ARTICLE
Articulated Efficiency How Bendi articulated trucks could halve your energy costs
12 December 2012
Heating, lighting and maintenance all play their part in the increasing costs of operating a warehouse, as well as the costs of the property and staffing.
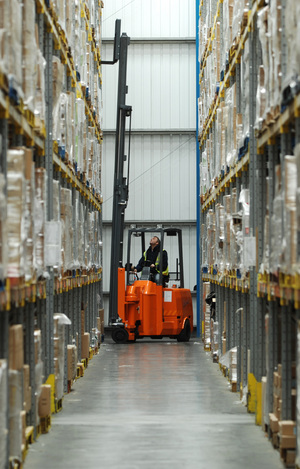
Heating, lighting and maintenance all play their part in the increasing costs of operating a warehouse, as well as the costs of the property and staffing. Under increasing pressure to trim costs warehouse operators are recognising that the space-saving abilities of Bendi articulated trucks are also creating opportunities for significant energy savings compared with premises in which counterbalance, VNA or reach trucks operate.
Warehouses designed for counterbalance or reach trucks in conjunction with adjustable pallet racking (APR) are the least space efficient, with typical aisle widths from 2.8m-4m+ in common use. However, the aisle width is only part of the equation. Turning and loading/unloading space at the ends of the aisles also accounts for 'lost' space.
Fresh air in your warehouse is costing you!
Imagine a 100m x 120m warehouse, 10m high block stacked to the roof with 100,000off 1m tall Chep pallets stacked floor to ceiling. If building, staff and equipment costs come to X£ per month, then the cost per pallet stored is X/100,000 per month. This storage method is utopian and rarely suits real life warehousing in terms of stock rotation, accessibility or the ability of products to support themselves whilst stacked this way. More often than not, product has to be 100% accessible. This is why APR is so prevalent.
Using APR and a standard counterbalance, the building will only store 10,496 pallets (assuming a 4m aisle and counterbalances being limited to about 6m of lift, so the product can only be stacked 4 high allowing for clearances). This is only utilising a miniscule 10% of its total cubic space, leaving 90% as very costly fresh air!
A reach truck, working in a 2.85m aisle but allowing a 15m marshalling/drop area for the counterbalance, because the reach is unsuitable to go outside, will store 20,720 pallets, if stored 7 high. This is almost twice the storage capacity of a standard counterbalance, cutting the storage cost per pallet by almost half - and this is why they are so popular throughout the world.
The next step in efficiency is wire guided VNA's working in 1850mm aisles, with a 7m end of aisle transfer. This solution requires an additional 15m marshalling/drop area for conventional trucks to take pallets to/from the system, so storing 7 high will squeeze in 24,500 racked pallets. This gives 18% more than the warehouse with Reach Trucks.
Bendi saves more space, time and energy
A Bendi working in 1696mm aisles (1600mm is the minimum aisle width) will also store 7 high but only requires a transfer aisle of 2.6m. This configuration achieves 30,680 pallets stored. That's almost 50% more than the reach truck and 25% more than the VNA - therefore offering significantly lower costs.
In fact the Bendi offers the same storage capacity as a warehouse operating counterbalance trucks in just 33% of the space! That makes the warehouse with Bendis a whopping 66% more energy efficient.
Efficient warehousing? We wrote the book
As the pioneer and World's leading manufacturer and supplier of articulated forklift trucks, Translift Bendi has produced a comprehensive guidebook, covering all aspects of articulated truck theory and practice. Entitled 'The Warehouse Revolution', the book is available from Translift Bendi.
Warehouses designed for counterbalance or reach trucks in conjunction with adjustable pallet racking (APR) are the least space efficient, with typical aisle widths from 2.8m-4m+ in common use. However, the aisle width is only part of the equation. Turning and loading/unloading space at the ends of the aisles also accounts for 'lost' space.
Fresh air in your warehouse is costing you!
Imagine a 100m x 120m warehouse, 10m high block stacked to the roof with 100,000off 1m tall Chep pallets stacked floor to ceiling. If building, staff and equipment costs come to X£ per month, then the cost per pallet stored is X/100,000 per month. This storage method is utopian and rarely suits real life warehousing in terms of stock rotation, accessibility or the ability of products to support themselves whilst stacked this way. More often than not, product has to be 100% accessible. This is why APR is so prevalent.
Using APR and a standard counterbalance, the building will only store 10,496 pallets (assuming a 4m aisle and counterbalances being limited to about 6m of lift, so the product can only be stacked 4 high allowing for clearances). This is only utilising a miniscule 10% of its total cubic space, leaving 90% as very costly fresh air!
A reach truck, working in a 2.85m aisle but allowing a 15m marshalling/drop area for the counterbalance, because the reach is unsuitable to go outside, will store 20,720 pallets, if stored 7 high. This is almost twice the storage capacity of a standard counterbalance, cutting the storage cost per pallet by almost half - and this is why they are so popular throughout the world.
The next step in efficiency is wire guided VNA's working in 1850mm aisles, with a 7m end of aisle transfer. This solution requires an additional 15m marshalling/drop area for conventional trucks to take pallets to/from the system, so storing 7 high will squeeze in 24,500 racked pallets. This gives 18% more than the warehouse with Reach Trucks.
Bendi saves more space, time and energy
A Bendi working in 1696mm aisles (1600mm is the minimum aisle width) will also store 7 high but only requires a transfer aisle of 2.6m. This configuration achieves 30,680 pallets stored. That's almost 50% more than the reach truck and 25% more than the VNA - therefore offering significantly lower costs.
In fact the Bendi offers the same storage capacity as a warehouse operating counterbalance trucks in just 33% of the space! That makes the warehouse with Bendis a whopping 66% more energy efficient.
Efficient warehousing? We wrote the book
As the pioneer and World's leading manufacturer and supplier of articulated forklift trucks, Translift Bendi has produced a comprehensive guidebook, covering all aspects of articulated truck theory and practice. Entitled 'The Warehouse Revolution', the book is available from Translift Bendi.
MORE FROM THIS COMPANY
- Life Celebration of Freddy Brown set for Monday
- Bendi at CeMAT: Save space, time and money
- Have your cake and eat it
- Bendi makes key appointments to sales team
- Innovation trumps slumps
- Built on 'beating heart'of R&D
- Translift senior management makes key transition
- Bendi Order Picker goes into full production
- New cold store cab
- Bendi founder Freddy Brown passes away
RELATED ARTICLES
- No related articles listed
OTHER ARTICLES IN THIS SECTION