Home> | Automation | >Picking & sortation | >Racking in frame for success |
ARTICLE
Racking in frame for success
12 December 2012
A BITO solution shows the importance of storage systems in ensuring the success of picking implementations Racking from BITO Storage Systems is playing a key role in maintaining the flow for highly accurate order pick
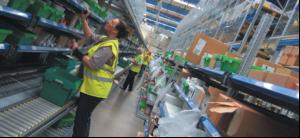
A BITO solution shows the importance
of storage systems in ensuring the
success of picking implementations
Racking from BITO Storage Systems is playing a key role in maintaining the flow for highly accurate order picking at Alliance Healthcare's 56,000 sq ft distribution centre in Exeter. BITO integrated its CLS around the picking conveyor loop and A-Frame picker, installed in the new DC by systems integrator Knapp.
BITO has installed a Carton Live Storage (CLS) system to feed both an automated A-Frame picking system and manual pickers building orders for delivery to pharmacies, hospitals and dispensing doctors throughout the south west - twice daily.
Alliance Healthcare's Exeter Service Centre supplies some 9500 medical product lines and picking has to be quick and accurate.
Moving into the new building in January this year to accommodate a new automated order picking system, the company is now reaping its benefits in terms of accuracy and speed of operation.
The picking process begins when Alliance Healthcare's standalone, company-wide order and delivery system releases orders for picking. It instantly selects the appropriate size tote to avoid having just one item, or a small order, rattling around inside a large tote and causing delivery vehicles to carry lots of empty space.
As each tote is barcoded, the system can track them as they pass readers and direct them to the required location for the items on each order. Once despatched onto the transport conveyor the order's tote goes first to the A-Frame, a unit that comprises rows of dispensing channels holding vertical stacks of the fastest moving products. The tote waits beneath the AFrame's dispensing conveyor to receive the fast moving items it requires, which are ejected from this automated picking system.
About 70 per cent of picking at the Service Centre takes place on the A-Frame; the remaining products are picked manually.
Orders requiring products from the A-Frame only are taken directly to despatch. If other items are required for the order, the tote continues to the two manual picking areas: one aisle for medium speed goods, where products are picked directly from the CLS and another aisle for slower goods where products are picked from both CLS and BITO shelving.
When the tote arrives in these areas on the transport conveyor it gets pushed off at the appropriate station onto the picking conveyor, which runs beneath the CLS pick face on one side of each of these aisles. The picker, wearing a wrist-mounted scanner with an LCD screen, scans the bin and pick information is displayed on the scanner's screen, enabling quick and accurate location of the correct product on the flow shelves. Once picked the tote is scanned again to let the system know the pick is finished at that location. It goes back to the transport conveyor and continues to the next station.
Once the order is complete it goes to despatch where it is put on the required delivery vehicle.
The density of storage provided by CLS allows products in the manual pick areas to be close to hand and each person picks only within a small area, avoiding long, time consuming walks. In the previous facility, this manual pick stock was stored in ten rows of conventional racking, each about 30 metres long. One person would have to walk up and down the aisles picking a single order, which could take up to five minutes to complete. In the new facility it takes a matter of seconds.
BITO's Carton Live Storage also ensures all the picking in the Service Centre has a constant feed. Each of the A-Frame's channels has a separate number and location that corresponds to a position in the flow rack face opposite, allowing stock to be found quickly when the channels are being refilled. As soon as a carton is empty of product, it is removed and a full carton flows down the lane to replace it. The flow racks themselves are replenished from bulk storage locations in pallet racking bays, which are located either above or opposite the feed face of the flow rack. Top selling lines are located where they can be reached by hand at ground level across the aisle to feed the flow lane.
Other lines are lifted down by forklift.
BITO's CLS saves time on putaway, allowing stock to be delivered directly to the shelf; when a pallet comes through goods in, the flow rack is replenished first and the remaining stock is located in nearby bulk storage position. Carton Live Storage gives Alliance the flexibility to store different sizes of cartons as well as fast moving products that won't fit on the A Frame.
Racking from BITO Storage Systems is playing a key role in maintaining the flow for highly accurate order picking at Alliance Healthcare's 56,000 sq ft distribution centre in Exeter. BITO integrated its CLS around the picking conveyor loop and A-Frame picker, installed in the new DC by systems integrator Knapp.
BITO has installed a Carton Live Storage (CLS) system to feed both an automated A-Frame picking system and manual pickers building orders for delivery to pharmacies, hospitals and dispensing doctors throughout the south west - twice daily.
Alliance Healthcare's Exeter Service Centre supplies some 9500 medical product lines and picking has to be quick and accurate.
Moving into the new building in January this year to accommodate a new automated order picking system, the company is now reaping its benefits in terms of accuracy and speed of operation.
The picking process begins when Alliance Healthcare's standalone, company-wide order and delivery system releases orders for picking. It instantly selects the appropriate size tote to avoid having just one item, or a small order, rattling around inside a large tote and causing delivery vehicles to carry lots of empty space.
As each tote is barcoded, the system can track them as they pass readers and direct them to the required location for the items on each order. Once despatched onto the transport conveyor the order's tote goes first to the A-Frame, a unit that comprises rows of dispensing channels holding vertical stacks of the fastest moving products. The tote waits beneath the AFrame's dispensing conveyor to receive the fast moving items it requires, which are ejected from this automated picking system.
About 70 per cent of picking at the Service Centre takes place on the A-Frame; the remaining products are picked manually.
Orders requiring products from the A-Frame only are taken directly to despatch. If other items are required for the order, the tote continues to the two manual picking areas: one aisle for medium speed goods, where products are picked directly from the CLS and another aisle for slower goods where products are picked from both CLS and BITO shelving.
When the tote arrives in these areas on the transport conveyor it gets pushed off at the appropriate station onto the picking conveyor, which runs beneath the CLS pick face on one side of each of these aisles. The picker, wearing a wrist-mounted scanner with an LCD screen, scans the bin and pick information is displayed on the scanner's screen, enabling quick and accurate location of the correct product on the flow shelves. Once picked the tote is scanned again to let the system know the pick is finished at that location. It goes back to the transport conveyor and continues to the next station.
Once the order is complete it goes to despatch where it is put on the required delivery vehicle.
The density of storage provided by CLS allows products in the manual pick areas to be close to hand and each person picks only within a small area, avoiding long, time consuming walks. In the previous facility, this manual pick stock was stored in ten rows of conventional racking, each about 30 metres long. One person would have to walk up and down the aisles picking a single order, which could take up to five minutes to complete. In the new facility it takes a matter of seconds.
BITO's Carton Live Storage also ensures all the picking in the Service Centre has a constant feed. Each of the A-Frame's channels has a separate number and location that corresponds to a position in the flow rack face opposite, allowing stock to be found quickly when the channels are being refilled. As soon as a carton is empty of product, it is removed and a full carton flows down the lane to replace it. The flow racks themselves are replenished from bulk storage locations in pallet racking bays, which are located either above or opposite the feed face of the flow rack. Top selling lines are located where they can be reached by hand at ground level across the aisle to feed the flow lane.
Other lines are lifted down by forklift.
BITO's CLS saves time on putaway, allowing stock to be delivered directly to the shelf; when a pallet comes through goods in, the flow rack is replenished first and the remaining stock is located in nearby bulk storage position. Carton Live Storage gives Alliance the flexibility to store different sizes of cartons as well as fast moving products that won't fit on the A Frame.
MORE FROM THIS COMPANY
RELATED ARTICLES
OTHER ARTICLES IN THIS SECTION