Home> | Lift trucks | >Counterbalance | >A managed service |
ARTICLE
A managed service
12 December 2012
In the fast moving retail environment it is imperative forklift fleets are well managed to reduce ongoing costs, says Toyota Material Handling UK In today's climate it is paramount to minimise cost wherever possible
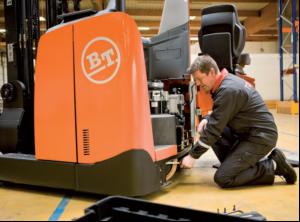
In the fast moving retail environment it is imperative
forklift fleets are well managed to reduce ongoing costs,
says Toyota Material Handling UK
In today's climate it is paramount to minimise cost wherever possible and if companies do not act, they can spiral out of control. A forklift fleet can be a big contributor to cost in the retail supply chain, with unbudgeted costs resulting from poor maintenance, bad driver practice and damage resulting from accidents. In today's 24/7, fast-moving retail environment it is imperative operations are not hindered by any of these factors.
When a supplier is chosen by a retailer, price is important but not all-important.
Sometimes a little additional investment can help to bring down overall costs. This may mean looking at an alternative - a managed service approach such as that offered by Toyota.
Most organisations are running a lean operation and looking to maximise their forklift fleets. In this situation availability is key. When considering a supplier, look for fast, reliable, consistent service. It is also important for multi-site organisations to ensure a high level of support is available consistently throughout the UK.
Accidents happen but equipment damage can have a considerable impact on costs, not just on the repair of the equipment but also on the infrastructure (buildings, racking, product, clean up, downtime, lost sales etc). It can also lead to an unsafe working environment with personnel being injured.
In most industries, a calculation of the actual cost of damage is not made, but we have found it can run to a 10:1 ratio. So if you consider your £500 invoice for the equipment repair being a £5,000 overall cost, then a small investment in managed solutions would be worthwhile.
Toyota is constantly looking to drive down customer costs. This can be achieved through the products and services we bring to market, initiatives that are geared to minimise the lifecycle cost of its equipment to the customer, as well as offering closely managed solutions with advice and support on all aspects of material handling equipment, operator training and service.
In today's climate it is paramount to minimise cost wherever possible and if companies do not act, they can spiral out of control. A forklift fleet can be a big contributor to cost in the retail supply chain, with unbudgeted costs resulting from poor maintenance, bad driver practice and damage resulting from accidents. In today's 24/7, fast-moving retail environment it is imperative operations are not hindered by any of these factors.
When a supplier is chosen by a retailer, price is important but not all-important.
Sometimes a little additional investment can help to bring down overall costs. This may mean looking at an alternative - a managed service approach such as that offered by Toyota.
Most organisations are running a lean operation and looking to maximise their forklift fleets. In this situation availability is key. When considering a supplier, look for fast, reliable, consistent service. It is also important for multi-site organisations to ensure a high level of support is available consistently throughout the UK.
Accidents happen but equipment damage can have a considerable impact on costs, not just on the repair of the equipment but also on the infrastructure (buildings, racking, product, clean up, downtime, lost sales etc). It can also lead to an unsafe working environment with personnel being injured.
In most industries, a calculation of the actual cost of damage is not made, but we have found it can run to a 10:1 ratio. So if you consider your £500 invoice for the equipment repair being a £5,000 overall cost, then a small investment in managed solutions would be worthwhile.
Toyota is constantly looking to drive down customer costs. This can be achieved through the products and services we bring to market, initiatives that are geared to minimise the lifecycle cost of its equipment to the customer, as well as offering closely managed solutions with advice and support on all aspects of material handling equipment, operator training and service.
MORE FROM THIS COMPANY
- Toyota Material Handling drives ‘Think like Toyota’ approach
- 2012 to be 'Year of Safety'for Toyota
- Toyota reports strong lithium-ion take-up
- Toyota hand pallet truck receives design award
- How to best use data
- Low-level order picker launch
- Integrated pre-operational check
- Optimised diesel engine developed
- First-class fleet management
- Picking heights to 12m
OTHER ARTICLES IN THIS SECTION