Home> | Automation | >Picking & sortation | >Sortation for Sainsburys |
Home> | Industry Sector | >Retail/E-tail | >Sortation for Sainsburys |
ARTICLE
Sortation for Sainsburys
21 January 2013
Durkopp Fordertechnik completed a multi million pound system for Sainsbury's at its National Distribution Centre for Clothing in Bedfordshire.
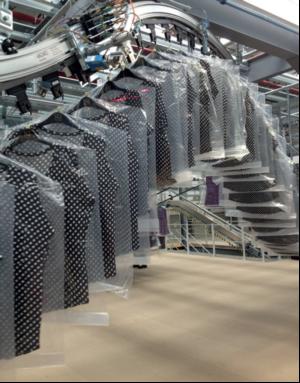
Durkopp Fordertechnik completed a
multi million pound system for
Sainsbury's at its National Distribution
Centre for Clothing in Bedfordshire.
The DC has the capacity to store over 7 million garments, 3.5 million of which are hanging, and currently services 410 Sainsbury's Supermarkets nationwide with clothing.
The system was installed in nine months from receipt of order to commissioning and has 51 kilometres of storage rail and runs 20,000 trolleys.
It is based on the "763" trolley system with each trolley capable of carrying up to 50 items at a time.
On arrival, trucks are rapidly unloaded by using telescopic booms.
Garments are then held in a buffering zone so they can undergo quantity, quality and barcode checks. Garments are then allocated by the WMS / WCS and automatically transported to the correct storage area.
After picking they are separated into three categories - Menswear, Ladieswear and Kidswear in the Presort Buffer and then into stores on two high speed Sortation Systems before being moved to one of 148 Drop-off Lanes for despatch. Both the Pre-sort Buffer and the Sortation Systems are on a mezzanine floor above the despatch bays, allowing maximum use of the site footprint.
Items ready for despatch are taken from trolley in the Drop-off Lanes and loaded on to one of eleven brush conveyors which carry them to the ground floor. The system uses gravity wherever possible so saving energy.
James Osborn, Strategy Manager at Sainsbury's says: "There are always going to be obstacles to overcome but Durkopp did not disappoint, they were professional throughout."
The DC has the capacity to store over 7 million garments, 3.5 million of which are hanging, and currently services 410 Sainsbury's Supermarkets nationwide with clothing.
The system was installed in nine months from receipt of order to commissioning and has 51 kilometres of storage rail and runs 20,000 trolleys.
It is based on the "763" trolley system with each trolley capable of carrying up to 50 items at a time.
On arrival, trucks are rapidly unloaded by using telescopic booms.
Garments are then held in a buffering zone so they can undergo quantity, quality and barcode checks. Garments are then allocated by the WMS / WCS and automatically transported to the correct storage area.
After picking they are separated into three categories - Menswear, Ladieswear and Kidswear in the Presort Buffer and then into stores on two high speed Sortation Systems before being moved to one of 148 Drop-off Lanes for despatch. Both the Pre-sort Buffer and the Sortation Systems are on a mezzanine floor above the despatch bays, allowing maximum use of the site footprint.
Items ready for despatch are taken from trolley in the Drop-off Lanes and loaded on to one of eleven brush conveyors which carry them to the ground floor. The system uses gravity wherever possible so saving energy.
James Osborn, Strategy Manager at Sainsbury's says: "There are always going to be obstacles to overcome but Durkopp did not disappoint, they were professional throughout."
MORE FROM THIS COMPANY
- Dress hire firm orders sortation system from Dürkopp
- Massive garment handling facility for John Lewis
- Clothing retailer installs automated hanging garment storage and retrieval system
- Hanger handling
- Asda upgrades kit at garment NDC
- Sainsbury's revamps garment handling at NDC
- Automating ‘One and Done’
- Hanging loose
- Modular set carrier system
- Next phase completed
OTHER ARTICLES IN THIS SECTION