Home> | Automation | >Automated handling | >Flexibility is top priority for food and drink client |
Home> | Automation | >Automated storage | >Flexibility is top priority for food and drink client |
Home> | Industry Sector | >Food & drink | >Flexibility is top priority for food and drink client |
Flexibility is top priority for food and drink client
11 January 2017
SSI Schaefer has implemented one of the largest and most modern beverage distribution centres in Germany as a general contractor for A. Kempf Getränkegroßhandel GmbH, a subsidiary of Edeka Südwest.
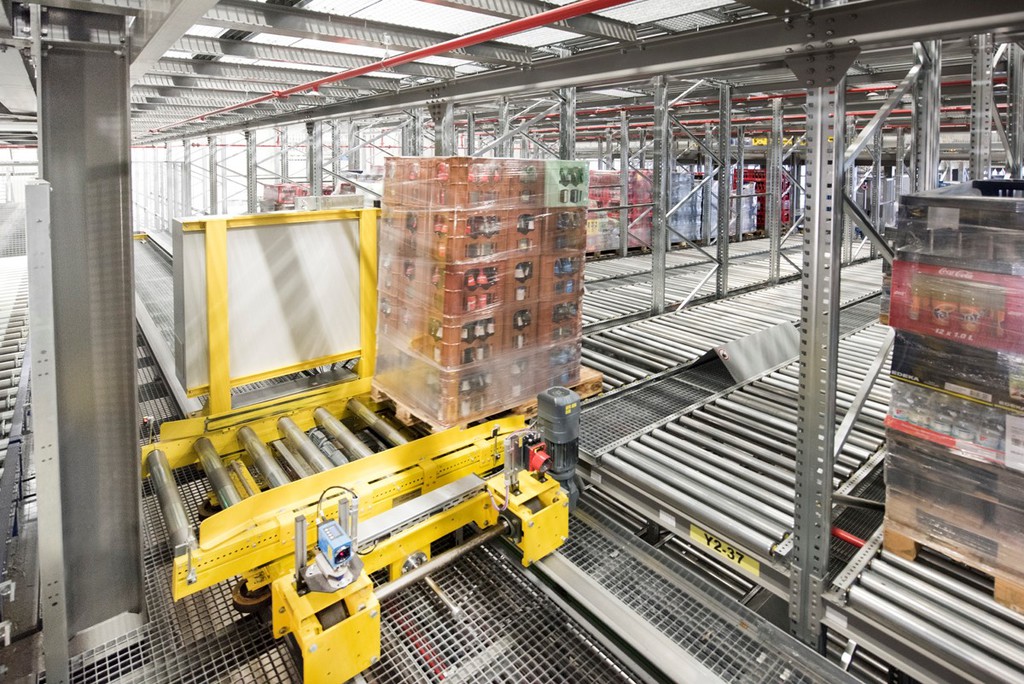
Intelligent control of the flow of goods and a combination of manual and fully automated picking strategies ensures maximum levels of efficiency.
The contract covered all the building construction work, including the outdoor facilities and system engineering, and training for employees.
In the drinks warehouse, the wholesaler handles up to 160,000 full and empty beverage crates every day. To guarantee efficiency in the warehousing and distribution processes, SSI Schaefer has constructed a 17-aisle high bay warehouse (HBW) and a 6-aisle automated miniload system (ASPW) with tray storage locations. An electric monorail system (EMS) is installed above this for internal transport. Gantry robots, which are supplied with whole pallets directly from the HBW, carry out the depalletising and branch-specific assembly of order pallets with fast movers.
Seventeen Exyz storage-retrieval machines from SSI Schaefer, each equipped with an Orbiter load handling device, ensure there are ample capacity reserves for the multi-depth storage in the racking channels of the HBW to respond to seasonal peaks. Based on and controlled by the WAMAS logistics software from SSI Schaefer, complex flows of goods with varying picking strategies have been implemented.
Edeka ordered the goods according to an ABC classification system as part of a profitability analysis. Processes were defined, and the automation potential and its economic effects compared to person-to-goods picking were considered. The most cost-effective solution proved to be a combination of goods-to-person and person-to-goods picking. "As much automation as necessary, as little as possible," emphasises the logistics division manager. "Our highest priority is flexibility, particularly when it comes to changes in the assortment; for instance, flexibility in the classification and corresponding assignment of processes."
Medium movers
To pick the 750 medium-mover beverage products, the lowest level of the racking system in the HBW has been set up as channel storage with 18 picking tunnels and is supplied by the SRMs from behind. At the front of the tunnel, the employees pick the cases manually from pallets onto pallets. SSI Schaefer Project Manager Frank Boberg describes one of the advantages of the solution as follows: "The replenishment locations directly from the HBW and behind the staging units reduce replenishment times". WAMAS generates the picking orders in a route and order-optimised manner – and communicates them to the displays on the picking vehicles via WLAN. Once picking is complete, the employees transfer the order pallets to the conveying system. On their way to the outgoing goods area, the pallets are automatically wrapped in foil and labelled. The same process takes place for order pallets, which are temporarily stored on the staging locations in the HBW ready for dispatch.
The highest degree of automation is used for the 60 fast movers, consistently refillable beverage crates. Recurring processes and minimal differences in the shapes of the beverage crates enable the gantry robots to assemble the order pallets according to the branch's needs in a fully automated manner. The crates on the single-item pallets retrieved from the HBW are automatically depalletised by the gantry robots based on the order and transferred to a conveying section. This transports the cases to the robot cells, where more gantry robots stack them and assemble them onto order pallets according to the branch's needs. Finally, the picked order pallets are transported to the outgoing goods buffer along the EMS.
A special warehouse area has also been constructed to process displays, KEGs and special pallets. In order to be able to respond to changes as flexibly as possible, a conscious decision was made not to use automation for these types of items. Only the supply and removal of stock from this warehouse area has been automated.
- Online retail set for second revolution
- SSI Schaefer acquires Italian automation firm
- Fast and flexible storage & retrieval
- SSI Schaefer expands its Midlands base
- Schaefer high bay racking key to new Unicef DC
- Watching the wage bill
- Containing corrosion
- Huge automated DC being built in Leeds
- Mick Schumacher unveiled as brand ambassador
- Rising to the challenge