Home> | Automation | >Automated storage | >Steel processor automates storage |
Home> | Industry Sector | >Manufacturing | >Steel processor automates storage |
Home> | Warehouse Storage | >Racking & shelving | >Steel processor automates storage |
Steel processor automates storage
07 March 2016
Striebel & John processes about 9,500 tonnes of steel sheets a year and wanted consistent automation from sheet metal storage system to final mounting box production.
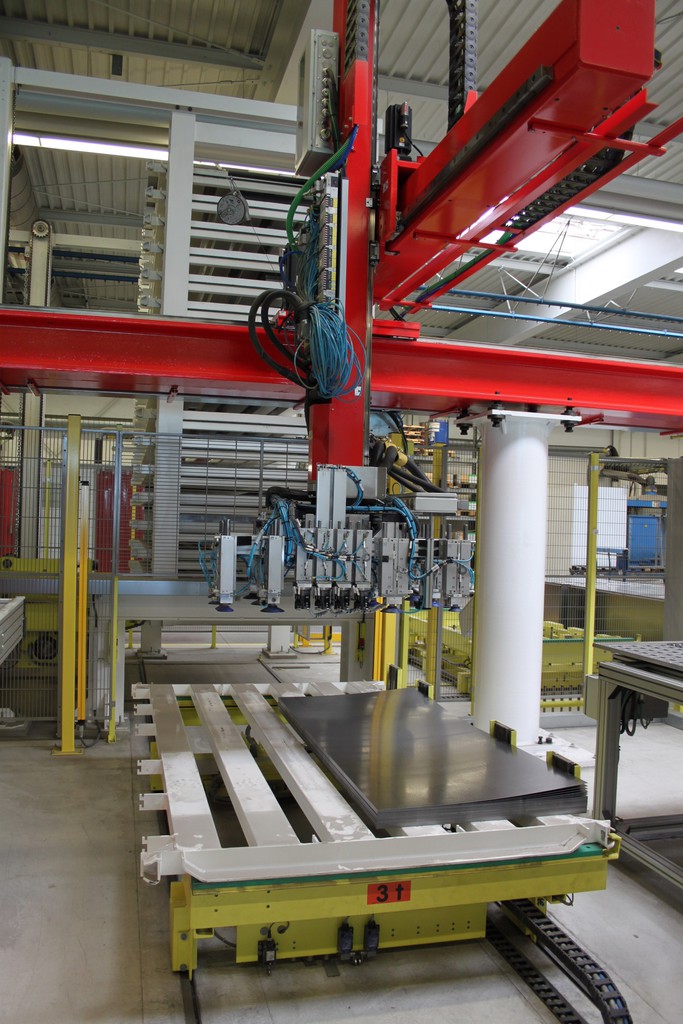
Head of production Roland Schnurr says: “Our customers in the electrical systems wholesale and switchgear production sectors no longer manage storage systems, so we are forced to provide a highly flexible job controlled manufacturing of batch sizes from single batch. This is economically viable only with a certain, very high, yet practical degree of automation."
The processing area is served by a gantry robot system and a Unitower B3.0 automatic sheet metal storage system from KASTO.
The task of the automatic inline storage system is to supply the welding cell with various rear panels. It functions as a buffer and interim storage system that can be supplied externally and inline with parts that are needed either immediately or at a later time. The sheet metal storage system presents a total of 35 pallet storage locations arranged in two blocks that then provide the required quantities of the various rear panel geometries. The pallets are designed for payloads up to 2500 mm long, 1545 mm wide, 130 mm high, and 3 t in weight. The operating gantry crane traverses between the two shelf blocks and handles all of the storage and removal operations. Outside of the cell area downstream of the transverse storage station, it utilises the carriage for the removal and return storage systems.
Inside the welding/gantry robot cell, it utilises the carriage for the longitudinal transfer system. The pallet changeover time from the transfer station to the gantry robot system is 135 seconds, starting from the carriage’s parked position. This 135 second cycle includes the carriage’s traverse into the shelf block, the return of the pallet no longer needed, the retrieval of the requested pallet, and finally the traverse to the position for transfer to the gantry robot system and automatic loading on the changeover table. The 135 second cycle runs parallel to the welding cycles of the robots.To minimise storage and removal times, the operating gantry crane traverses in the hoist at speeds up to 16 m/min, and the push/pull mechanism for the pallets up to 20 m/min.
- KASTOecostore entry level metal storage on show at Open House
- Automated storage key to revamped supply chain
- Finding savings
- Steeled for growth
- Automated bar store streamlines production
- Kasto wins handling safety award
- Energy recovery and storage system
- Automated storage and retrieval of metals on show
- Good as new - it’s retrofit
- Robotic handling of steel material