its first customer, Clipper secured a 10 year deal with ASDA to provide portcentric solutions for George, its fashion brand. The solution encompasses receipt, QC, stock management, and a full suite of pre-retail activities - and builds on the work done at Clipper's Darlington deconsolidation centre where it has handled weekly peaks of up to 2 million units for George since 2009.
The new site solution includes a bespoke installation of a three-tier hanging garment mezzanine and hanging conveyors - creating operational space of over 600,000 sq ft.
On boxed intake, extendable boom conveyors provide flexibility and capacity on carton sortation. Cartons are then palletised and moved to gravity roller beds before going through the enhanced processing section of the facility.
"Lighting on the telescopic booms used to unload and load stock will create a safer working environment, and this is also the case inside where there's no crossover between people and machines used to move stock between areas," explains Carl.
Slick rail is used for the enhanced processing and pre-retail elements of the work before being integrated onto a rail and trolley system. This allows greater functionality and integration through the building to either storage location via uplift conveyors or straight through cross dock to outbound.
"One of the benefits of a purpose-designed solution is that we've been able to integrate the enhanced services area into the overall flow, in such a way that stock flows smoothly and efficiently through or around the value-added services," says Carl.
The experienced on-site pre-retail team work in a spacious area equipped with steam tunnels, semi-automatic bagging machines, and hand irons to ensure stock is store-ready before it proceeds to the next stage.
Once the inbound check-in is complete, goods are moved to the appropriate storage areas or they may cross dock the same day to outbound.
"We'll also be using an outer loop to return empty trolleys from the outbound to inbound bays using a chain-driven belt configuration. This will save a significant amount of time and energy spent pushing trolleys." To improve order picking productivity Wynyard Park is fully geared up to provide a multi-channel service, incorporating RF and voice recognition technologies.
The facility has been designed to be able to pick at RDC level or batch level for future upstream storage, which builds upstream storage capacity ahead of the RDCs.
Carl concludes: "The supercentre will operate as a true cross dock facility, helping retailers reduce costs, increase efficiency, reduce lead times and achieve green objectives. This will enable them to expand product ranges and hold larger stocks to ensure 24-hour availability for customers, wherever they choose to buy from. We find this is a must for the multichannel marketplace."
ClipperLogistics will take its service offering to a new level with a £40 million investment in a purpose-built, cross dock supercentre serving in-store and online channels for multi-users.
Wynyard Park, near Teesport in the north east, will offer portcentric deconsolidation solutions on a new scale when it opens later this year. It's the culmination of years of experience and Clipper believes it's the shape of things to come.
The facility has a footprint of 350,000 sq ft, but with mezzanines the operational space will be well over 1m sq ft.
Clipper's head of portcentric logistics, Carl Muir says there have been a number of lessons learned from operations at the Clipper de-consolidation and e-fulfilment centres of excellence, all of which have been included in the design of Wynyard Park to provide a solution that is both agile and extremely capable.
"The solution has been designed to provide warehouse optimisation and aid team productivity," explains Carl. "The flexibility it will allow is very exciting. We've given a lot of thought to optimising the flow through of products, deploying solutions that give us the benefit of mechanisation with the versatility to change. Our handling solution is designed to meet both current and future challenges arising in the retail environment." As its first customer, Clipper secured a 10 year deal with ASDA to provide portcentric solutions for George, its fashion brand. The solution encompasses receipt, QC, stock management, and a full suite of pre-retail activities - and builds on the work done at Clipper's Darlington deconsolidation centre where it has handled weekly peaks of up to 2 million units for George since 2009.
The new site solution includes a bespoke installation of a three-tier hanging garment mezzanine and hanging conveyors - creating operational space of over 600,000 sq ft.
On boxed intake, extendable boom conveyors provide flexibility and capacity on carton sortation. Cartons are then palletised and moved to gravity roller beds before going through the enhanced processing section of the facility.
"Lighting on the telescopic booms used to unload and load stock will create a safer working environment, and this is also the case inside where there's no crossover between people and machines used to move stock between areas," explains Carl.
Slick rail is used for the enhanced processing and pre-retail elements of the work before being integrated onto a rail and trolley system. This allows greater functionality and integration through the building to either storage location via uplift conveyors or straight through cross dock to outbound.
"One of the benefits of a purpose-designed solution is that we've been able to integrate the enhanced services area into the overall flow, in such a way that stock flows smoothly and efficiently through or around the value-added services," says Carl.
The experienced on-site pre-retail team work in a spacious area equipped with steam tunnels, semi-automatic bagging machines, and hand irons to ensure stock is store-ready before it proceeds to the next stage.
Once the inbound check-in is complete, goods are moved to the appropriate storage areas or they may cross dock the same day to outbound.
"We'll also be using an outer loop to return empty trolleys from the outbound to inbound bays using a chain-driven belt configuration. This will save a significant amount of time and energy spent pushing trolleys." To improve order picking productivity Wynyard Park is fully geared up to provide a multi-channel service, incorporating RF and voice recognition technologies.
The facility has been designed to be able to pick at RDC level or batch level for future upstream storage, which builds upstream storage capacity ahead of the RDCs.
Carl concludes: "The supercentre will operate as a true cross dock facility, helping retailers reduce costs, increase efficiency, reduce lead times and achieve green objectives. This will enable them to expand product ranges and hold larger stocks to ensure 24-hour availability for customers, wherever they choose to buy from. We find this is a must for the multichannel marketplace."
MORE FROM THIS COMPANY
- Reliable e-fulfilment
- Clipper takes huge Leeds warehouse due to unprecedented eComm growth
- Switch to flat pack garment supply
- Clipper and Wilko open South Wales warehouse
- Multi channel fulfilment and returns
- Innovative approach to recruitment saves 3PL small fortune
- Hat trick of retail wins for Clipper Logistics
- Mastering returns
- eComm platform extends deal with Clipper
- Clipper open to takeover from GXO
RELATED ARTICLES
- No related articles listed
OTHER ARTICLES IN THIS SECTION